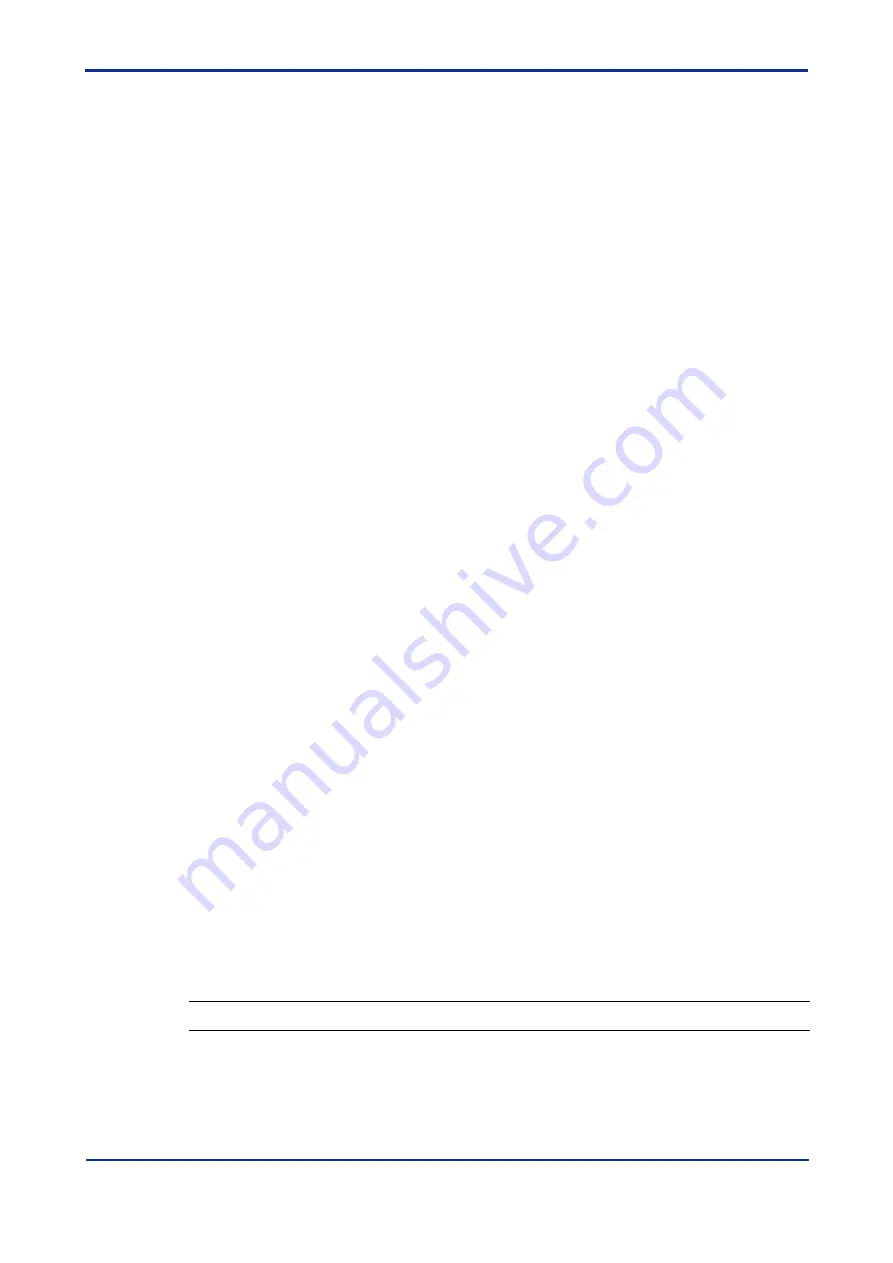
< PART – C Operation and Maintenance >
C-11
IM 39J06B40-01EN
14th Edition: May 30, 2022
3. Determine the wavenumber
The wavenumber is the Raman shift wavenumber (per cm) of the sensor optical
fiber and is related to how Raman scatter intensity changes with sensor optical
fiber temperature. The DTSX3000 can calculate the wavenumber using two-point
temperature calibration parameters (T1, T1’, T2, T2’). Here T1 and T2 denote the
thermometer readings at two points along a section of the sensor optical fiber in
question, and T1’ and T2’ denote the temperatures measured with DTSX3000
before calibration (with Calibration OFF). Based on these parameters, the
wavenumber is calculated using the wavenumber calculation tool of the DTSX3000
Control Visualization Software. In this case, the DTSX3000 Control Visualization
Software uses the internal data of the DTSX3000 to perform wavenumber
calculation so you must run the program on a PC connected to the DTSX3000 via
a LAN. The error in the calculated wavenumber varies inversely with the
temperature difference between T1 and T2 so you should maximize the
temperature difference between T1 and T2 to cover the expected temperature
measurement range as much as possible.
