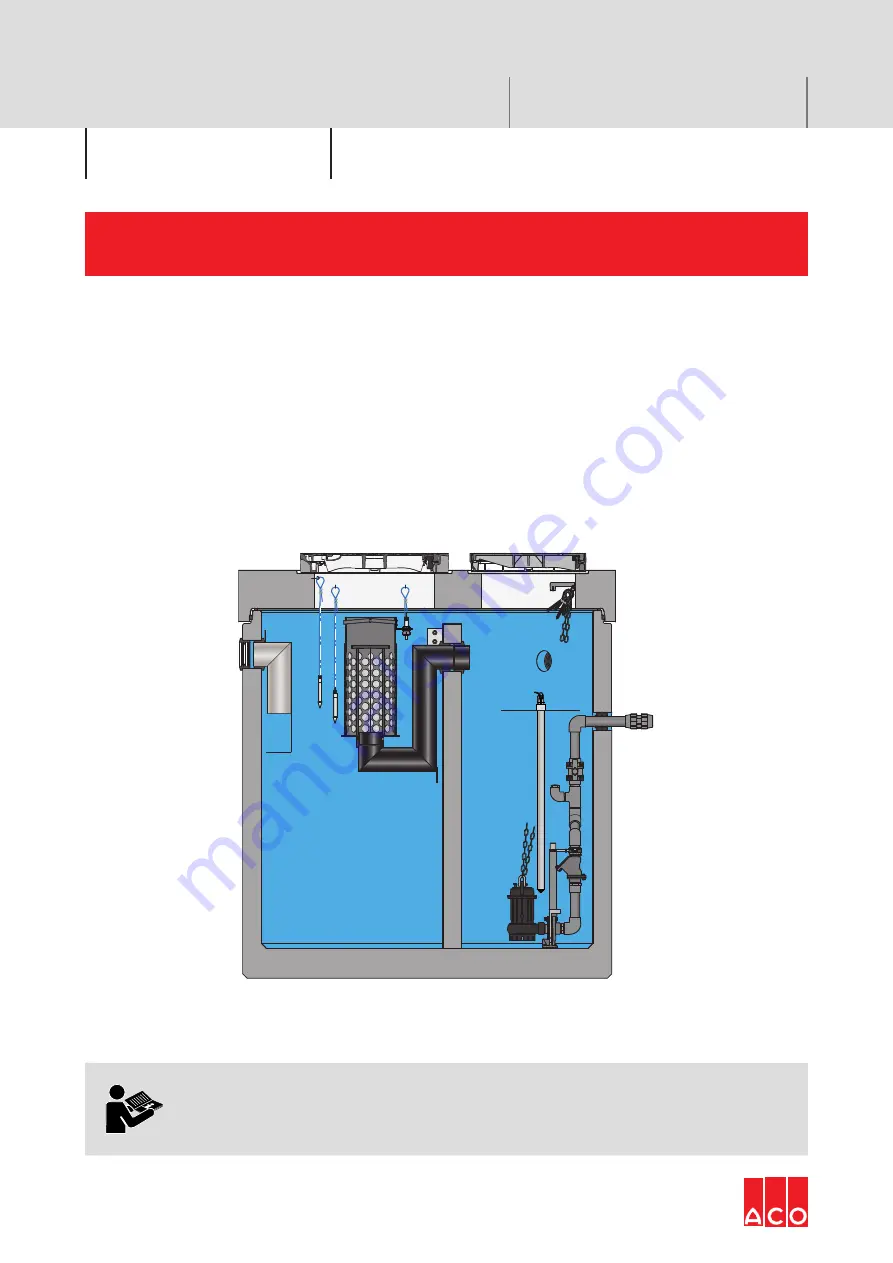
ACO Tiefbau
Instructions for Use
For safe and proper use, read carefully through the instructions for use and all other
documents enclosed with the product, pass them on to the end user and keep them until the
end of the product’s life.
The German version of the instructions for use is definitive.
Issued: 2020-08-11
V0.3_DE Original instructions for use
Light liquid separator (separator class I according to DIN EN
858-1 in conjunction with DIN 1999-100 and DIN 1999-101) with
integrated sludge trap, integrated sampler, integrated pump
station for backflow protection and warning system for locking
the submerged pumps, for underground installation
Oleolift-C