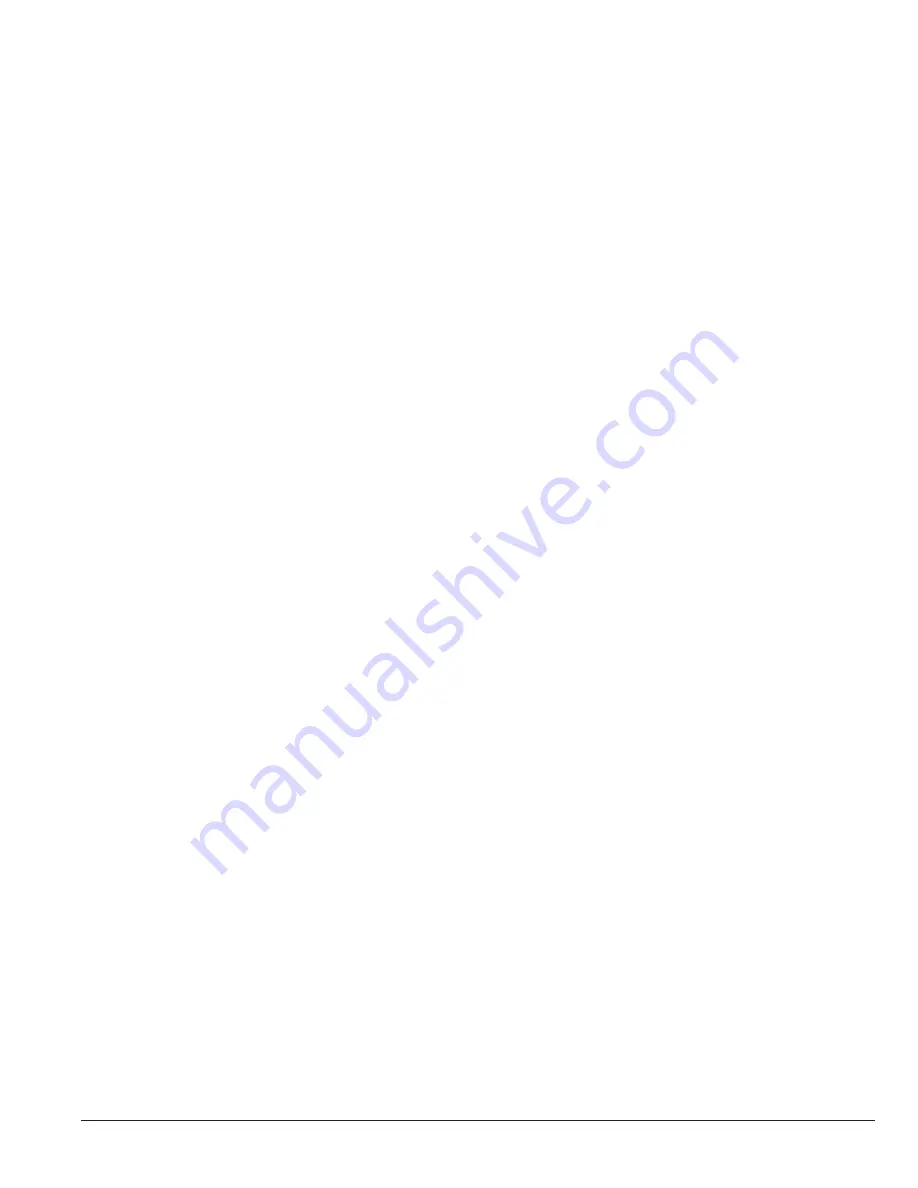
Control Wiring 6-1
3AXD50000011888
Chapter 6
Control Wiring
This section outlines the basics of the control wiring for the N5350. Sample wiring diagrams are shown later in this
guide.
