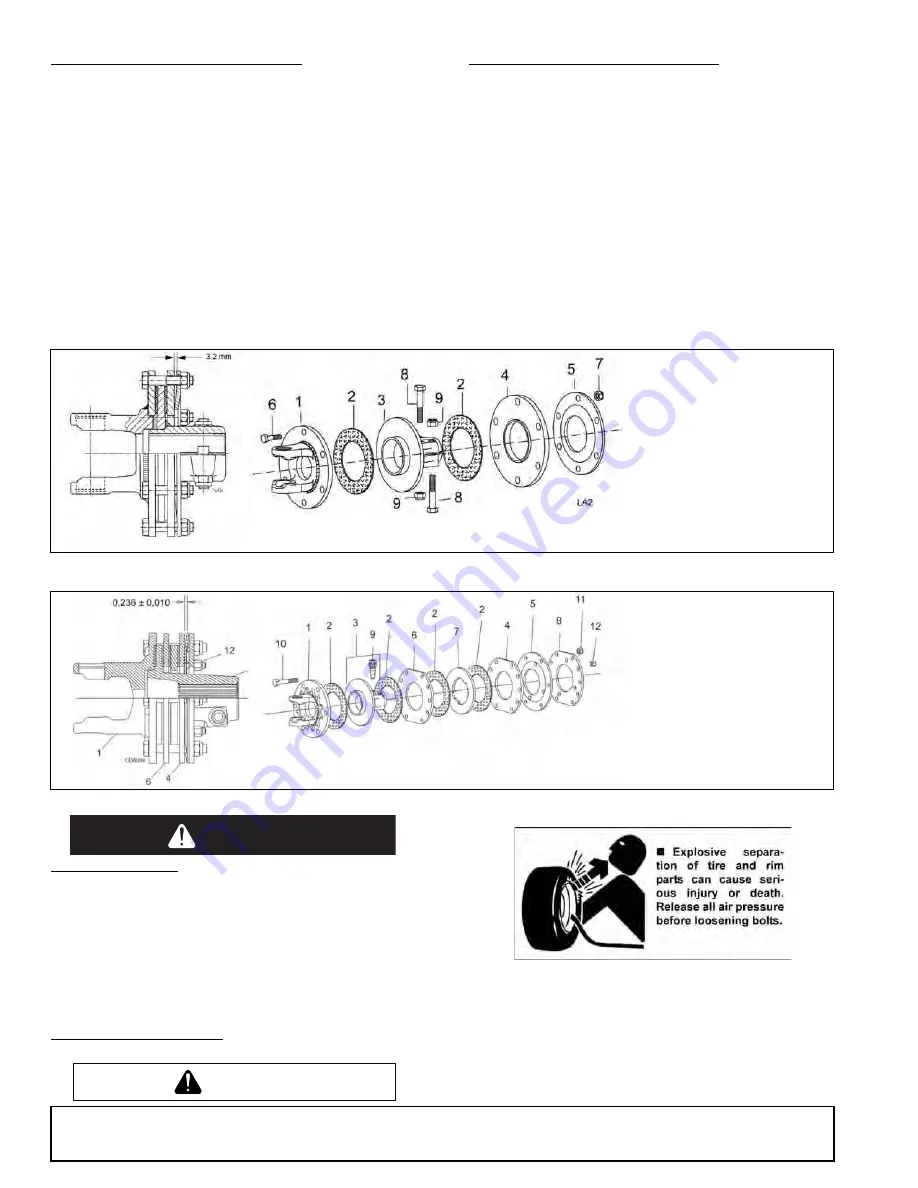
18
Owner Service
MAN1246 (04/10/2018)
2 - PLATE SLIP CLUTCH ADJUSTMENT (FIGURE 8)
The slip clutch is designed to slip so that the gearbox and driveline are pro-
tected if the cutter strikes an obstruction.
A new slip clutch or one that has been in storage over the winter may seize.
Before operating the cutter, make sure it will slip by performing the following
operation:
1.
Turn off tractor engine and remove key.
2.
Remove driveline from tractor PTO.
3.
Loosen six 10 mm cap screws (6) to remove all tension from Belleville
spring plate (5).
4.
Hold clutch hub (3) solid and turn shaft to make sure clutch slips.
5.
If clutch does not slip freely, disassemble and clean the thrust plate faces
(4), flange yoke (1), and clutch hub (3).
6.
Reassemble clutch.
7.
Tighten Belleville spring (5) until it is against the thrust plate (4) of the
clutch, and then back off each of the six nuts by 2 full revolutions. The
gap between Belleville spring and thrust plate should be 3.2 mm as
shown in Figure 8.
8.
If a clutch continues to slip when the spring is compressed to 3.2 mm
gap, check friction discs (2) for excessive wear. Discs are 3.2 mm when
new. Replace discs after 1.6 mm wear. Minimum disc thickness is 1.6
mm.
4 - PLATE SLIP CLUTCH ADJUSTMENT
(FIGURE 9)
1.
