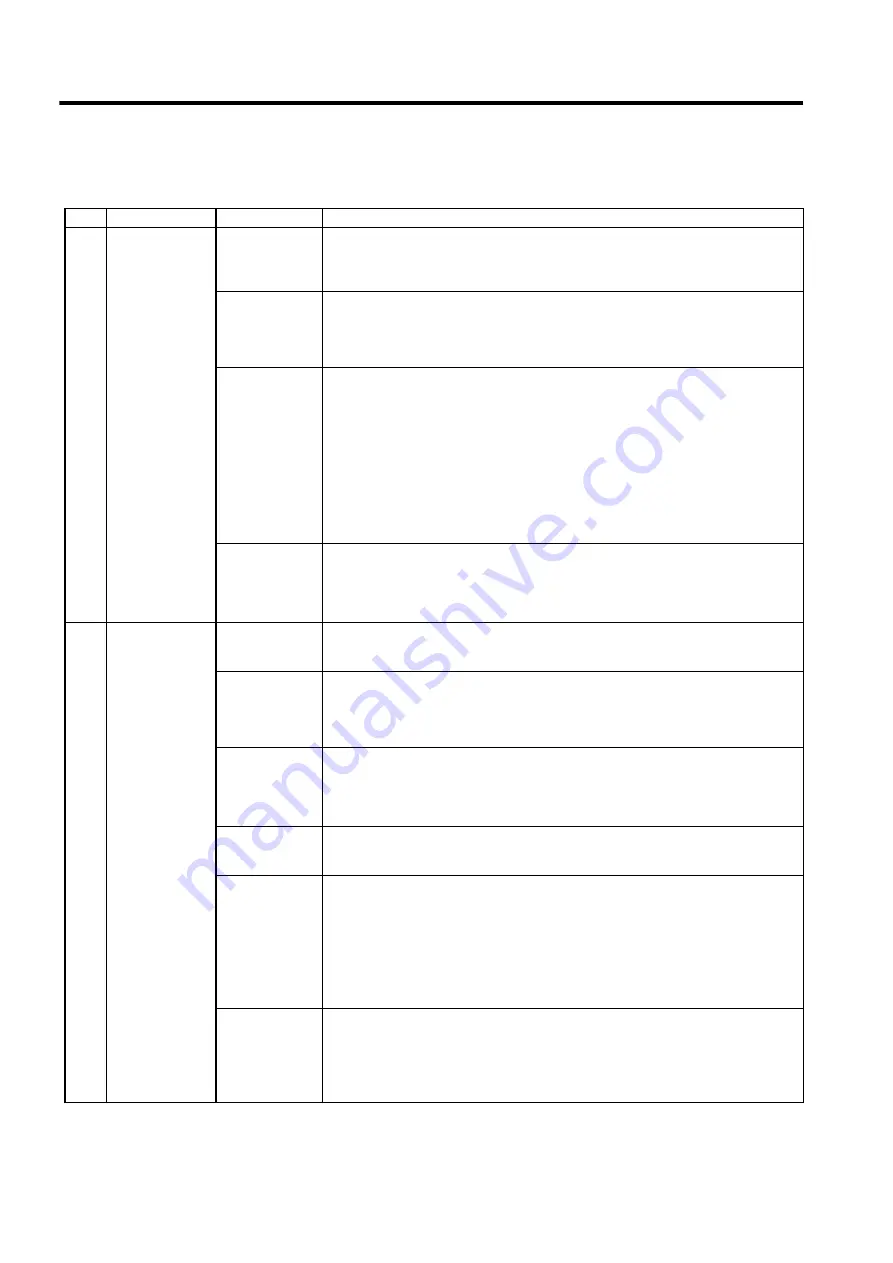
9 Operation
9.2.3 Setup Procedure Using Linear Servomotors without Hall Sensors
9-20
(d) Troubleshooting for Polarity Detection Errors
Refer to the following table for troubleshooting if polarity detection is not completed normally.
No.
Problem
Cause
Countermeasure
1
The linear
servomotor
does not move
during polarity
detection
(speed
feedback is 0).
Polarity
detection is not
being
performed.
Check whether the status display is
P-dt
when the /S-ON (/P-DET) signal is input.
If
P-dt
is not displayed, check whether the parameters for input signal selection Pn50A
and Pn50D are set correctly, and check whether signal input is being performed cor-
rectly.
A force limit is
activated.
To prevent danger during setup, the SGDH SERVOPACK’s factory settings for the
force limit parameters are 30%.
Check the set values for Pn483 and Pn484, and change to a user-set value if the setting
is initial value. Increase the value to the maximum value if no particular restrictions are
required.
The mechanical
friction is large.
When the mechanical friction is relatively larger than the linear servomotor’s rated
force (10% or more), the linear servomotor may stop operating during polarity detec-
tion if factory settings are used.
First, check whether the mass ratio (Pn103) is set correctly.
If Pn103 is set correctly, increase the value set for polarity detection speed loop gain
(Pn481).
If the load is heavy and the mechanical friction is very large, a large gain will cause an
alarm. The gain cannot be increased under this condition, so reduce the mechanical
friction.
If the mechanical friction cannot be reduced without difficulty and the situation does
not improve even if the gain is reduced, consider using the hall sensor for polarity
detection.
Overtravel
signal is
detected during
polarity
detection.
If the OT signal is detected during polarity detection, polarity detection will be ended
and the status will be returned to previous status.
Before performing polarity detection, move the linear servomotor to a position where
the OT signal is not detected.
2
Polarity
detection error
alarm (A.C5)
has occurred.
Parameter
settings are
incorrect.
The settings for scale pitch (Pn280) and motor phase selection (Pn080.1) may not be
appropriate for the device. Check the linear scale specifications and feedback signal
conditions.
Noise is present
in the scale
signal.
When the detection reference is repeatedly output several times in the same direction,
noise may occur in the scale signal, resulting in malfunction. Check that the FG of the
serial converter unit and linear servomotor is connected to FG of the SERVOPACK,
and that FG of the SERVOPACK is connected to the power supply FG.
Also check that the encoder cable is securely sealed.
The coil
assembly is
being subjected
to an external
force.
If the coil assembly is subjected to an external force such as cable tension, and the
speed feedback is not 0 regardless of a 0 detection reference, polarity detection will be
poor. Reduce the external force and make the speed feedback 0.
The linear scale
precision is
rough.
When the linear scale pitch is 100
µ
m min, the SERVOPACK cannot detect correct
speed feedback.
Use a linear scale with good scale pitch precision (within 40
µ
m is recommended).
Linear
servomotor
traceability for
the polarity
detection
reference is
poor.
When the size of the speed feedback for the polarity detection reference is 2 mm/s max,
detection may be poor.
First, check that the mass ratio (Pn103) is set correctly.
If Pn103 is set correctly, increase the value of polarity detection speed loop gain
(Pn481).
When the load is heavy, a large gain will cause an alarm. The gain cannot be increased
under this condition, so reduce the mechanical friction.
If the mechanical friction cannot be reduced without difficulty, consider using the hall
sensor for polarity detection.
The travel
distance during
polarity
detection has
exceeded 10
mm.
An alarm will occur if the linear servomotor movement distance exceeds 10 mm during
polarity detection. The linear servomotor may have moved during detection for some
reason, so check other causes and take appropriate countermeasures.
Summary of Contents for SGLFW
Page 270: ...9 3 9...