6.1 Motor Thermostat
RPM AC permanent magnet cooling tower motors are provided with thermostats in the stator windings that operate should
the motor overheat. The thermostats are dry contacts designed to provide a closed (short) circuit when the motor is at a safe
temperature and an open circuit should the motor overheat. Dedicated connections are provided for a series connection
of these leads within the N5350. All N5350 drives must be used with motor overtemperature sensing
by correctly connecting the RPM AC cooling tower motor thermostats to the XD24-1 and XD24-2 terminals. The terminal
designations for the motor thermostat connections are XD24-1 and XD24-2 within the N5350. The thermostat
wiring between the motor and the control must be run in a conduit separate from the motor power leads to avoid noise
related problems with the system.
6.2 Digital Inputs
The N5350 is supplied with 9 digital inputs for controlling the cooling tower fan. The connections for these
digital inputs are made on terminals XD24, XD10 and XDI. XDIO-1 & 2 terminals are dedicated to trickle current and de-ice
enable inputs and cannot be changed. XDI-6 is shipped as an External Trip input as discussed in the next section and it is
recommended that this not be changed. The definitions of inputs on XDI-1 through XDI-5 are determined by the selected
operating mode of the drive. Operating mode selection is used to easily select a pre-configured setup of the drive thus
minimizing the programming required to commission the control. The available operating modes are described later in this
guide.
The digital inputs are shipped as “active high” (NPN) inputs. This means that an input signal is true when it is connected
to XD24-4 (Internal 24VDC Source). Conversely, the digital inputs can be set up to be “active high” inputs. In this case, an
input signal is true or when it is connected to the +24VDC power of a customer provided power source that is being used to
control the digital inputs.
Switch J6 on the control board are used to set up the digital inputs. If the inputs are to be controlled as “active high”
signals utilizing the internal supply of the N5350, then no changes to the jumpers will be required. To set up the
digital inputs for other methods of control, reference Figure 6-2 for the jumper settings and the connections required to the
customer supplied inputs and power source.
Содержание ACS880+N5350
Страница 1: ... ABB INDUSTRIAL DRIVES ACS880 N5350 cooling tower drives User s guide ...
Страница 32: ...Terminal Specifications 4 7 3AXD50000011888 Figure 4 3 Cable Conduit Installation R6 R7 R8 R9 ...
Страница 193: ...13 20 Troubleshooting 3AXD50000011888 ...
Страница 201: ...B 2 Dimensions 3AXD50000011888 Figure B 1 Frame R1 IP21 UL Type 1 Frame R1 IP21 UL Type 1 3AUA0000097621 ...
Страница 202: ...Dimensions B 3 3AXD50000011888 Figure B 2 Frame R2 IP21 UL Type 1 Frame R2 IP21 UL Type 1 3AUA0000097691 ...
Страница 203: ...B 4 Dimensions 3AXD50000011888 Figure B 3 Frame R3 IP21 UL Type 1 Frame R3 IP21 UL Type 1 3AUA0000097847 ...
Страница 206: ...Dimensions B 7 3AXD50000011888 Figure B 6 R6 IP21 UL Type 1 Frame R6 IP21 UL Type 1 3AUA0000098321 ...
Страница 207: ...B 8 Dimensions 3AXD50000011888 Figure B 7 Frame R7 IP21 UL Type 1 Frame R7 IP21 UL Type 1 3AUA0000073149 ...
Страница 208: ...Dimensions B 9 3AXD50000011888 Figure B 8 Frame R8 IP21 UL Type 1 Frame R8 IP21 UL Type 1 3AUA0000073150 ...
Страница 209: ...B 10 Dimensions 3AXD50000011888 Figure B 9 Frame R9 IP21 UL Type 1 Frame R9 IP21 UL Type 1 3AUA0000073151 ...
Страница 211: ...C 2 CE Guidelines 3AXD50000011888 Figure C 1 Declaration of Conformity ...
Страница 212: ...CE Guidelines C 3 3AXD50000011888 ...
Страница 244: ...Ethernet IP Setup G 3 3AXD50000011888 3 Click on New Module 4 Select Module Type ETHERNET MODULE ...
Страница 246: ...Ethernet IP Setup G 5 3AXD50000011888 8 The ACS880 CTD Drive is now added to the PLC I O ...