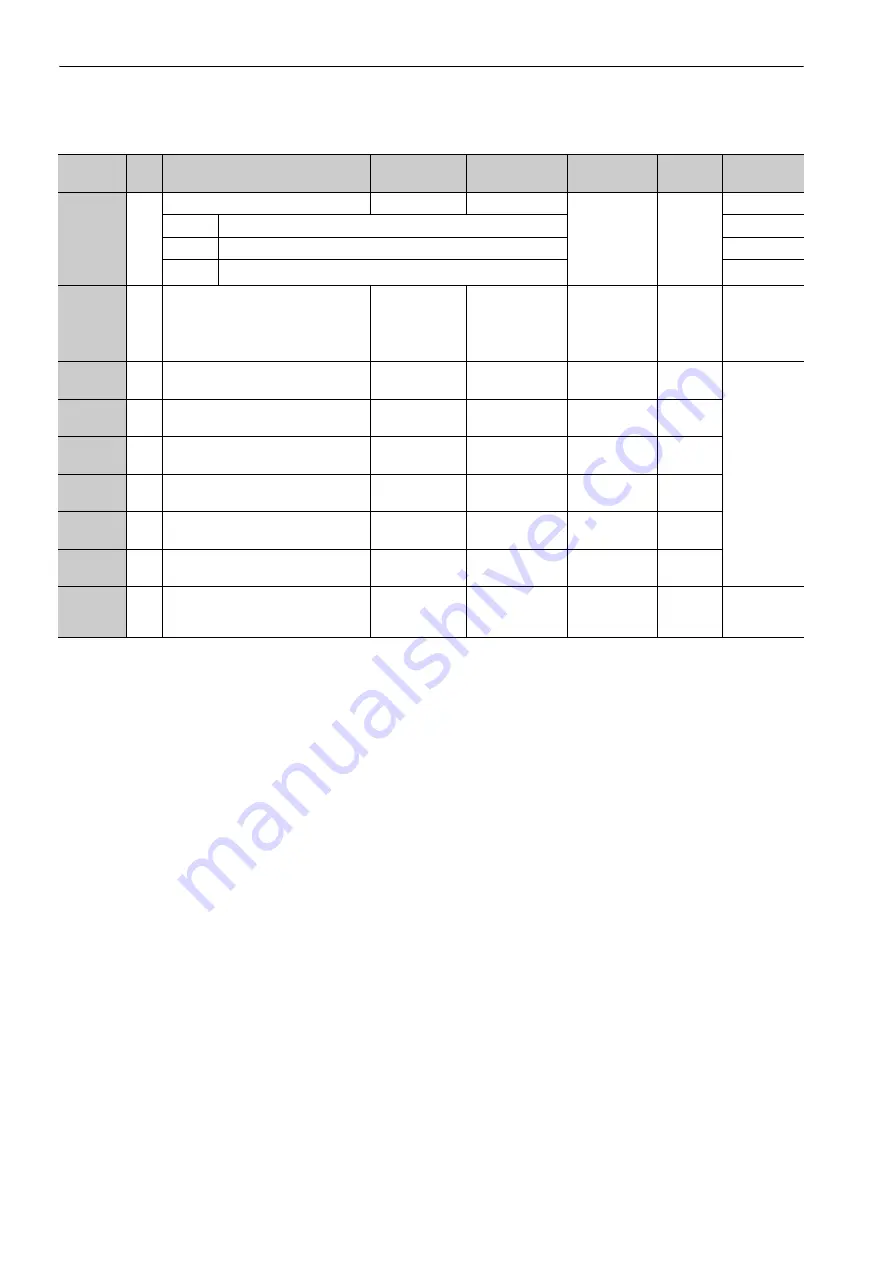
11 Appendix
11.2.2 MECHATROLINK-
III
Common Parameters
11-22
47
PnA8E
4
Torque Unit
1 and 2
–
1
After
restart
0000H
Not supported
0001H
Percentage (%) of rated torque
0002H
Max. torque/40000000H
*4
48
PnA90
4
Torque Base Unit
*4
(Set the value of “n” used as the
exponent in 10
n
when calculating
the Torque Unit (47).)
–5 to 0
–
0
After
restart
61
PnAC2
4
Speed Loop Gain
1000 to
2000000
0.001 Hz
[0.1 Hz]
40000
Immedi-
ately
Adjustment
Related
Parameters
62
PnAC4
4
Speed Loop Integral Time Constant
150 to 512000
μ
s
[0.01 ms]
20000
Immedi-
ately
63
PnAC6
4
Position Loop Gain
1000 to
2000000
0.001/s
[0.1/s]
40000
Immedi-
ately
64
PnAC8
4
Feedforward Compensation
0 to 100
1%
0
Immedi-
ately
65
PnACA
4
Position Loop Integral Time Con-
stant
0 to 5000000
μ
s
[0.1 ms]
0
Immedi-
ately
66
PnACC
4
Positioning Completed Width
0 to
1073741824
1 reference unit
7
Immedi-
ately
67
PnACE
4
NEAR Signal Width
1 to
1073741824
1 reference unit
1073741824
Immedi-
ately
Adjustment
Related
Parameters
∗4.
When 0002H is selected for the Torque Unit (parameter 47), set the Torque Base Unit (parameter 48) to 0.
∗5.
Change the setting when the reference is stopped (DEN is set to 1), because the change will affect the output during
operation.
Note: When using parameters that are enabled after restarting the SERVOPACK, a CONFIG command must be input or
the power must be turned OFF and then ON again.
(cont’d)
Parameter
No.
Size
Name
Setting Range
Units
[Resolution]
Factory
Setting
When
Enabled
Classifica-
tion