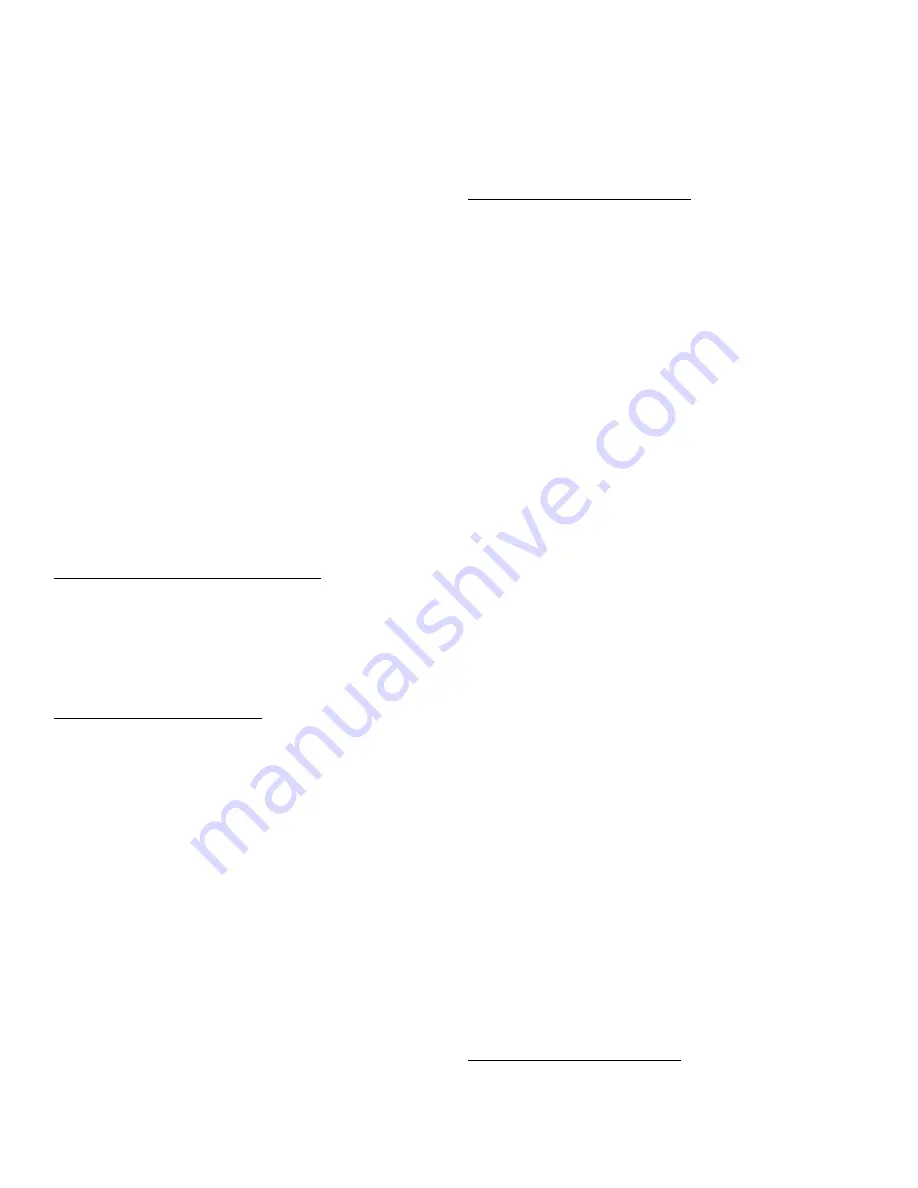
60
The lead chiller responds to normal start/stop controls such
as the occupancy schedule, a forced start or stop, and remote
start contact inputs. After completing start-up and ramp load-
ing, the PIC II evaluates the need for additional capacity. If ad-
ditional capacity is needed, the PIC II initiates the start-up of
the chiller configured at the
LAG ADDRESS
. If the lag chiller
is faulted (in alarm) or is in the OFF or LOCAL modes, the
chiller at the
STANDBY ADDRESS
(if configured) is requested
to start. After the second chiller is started and is running, the
lead chiller monitors conditions and evaluates whether the ca-
pacity has been reduced enough for the lead chiller to sustain
the system alone. If the capacity is reduced enough for the lead
chiller to sustain the
CONTROL POINT
temperatures alone,
then the operating lag chiller is stopped.
