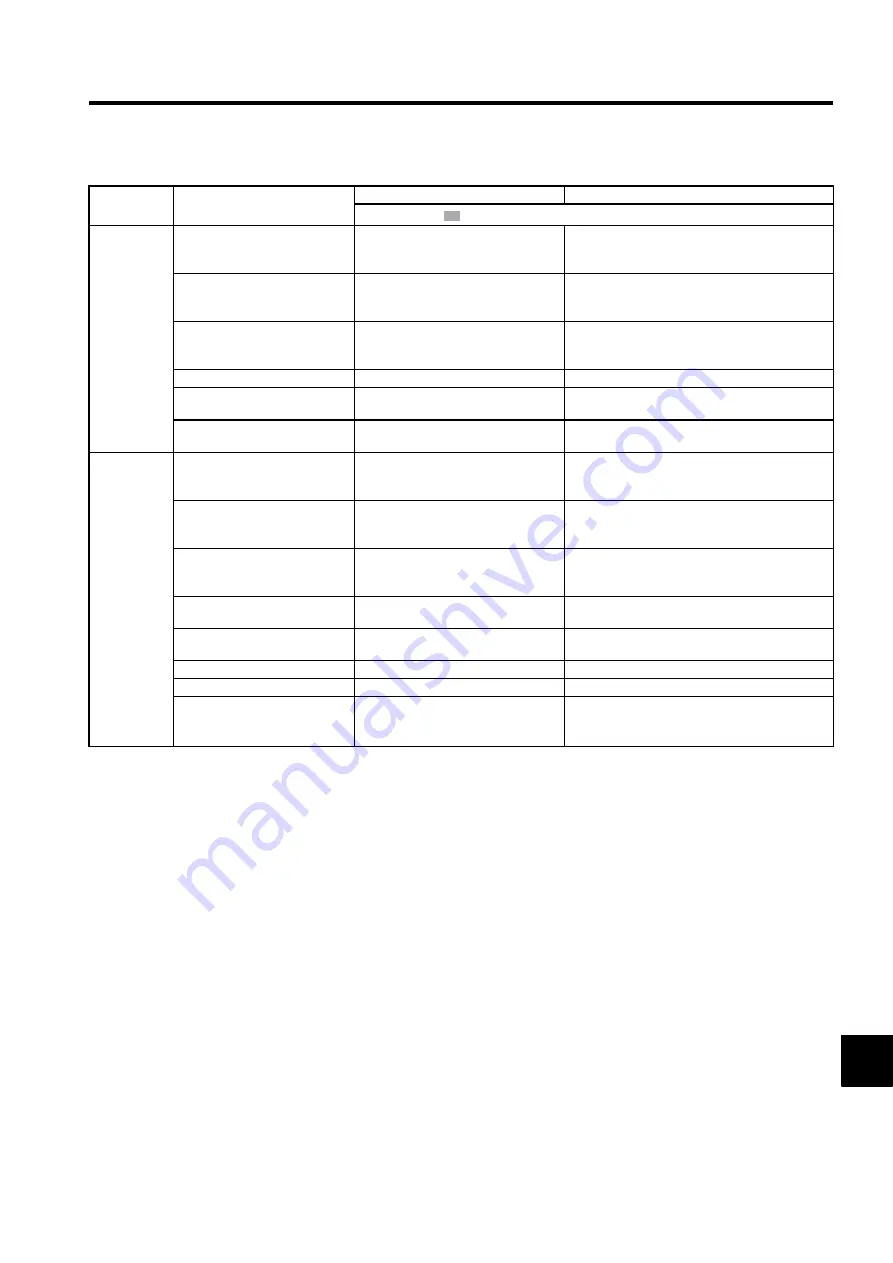
11.1 Troubleshooting
11-19
11
Servomotor
Vibrates at
about 200 to
400 Hz
Speed loop gain value (Pn100) too
high.
Factory setting: Kv=40.0 Hz
Refer to
9.3.2 Operating Procedure in
Speed Control Mode (Pn000 = n.
0
)
.
Reduce speed loop gain (Pn100) preset value.
Position loop gain value (Pn102) too
high
Factory setting: Kp=40.0/s
Refer to
9.3.2 Operating Procedure in
Speed Control Mode (Pn000 = n.
0
)
.
Reduce position loop gain (Pn102) preset value.
Incorrect speed loop integral time
constant (Pn101) setting
Factory setting: Ti=20.00 ms
Refer to
9.3.2 Operating Procedure in
Speed Control Mode (Pn000 = n.
0
)
.
Correct the speed loop integral time constant (Pn101)
setting.
Mass ratio data is incorrect.
Check the setting of Pn103 (Mass Ratio).
Correct the setting of Pn103 (Mass Ratio).
When the autotuning is used: Incor-
rect mass ratio data setting
Check the setting of Pn103 (Mass Ratio).
Correct the setting of Pn103 (Mass Ratio).
When the autotuning is used: Incor-
rect machine rigidity setting
Check the setting of Fn001 (Machine Ridig-
ity Setting).
Correct the setting of Fn001 (Machine Ridigity Setting).
High
Speed
Overshoot on
Starting and
Stopping.
Speed loop gain value (Pn100) too
low
Factory setting: Kv=40.0 Hz
Refer to the gain adjustment in User’s Man-
ual.
Reduce the speed loop gain (Pn100) preset value.
Position loop gain value (Pn102) too
high
Factory setting: Kp=40.0/s
Refer to the gain adjustment in User’s Man-
ual.
Reduce the position loop gain (Pn102) preset value.
Incorrect speed loop integral time
constant (Pn101) setting
Factory setting: Ti=20.00 ms
Refer to the gain adjustment in User’s Man-
ual.
Correct the speed loop integral time constant (Pn101)
setting.
When the autotuning is used: Incor-
rect mass ratio data
Check the setting of Pn103 (Mass Ratio).
Correct the setting of Pn103 (Mass Ratio).
When the autotuning is not used:
Incorrect machine rigidity setting
Check the setting of Fn001 (Machine Ridig-
ity Setting).
Correct the setting of Fn001 (Machine Ridigity Setting).
Mass ratio data is incorrect.
Check the setting of Pn103 (Mass Ratio).
Correct the setting of Pn103 (Mass Ratio).
The force reference is saturated.
Check the force reference wave form.
Use the mode switch function.
The force limit (Pn483, Pn484) is set
to the initial value.
Initial value of force limit:
Pn483 = 30%
Pn484 = 30%
Set a appropriate value for Pn483 and Pn484 (Force
Limit).
Table 11.7 Troubleshooting for Malfunction without Alarm Display (Cont’d)
Symptom
Cause
Inspection
Corrective Actions
: Turn OFF the servo system before executing operations.
Summary of Contents for SGLFW
Page 270: ...9 3 9...