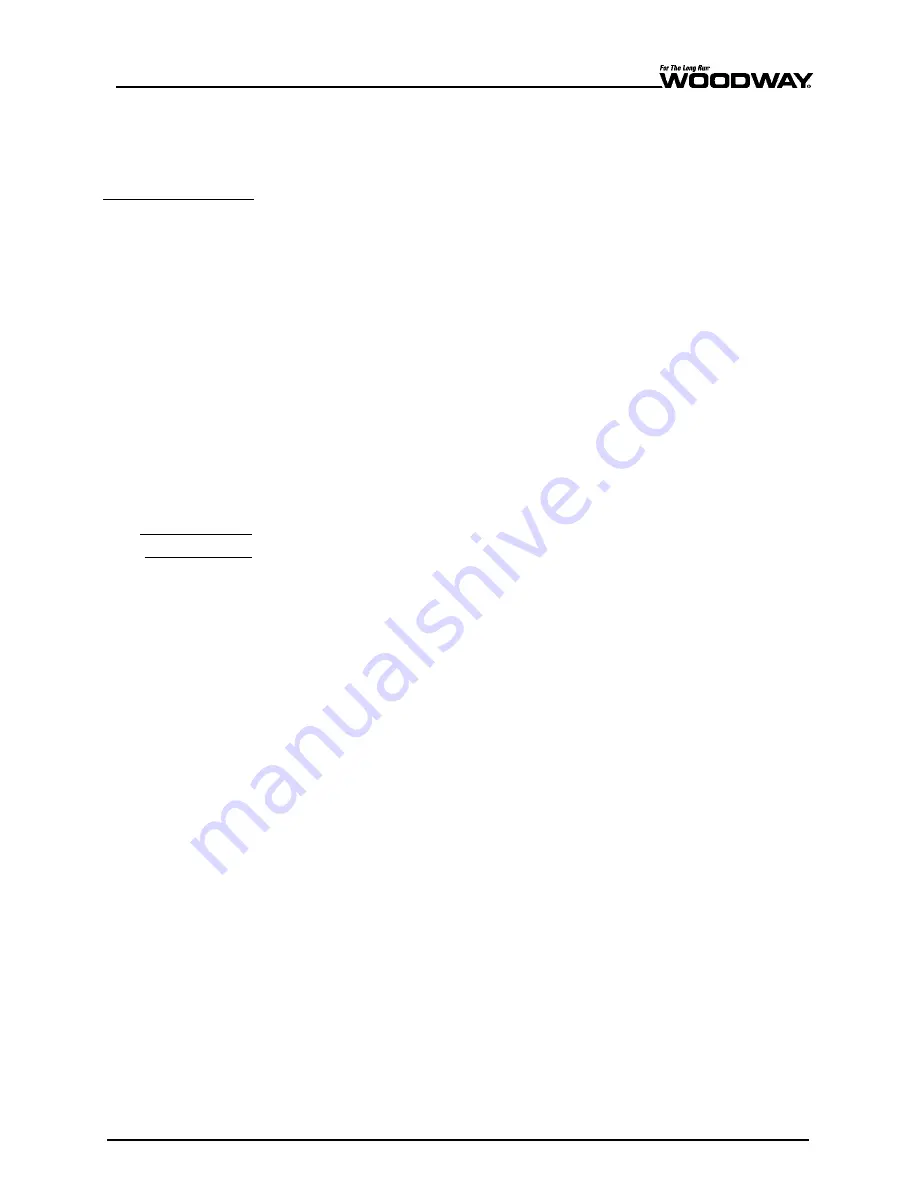
05/2016 – SM-MT-EN-02
71
7.2
Calibrating the Elevation
If it is determined that the potentiometer needs to be adjusted, you will need a 5/64”
Allen wrench to loosen the display set screw.
To adjust elevation (incline) through the treadmill’s LCD or Color LCD display board, per-
form the following:
1.
Turn the treadmill display board ON.
2.
Press ENTER-9-1-1 (in that order). The Diagnostic Mode menu will appear on the
display screen.
3.
Check to see what the actual grade reading is. If the actual grade reading is consid-
erably different from 0.0 (+/-0.3 acceptable margin of error), the potentiometer will
need to be adjusted.
4.
To adjust the potentiometer, loosen the small set screw on the side of the white
plastic gears using a 5/64” Allen wrench.
5.
Turn the potentiometer until the actual grade reading is between 0.0 and 0.3. Make
sure the actual grade reading is not negative.
6.
Once the actual grade reading is between 0.0 and 0.3, re-tighten the white gear.
Make sure that the actual grade reading does not change when the gears are tight-
ened.
7.
Once all parts are tightened properly, run the elevation up and down to make sure
the white gears stay meshed together.
8.
Press the OFF button on the display twice to save the changes and exit Diagnostic
Mode.
To adjust elevation (incline) through the treadmill’s LED display, perform the following:
1.
Turn OFF the treadmill at the main power switch (at base of treadmill by power
cord).
2.
Press and hold down the FAST key and flip the main power switch ON. The Diag-
nostic Mode menu will appear on the display screen
3.
Press the DOWN key until the treadmill cannot lower any further.
4.
Check to see what the actual grade reading is. If the actual grade reading is consid-
erably different from 0.0 (+/-0.3 acceptable margin of error), the potentiometer will
need to be adjusted.
5.
To adjust the potentiometer, loosen the small set screw on the side of the white
plastic gears using a 5/64” Allen wrench.
6.
Turn the potentiometer until the actual grade reading is between 0.0 and 0.3. Make
sure the actual grade reading is not negative.
7.
Once the actual grade reading is between 0.0 and 0.3, re-tighten the white gear.
Make sure that the actual grade reading does not change when the gears are tight-
ened.
8.
Once all parts are tightened properly, run the elevation up and down to make sure
the white gears stay meshed together.
9.
Press the OFF button on the display twice to save the changes and exit Diagnostic
Mode.
Standard LED &
Group Training
(All)
Personal Trainer LCD
(All)
Summary of Contents for 4Front
Page 16: ...16 05 2016 SM MT EN 02 2 6 EC Declaration of Conformity Fig 1 EC Declaration of Conformity...
Page 20: ...20 05 2016 SM MT EN 02 4 Parts Description 4 1 Interface Board Fig 3 Interface board C1216...
Page 61: ...05 2016 SM MT EN 02 61 6 13 Idler Shaft Replacement...
Page 82: ...82 05 2016 SM MT EN 02 11 Maintenance Report DATE MAINTENANCE MEASURES FROM REMARKS...
Page 86: ...86 05 2016 SM MT EN 02 1...
Page 87: ...05 2016 SM MT EN 02 87 2...
Page 88: ...88 05 2016 SM MT EN 02 3...
Page 89: ...05 2016 SM MT EN 02 89 4...
Page 90: ...90 05 2016 SM MT EN 02 5...
Page 91: ...05 2016 SM MT EN 02 91 6...
Page 92: ...92 05 2016 SM MT EN 02 7...
Page 93: ...05 2016 SM MT EN 02 93 8...
Page 94: ...94 05 2016 SM MT EN 02 9...
Page 95: ...05 2016 SM MT EN 02 95 10...
Page 96: ...96 05 2016 SM MT EN 02 11...
Page 97: ...05 2016 SM MT EN 02 97 12...