If the lead chiller is stopped in CCN mode for any reason
other than an alarm (*) condition, the lag and standby chillers
are also stopped. If the configured lead chiller stops for an
alarm condition, the configured lag chiller takes the lead
chiller’s place as the lead chiller, and the standby chiller serves
as the lag chiller.
The PRESTART FAULT TIMER provides a timeout if
there is a prestart alert condition that prevents a chiller from
starting in a timely manner. If the configured lead chiller does
not complete its start-up before the PRESTART FAULT TIM-
ER (a user-configured value) elapses, then the lag chiller starts,
and the lead chiller shuts down. The lead chiller then monitors
the lag, acting as the lead, for a start request. The
PRESTART
FAULT TIMER
parameter is on the LEADLAG screen, which
is accessed from the EQUIPMENT SERVICE table of the
SERVICE menu.
If the lag chiller does not achieve start-up before the
PRE-
START FAULT TIMER
elapses, the lag chiller stops, and the
standby chiller is requested to start, if configured and ready.
Standby Chiller Configuration and Operation — A chiller is
designated as a standby chiller when its
LEADLAG: CONFIG-
URATION
value on the LEADLAG screen is set to “3.” The
standby chiller can operate as a replacement for the lag chiller
only if one of the other two chillers is in an alarm (*) condition
(as shown on the ICVC panel). If both lead and lag chillers are
in an alarm (*) condition, the standby chiller defaults to oper-
ate in CCN mode, based on its configured occupancy schedule
and remote contacts input.
Lag Chiller Start-Up Requirements — Before the lag chiller
can be started, the following conditions must be met:
1. The lag chiller status indicates it is in CCN mode and is
not in an alarm condition. If the current lag chiller is in an
alarm condition, the standby chiller becomes the active
lag chiller, if it is configured and available.
2. Lead chiller ramp loading must be complete.
3. The configured
LAG STOP TIMER
entry has elapsed.
The
LAG STOP TIMER
starts when the lead chiller ramp
loading is completed or when a lag chiller stops. The
LAG STOP TIMER
entry is on the LEADLAG screen.
4. Lead chiller
ACTIVE DEMAND LIMIT
(see the MAIN-
STAT screen) value must be greater than 95% of full load
amps.
5. Lead chilled water temperature must be greater than the
CONTROL POINT
temperature (see the MAINSTAT
screen) plus 1/2 the
CHILLED WATER DEADBAND
temperature (see the SETUP1 screen).
NOTE: The chilled water temperature sensor may be the
leaving chilled water sensor, the return water sensor, the
common supply water sensor, or the common return wa-
ter sensor, depending on which options are configured
and enabled.
6. Lead chiller temperature pulldown rate (
TEMP PULL-
DOWN DEG/MIN
on the TEMP_CTL screen) of the
chilled water temperature is less than 0.5
F (0.27
C) per
minute for a cumulative duration greater than the PULL-
DOWN TIMER setting in the LEAD/LAG screen.
When all the above requirements have been met, the lag
chiller is commanded to a STARTUP mode (indicated by
“CONTRL” flashing next to the CHILLER START/STOP pa-
rameter in the MAINSTAT screen). The PIC II control then
monitors the lag chiller for a successful start. If the lag chiller
fails to start, the standby chiller, if configured, is started.
Lead/Lag Pulldown Timer Operation — Some lead/lag
chiller applications with large chilled liquid loop volumes must
accommodate intermittent slugs of warm ENTERING
CHILLED WATER for short time periods. This type of tran-
sient condition can result when a control valve rapidly opens to
allow flow through a previously isolated branch or zone within
the chilled liquid system. A PULLDOWN TIMER can be con-
figured to delay starting the lag chiller so it does not excessive-
ly cycle on and off for short time periods when intermittent
slugs of warm ENTERING CHILLED WATER pass through
the chillers. A larger PULLDOWN TIMER entry gives the
warm slug of water more time to pass through the chillers be-
fore the lag chiller can start.
