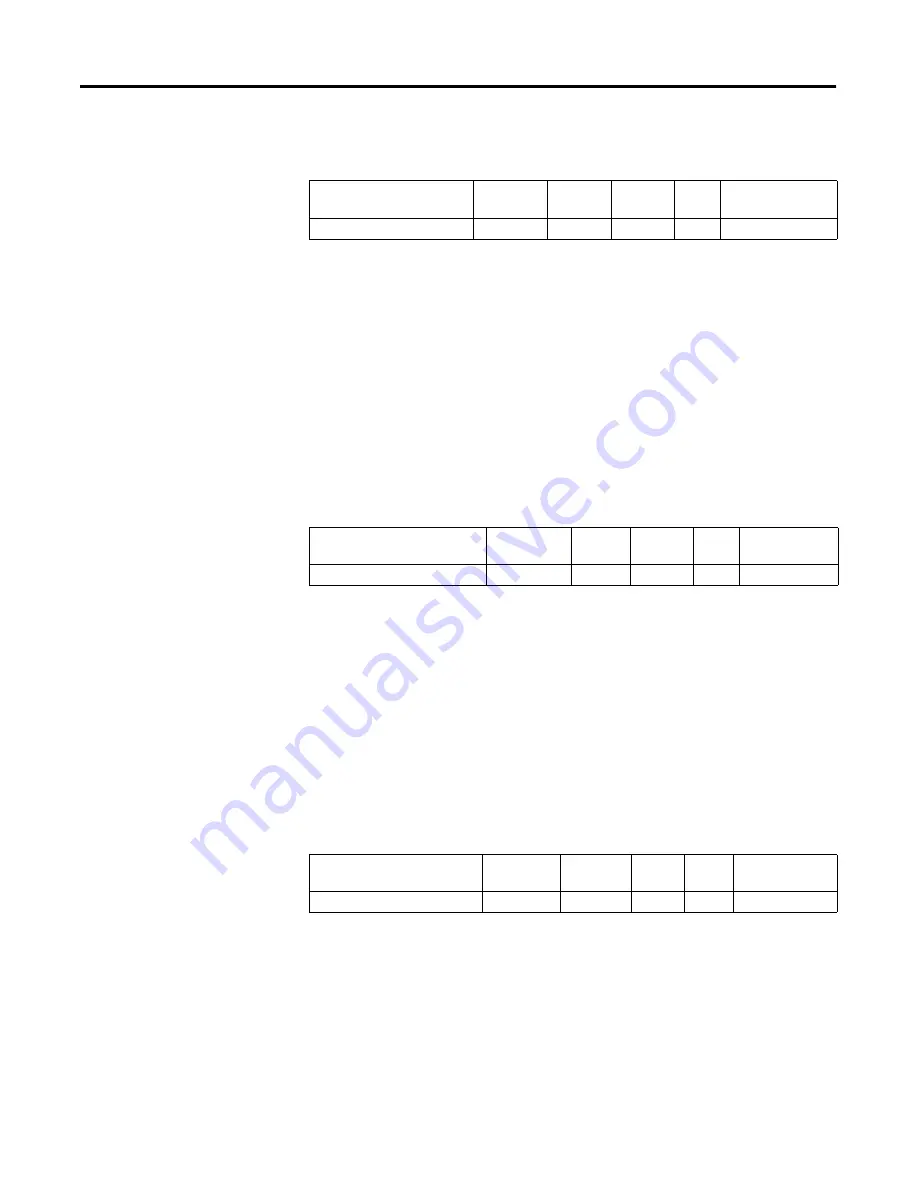
Publication 1763-RM001C-EN-P - October 2009
Using High-Speed Outputs
155
PWM Error Detected (ED)
The PWM ED (Error Detected) bit is controlled by the PWM sub-system. It
can be used by an input instruction on any rung within the control
program to detect when the PWM instruction is in an error state. If an
error state is detected, the specific error is identified in the error code
register (PWM:0.ER).
•
Set (1) - Whenever a PWM instruction is in an error state.
•
Cleared (0) - Whenever a PWM instruction is not in an error state.
PWM Normal Operation (NS)
The PWM NS (Normal Operation) bit is controlled by the PWM
sub-system. It can be used by an input instruction on any rung within the
control program to detect when the PWM is in its normal state. A normal
state is defined as ACCEL, RUN, or DECEL with no PWM errors.
•
Set (1) - Whenever a PWM instruction is in its normal state.
•
Cleared (0) - Whenever a PWM instruction is not in its normal state.
PWM Enable Hard Stop (EH)
The PWM EH (Enable Hard Stop) bit stops the PWM sub-system
immediately. A PWM hard stop generates a PWM sub-system error.
•
Set (1) - Instructs the PWM sub-system to stop its output modulation
immediately (output off = 0).
•
Cleared (0) - Normal operation.
Element Description
Address
Data
Format
Range
Type
User Program
Access
ED - PWM Error Detection
PWM:0/ED bit
0 or 1
status read only
Element Description
Address
Data
Format
Range
Type
User Program
Access
NS - PWM Normal Operation
PWM:0/NS
bit
0 or 1
status read only
Element Description
Address
Data
Format
Range
Type
User Program
Access
EH - PWM Enable Hard Stop
PWM:0/EH
bit
0 or 1
control read/write
efesotomasyon.com - Allen Bradley,Rockwell,plc,servo,drive