Turn off tractor engine and remove key.
2.
Tighten four nuts (12) to remove pressure from the clutch plates (2).
Repeat for all three clutches.
3.
Start tractor at low throttle and slowly engage PTO and allow clutches to
slip for 5 seconds. Disengage PTO and turn off tractor engine.
4.
If clutches slip freely, completely loosen nuts (12).
5.
If clutch does not slip freely, disassemble and clean plates (4, 6, & 7),
flange yoke (1), and clutch hub (3).
6.
Reassemble clutch.
7.
Tighten Belleville spring (5) until it is against the thrust plate (4) of the
clutch, and then back off each of the six nuts by 2 full revolutions. The
gap between Belleville spring and thrust plate should be 3.2 mm as
shown in Figure 9.
8.
If a clutch continues to slip when the spring is compressed to 3.2 mm
gap, check friction discs (2) for excessive wear. Discs are 3.2 mm when
new. Replace discs after 1.6 mm wear. Minimum disc thickness is 1.6
mm.
Figure 8
. Slip Clutch Assembly (.50E & .60E Series Models)
Figure 9
. Slip Clutch Assembly (.70E Series Models)
SHIELDING REPAIR
■
Full chain shielding must be installed at all times. Thrown objects could
injure people or damage property.
•
If the machine is not equipped with full chain shielding, operation
must be stopped.
•
This shielding is designed to reduce the risk of thrown objects. The
mower deck and protective devices cannot prevent all objects from
escaping the blade enclosure in every mowing condition. It is possible
for objects to ricochet and escape, traveling as much as 300 feet (92m).
Repairing Chain Shielding
1.
Inspect chain shielding each day of operation and replace any broken or
missing chains as required.
2.
Replace any missing hardware.
SERVICING TIRES SAFELY
Used Aircraft Tires (Figure 10)
Do not attempt to mount a tire unless you have the proper equipment and experience to
perform the job.
Always maintain the correct tire pressure. Do not inflate tires above the recommended
pressure. Never weld or heat a wheel and tire assembly. The heat can cause an
increase in air pressure and result in a tire explosion. Welding can structurally weaken
or deform the wheel.When inflating tires, use a clip-on chuck and an extension hose
long enough to allow you to stand to the side — not in front of or over the tire assembly.
Use a safety cage if available.
Check wheels for low pressure, cuts, bubbles, damaged rims, or missing lug bolts and
nuts. Never remove split rim assembly hardware (A) with the tire inflated.
1. Flange yoke
2. Friction disc
3. Hub 34.9 mm round bore
4. Thrust plate
5. Belleville spring plate
6. 10 mm x 1.5P x 50 mm Cap screw
7. 10 mm x 1.5P Hex nut
8. 12 mm x 1.5P x 65 mm Cap screw
9. 12 mm x 1.5P Hex nut
1. Flange yoke
2. Friction disc
3. Hub 34.9 mm round bore
4. Thrust plate
5. Belleville spring plate
6. Drive plate
7. Drive plate
8. Backup plate
9. Lock assembly
10. M12 x 1.75P x 85 mm HHCS
11. M12 x 1.75P Hex lock nut
12. M8 x 1.25P Hex nut
DANGER
DANGER
W
WARNING
ARNING
Summary of Contents for Batwing BW10.50E
Page 10: ...10 Declaration of Conformity MAN1246 04 10 2018 ...
Page 11: ...Declaration of Conformity 11 MAN1246 04 10 2018 ...
Page 12: ...12 Declaration of Conformity MAN1246 04 10 2018 ...
Page 28: ...28 Dealer Check Lists MAN1246 14 12 2017 NOTES ...
Page 34: ...34 50 Series Parts MAN1246 04 10 2018 WING CENTRE GEARBOX ASSEMBLY ...
Page 58: ...58 Parts All Models MAN1246 04 10 2018 TONGUE ASSEMBLY ...
Page 84: ...10 Déclaration de conformité MAN1246 14 12 2017 ...
Page 85: ...Déclaration de conformité 11 MAN1246 04 10 2018 ...
Page 86: ...12 Déclaration de conformité MAN1246 04 10 2018 ...
Page 110: ...10 Conformiteitsverklaring MAN1246 04 10 2018 ...
Page 111: ...Conformiteitsverklaring 11 MAN1246 04 10 2018 ...
Page 112: ...12 Conformiteitsverklaring MAN1246 04 10 2018 ...
Page 136: ...10 Declaración de conformidad MAN1246 04 10 2018 ...
Page 137: ...Declaración de conformidad 11 MAN1246 04 10 2018 ...
Page 138: ...12 Declaración de conformidad MAN1246 04 10 2018 ...
Page 162: ...10 Dichiarazione di conformità MAN1246 04 10 2018 ...
Page 163: ...Dichiarazione di conformità 11 MAN1246 04 10 2018 ...
Page 164: ...12 Dichiarazione di conformità MAN1246 04 10 2018 ...