The chiller CONTROL POINT can be configured to either
LEAVING CHILLED WATER or ENTERING CHILLED
WATER temperature. The PIC controls monitor the tempera-
ture pulldown rate of the CHILLED WATER and display the
result as CHILL WATER PULLDOWN/MIN in the
HEAT_EX screen. Samples of the CHILLED WATER tem-
perature are taken once every 10 seconds and compared against
the previous CHILLED WATER sample. A positive value of
CHILL WATER PULLDOWN/MIN indicates that the
CHILLED WATER temperature is decreasing between succes-
sive samples. If CHILL WATER PULLDOWN/MIN rate is a
minimum of 0.5 degrees F per minute then the PULLDOWN:
SATISFIED parameter in the LL_MAINT screen displays
YES, otherwise, the PULLDOWN: SATISFIED parameter
displays NO.
If the lead chiller is unable to achieve the CONTROL
POINT, the lag chiller will not start unless the lead chiller is un-
able to maintain a CHILL WATER PULLDOWN/MIN rate of
0.5 degrees F per minute for a time period equal to the number
of minutes entered in the PULLDOWN TIMER parameter.
PULLDOWN TIME in the LL_MAINT screen displays the re-
maining delay left before the lag chiller is allowed to start
based on the pulldown timer. PULLDOWN TIME will count
down starting at the value entered in PULLDOWN TIMER
under the following conditions:
Ramp Loading is Complete
AND
PULLDOWN: SATISFIED = NO
The lag chiller pulldown start condition is met when PULL-
DOWN TIME lapses to 0.0 min.
If PULLDOWN: SATISFIED changes to YES as the
PULLDOWN TIME is counting down to zero, the PULL-
DOWN TIME will start to count back up provided that the
CHILLED WATER temperature has not fallen to less than the
CONTROL POINT plus one half of the CHILLED WATER
DEADBAND. The PULLDOWN TIME will start to count
back down again should PULLDOWN: SATISFIED change
back to NO. The PULLDOWN TIME will be immediately re-
set to the value entered in the PULLDOWN TIMER parameter
if the CHILLED WATER temperature decreases to less than
the CONTROL POINT plus one half of the CHILLED WA-
TER DEADBAND.
Lag Chiller Shutdown Requirements — The following condi-
tions must be met in order for the lag chiller to be stopped.
1. Lead chiller compressor motor average line current or
load value (
MOTOR PERCENT KILOWATTS
on the
MAINSTAT screen) is less than the lead chiller percent
Содержание AquaEdge 19XR series
Страница 69: ...69 Fig 33 19XR Leak Test Procedures a19 1625 ...
Страница 150: ...150 Fig 62 PIC II Control Panel Wiring Schematic Frame 2 3 4 and E Compressors without Split Ring Diffuser a19 1870 ...
Страница 152: ...152 a19 1871 Fig 63 PIC II Control Panel Wiring Schematic Frame 4 and 5 Compressors with Split Ring Diffuser ...
Страница 154: ...154 Fig 64 Benshaw Inc Wye Delta Unit Mounted Starter Wiring Schematic Low Voltage a19 1873 ...
Страница 161: ...161 Fig 69 Typical Low Voltage Variable Frequency Drive VFD Wiring Schematic 575 v ...
Страница 162: ...162 Fig 69 Typical Low Voltage Variable Frequency Drive VFD Wiring Schematic 575 v cont ...
Страница 163: ...163 Fig 69 Typical Low Voltage Variable Frequency Drive VFD Wiring Schematic 575 v cont a19 1880 ...
Страница 176: ...176 CONTINUED ON NEXT PAGE Fig 71 Typical Medium Voltage Variable Frequency Drive VFD Wiring Schematic cont a19 2064 ...
Страница 186: ...186 APPENDIX B LEAD LAG WIRING 19XR Lead Lag Schematic Series Cooler Flow a19 1655 ...
Страница 187: ...187 APPENDIX B LEAD LAG WIRING cont 19XR Lead Lag Schematic Parallel Cooler Flow a19 1717 ...