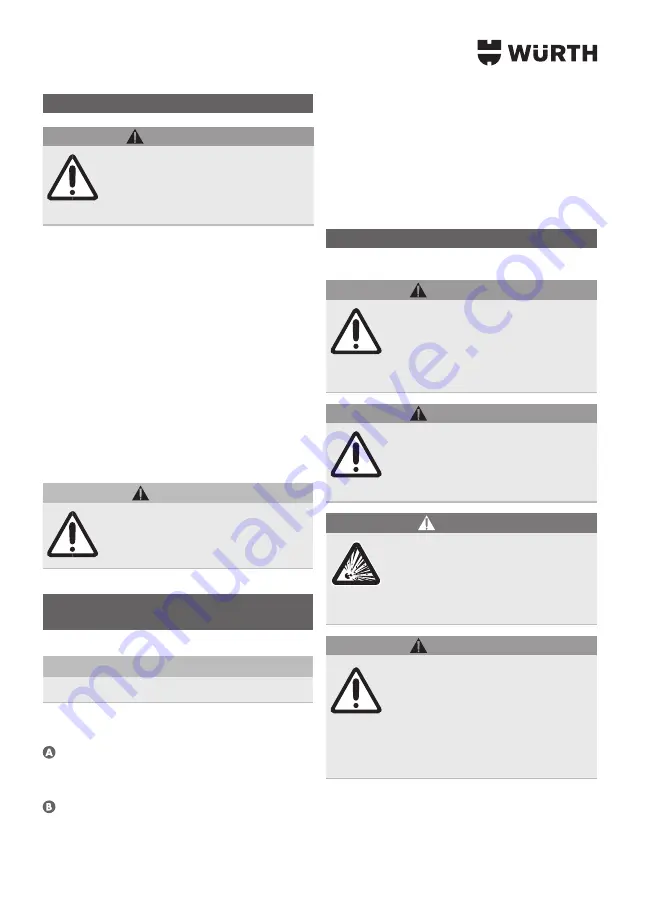
22
▸
Lock the spindle.
▸
Tighten the clamping nut in clockwise direction
using the two-hole wrench
[5]
.
Loosening the clamping nut
▸
Lock the spindle.
▸
Unscrew the clamping nut
[6]
in anti-clockwise
direction using the two-hole wrench
[5]
.
Operation
Switching ON/OFF
WARNING !
Risk of severe injuries.
¾
Always guide the machine with both
hands.
¾
First switch on, then bring the
attachment into contact with the
workpiece.
WARNING !
Danger of unintentional starting
¾
Always switch off the machine when
the mains plug is removed from the
plug socket or if a power failure has
occurred.
DANGER!
Risk of a dust explosion.
¾
Take care to prevent the machine
from drawing in additional dust and
chips.
¾
Keep away from dust deposits when
switching the machine ON and OFF.
WARNING !
Risk of severe injuries.
Â
If the machine is set to continuous
running, it will continue to run if it is
torn out of your hand.
¾
Always hold the machine with both
hands at the handles provided, take
up a stable posture and concentrate
on the work in hand.
Attaching grinding wheel
WARNING !
Risk of severe injuries.
¾
Pull the mains plug out of the plug
socket before all tooling operations.
¾
The machine must be switched off
and at a standstill.
Locking spindle
▸
Press in spindle locking knob
[12]
and turn the
spindle by hand until the spindle locking knob
audibly engages.
Fitting abrasive wheel or disc
▸
Push supporting flange
[10]
onto the spindle.
3
It is fitted correctly when it cannot be turned on
the spindle.
▸
Push abrasive wheel
[7]
onto the supporting
flange
[10]
.
• The grinding wheel must rest uniformly on the
supporting flange.
• The sheet metal flange of cut-off wheels must rest
on the supporting flange.
CAUTION!
Risk of severe injuries
¾
For safety reasons, always use the
safety guard when working with
cutting wheels.
Tightening/loosening the clamping
nut (Fig. I/III)
Tightening the clamping nut
Attention!
The 2 sides of the clamping nut
[6]
are different.
▸
Screw the clamping nut onto the spindle as
follows:
With thin grinding wheels
• The collar of the clamping nut
[6]
faces upwards
so that the thin grinding wheel can be securely
clamped.
With thick grinding wheels
• The collar of the clamping nut
[6]
faces down
-
wards so that the clamping nut can be securely
screwed onto the spindle.
Summary of Contents for EWS 8-115 Light
Page 3: ...3 I 11 6 12 3 1 2 4 5 8 7 9 10...
Page 4: ...12 4 III II 9 13...
Page 115: ...115 GR Adolf W rth GmbH Co KG 3 3 1...
Page 116: ...116 a b c d e f g h i j...
Page 117: ...117 k l m n o p a b c d e a b...
Page 118: ...118 c d e f a b c d e f a a b...
Page 119: ...119 FI FI P2 FI 30 mA...
Page 121: ...121 W rth II 1 2 3 4 5 6 7 8 9 10 11 12 13 2 II 3 4 mm 13 9 3 3 8...
Page 122: ...122 6 5 6 5 12 10 3 3 7 10 I III 2 6 6...
Page 123: ...123 1 1 30 40 W rth...
Page 195: ...195 BG Adolf W rth GmbH Co KG 3 3 1...
Page 196: ...196 a b c d e f g h i j...
Page 197: ...197 k l m n o p a b c d e a b...
Page 198: ...198 c d e f a b c d e f a a b...
Page 199: ...199 FI FI P2 30 mA...
Page 201: ...201 W rth I 1 2 3 4 5 6 7 8 9 10 11 12 13 2 3 4 mm 13 9 3 3 8...
Page 202: ...202 6 5 6 5 12 10 3 3 7 10 2 6 6...
Page 203: ...203 1 1 30 40 W rth...
Page 235: ...235 RU Adolf W rth GmbH Co KG 3 3 1...
Page 236: ...236 a b c d e f g h i j...
Page 237: ...237 k l m n o p a b c d e a b...
Page 238: ...238 c d e f a b c d e f a a b...
Page 239: ...239 FI P2 30 A...
Page 241: ...241 W rth I II 1 2 3 4 5 6 7 8 9 10 11 12 13 2 II 3 4 13 9 3 3 8...
Page 242: ...242 6 5 6 5 12 10 3 3 7 10 I III 6 6...
Page 243: ...243 1 1 30 40 W rth...
Page 265: ...265...
Page 266: ...266...
Page 267: ...267...