In high temperature measurement range applications, temperature calibration often
cannot be carried out at such high temperatures. In such cases, relatively small
errors can still be achieved even for temperatures 100°C to 200°C higher than the
calibration temperature by using a wavenumber which is 1 to 1.5
%
the
wavenumber calculated using the above tool.
A wavenumber must be determined for each section. However, for optical fibers
from the same lot from the same manufacturer, the same value determined for any
one section can be used for other sections.
4. Calibration
Finally, you need to configure parameters (T1, T1’) for single-point temperature
calibration to correct for optical switch and splice loss. T1 denotes the temperature
reading of a reference thermometer while T2 is the temperature measured by
DTSX3000 before calibration (in Calibration OFF state). The T1 and T1’ values
acquired at the time of wavenumber determination can be used without
modification. These values must be measured for each section and entered as
temperature calibration parameters for that section.
The T1 and T1’ values vary with the arrangement of the sensor optical fiber and
splice loss. They also vary for single-ended measurement and double-ended
measurement. Even in double-ended measurement, the T1 and T1’ values vary
depending on whether you have selected to determine the total differential loss
between the Stokes and anti-Stokes light over the full sensor optical fiber length
automatically using a uniform temperature section or simply using a fixed value.
For these reasons, recalibration is required if there is any change in the
measurement method, connection method, sensor optical fiber arrangement, etc.
In particular, if a significant temperature measurement error is discovered for a
sensor optical fiber segment of known temperature, splice loss change is
suspected. In such a case, we recommend performing recalibration.
C2.2.2.
Temperature Correction
Temperature correction refers to correction processing of DTSX3000 temperature
measurement data using linear correction coefficients. We do not recommend using the
correction function in DTSX3000, which is provided only for downward compatibility
considerations.
SEE ALSO
For details on correction , see Section B7.3.3, “Calibration.”
Summary of Contents for DTSXL
Page 2: ...Blank Page...
Page 15: ...Copyright and Trademark Notices xiii IM 39J06B40 01EN 14th Edition May 30 2022 Blank Page...
Page 23: ...IM 39J06B40 01EN 14th Edition May 30 2022 Blank Page...
Page 83: ...IM 39J06B40 01EN 14th Edition May 30 2022 Blank Page...
Page 215: ...PART B Software B 132 IM 39J06B40 01EN 14th Edition May 30 2022...
Page 222: ...PART B Software B 139 IM 39J06B40 01EN 14th Edition May 30 2022...
Page 233: ...PART B Software B 150 IM 39J06B40 01EN 14th Edition May 30 2022...
Page 239: ...PART B Software B 156 IM 39J06B40 01EN 14th Edition May 30 2022...
Page 247: ...PART B Software B 164 IM 39J06B40 01EN 14th Edition May 30 2022...
Page 253: ...IM 39J06B40 01EN 14th Edition May 30 2022 Blank Page...
Page 289: ...IM 39J06B40 01EN 14th Edition May 30 2022 Blank Page...