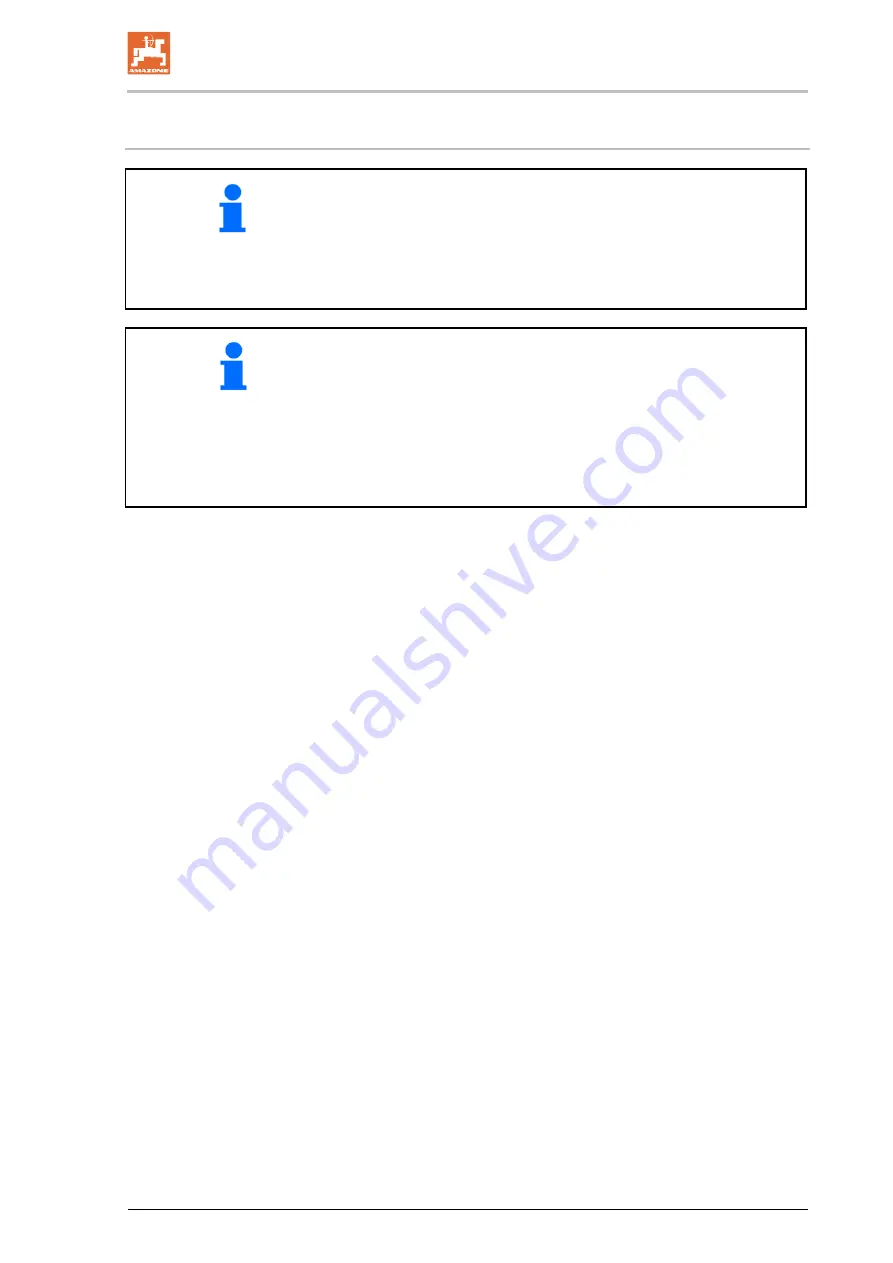
Start-up
EDX 9000-TC BAH0048-6 09.2019
101
6.1.1
Calculating the actual values for the total tractor weight, tractor axle loads
and load capacities, as well as the minimum ballast
The permissible total tractor weight, specified in the vehicle
documentation, must be greater than the sum of the
tractor tare weight
ballast weight and
total weight of the attached implement or drawbar load of the
hitched implement.
This note applies only to Germany.
If, having tried all possible alternatives, it is not possible to comply
with the axle loads and/or the permissible total weight, then a survey
by an officially recognised motor traffic expert can, with the approval
of the tractor manufacturer, be used as a basis for the responsible
authority to issue an exceptional approval according to § 70 of the
German Regulations Authorising the Use of Vehicles for Road Traffic
and the required approval according to § 29, paragraph 3 of the
German Road Traffic Regulations.
Содержание EDX 9000-TC
Страница 27: ...General Safety Instructions EDX 9000 TC BAH0048 6 09 2019 27 Fig 3 Fig 4...
Страница 212: ...Cleaning maintenance and repairs 212 EDX 9000 TC BAH0048 6 09 2019 Fig 304 Fig 305 Fig 306 Fig 307 Fig 308 Fig 309...
Страница 243: ...Hydraulic diagram EDX 9000 TC BAH0048 6 09 2019 243 Fig 346...
Страница 244: ...Hydraulic diagram 244 EDX 9000 TC BAH0048 6 09 2019...
Страница 245: ...Notes EDX 9000 TC BAH0048 6 09 2019 245 14 Notes Space for your notes...