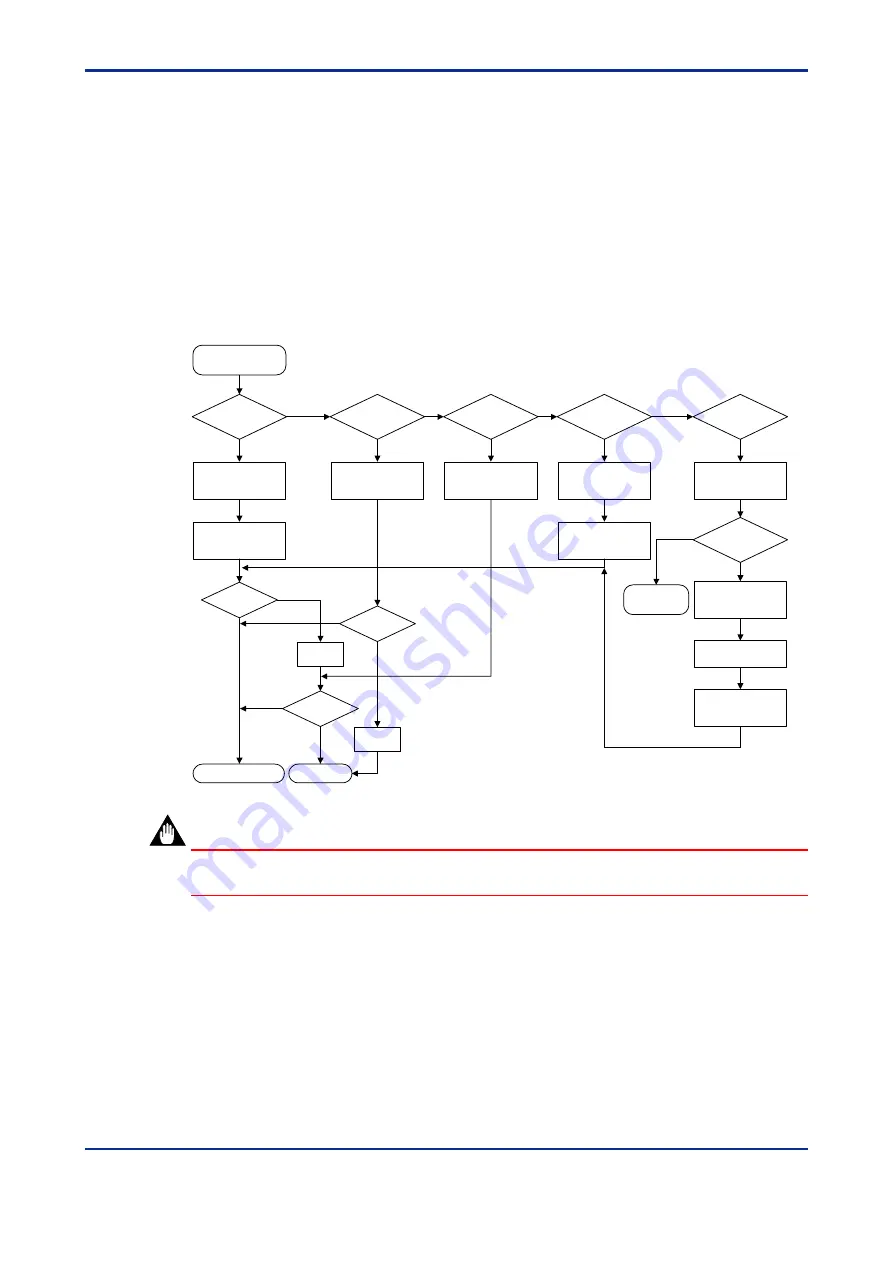
<Toc>
<5. Troubleshooting and Maintenance>
5-1
IM 05E01B02-41E
5.
Troubleshooting and Maintenance
5.1
Troubleshooting
■
Troubleshooting Flow
If the operating display does not appear after turning on the controller’s power, follow the
measures in the procedure below.
If a problem appears complicated, contact our sales representative.
Ask the vendor for repair.
Find the cause.
Totally
inoperable?
Yes
Yes
Yes
No
No
No
Is key
operation
faulty?
Yes
No
Yes
Check wiring on the
power supply
terminals.
Check the key lock
setting.
Is display
faulty?
Yes
No
Turn off power, and
then turn it on
again.
Is I/O
signal faulty?
Yes
No
Check the
instrument’s I/O
specifications.
Check the supply
voltage.
Check the specifications
of I/O counterpart for
wrong polarity.
Check the
communication-related
parameters.
Check the specifications
of communication
counterpart.
Check
communication wiring.
Is
communication
link faulty?
No
Does the code
include a communication
option?
Yes
Normal?
Is
key lock
enabled?
Check the
instrument's suffix
code.
Yes
No
Correct?
Correct the
error(s).
Disable
key lock.
No communication
capability.
Is the instrument
defective?
IMPORTANT
Take note of the parameter settings when asking the vendor for repair.
1st Edition : May 31,2000-00
Summary of Contents for UP750
Page 2: ...Blank Page...
Page 22: ...Blank Page...
Page 120: ...Blank Page...
Page 128: ...Blank Page...
Page 130: ...Blank Page...