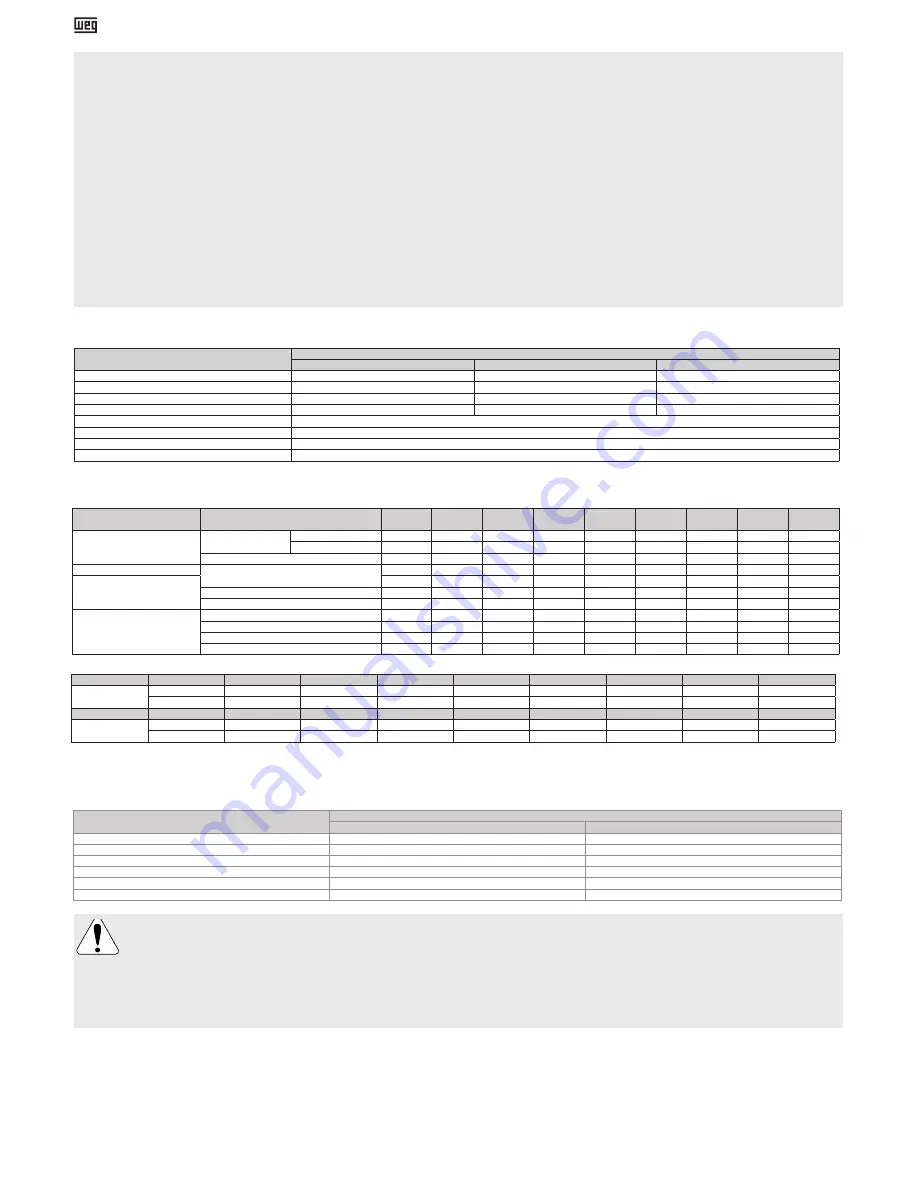
4 | Electric motors for explosive atmospheres
For motors with degree of protection IP56, IP65 or IP66, the drain plugs must remain at closed position, being opened only during the motor
maintenance procedures.
"Automatic" rubber drain plugs are designed for one use only and cannot be reused. If any drain plug is removed for any purpose, it must always
be replaced by a new one.
The drain system of motors with Oil Mist lubrication system must be connected to a specific collection system.
The drain plugs of explosion proof motors cannot be removed during installation and maintenance procedures.
When provided with a breather-drain to certificate IECEx CSA 12.0005U, the motors are limited to Groups IIB, IIC and IIIC, an ambient
temperature of -55 °C to + 40 °C, temperature classification T5 to T2, and have a degree of protection of IP6X (for group IIIC).
Do not block the motor ventilation openings. Ensure a minimum clearance of ¼ of the diameter of the air intake of the fan cover from the walls.
The air used for cooling the motor must be at ambient temperature, limited to the temperature range indicated on the motor nameplate (when not
indicated, -20 °C to +40 °C must be considered).
Motors installed outdoors or in the vertical position require the use of additional shelter to protect them from water; for instance, use of a drip cover.
To prevent accidents, ensure that the grounding connection has been performed according to the applicable standards and that the shaft key
has been well-fixed fastened before the motor is started.
Connect the motor properly to the power supply by means of safe and permanent contacts, always considering the data informed on the
nameplate, such as rated voltage, wiring diagram, etc.
When motors are supplied with flying leads, they must be suitably connected to an appropriate terminal box required for the use condition (type
of protection).
When using terminals, all wires that form the stranded cable must be fastened inside the sleeve. The insulation of the accessories cables must
be kept up to 1 mm from the connector connection point.
When provided with terminal blocks marked with “W-A12”, “W-B12 (160V)” or “W-B12 (500V)”, the following characteristics must be respected:
Table 1
- Terminal block type designation
For power cables and grounding system connections and terminal box assembly, the tightening torques indicated on Tables 2 and 3 must be respected.
Table 2
- Tightening torques for fixing elements [Nm]
Table 3
- Tightening torques for cable glands and plugs [Nm]
For power cables, switching and protection devices dimensioning, consider the rated motor current, the service factor, and the cable length, among
others. For motors without terminal block, insulate the motor terminal cables by using insulating materials that are compatible with the insulation class
informed on the nameplate. The minimum insulation distance between the non-insulated live parts themselves and between live parts and the grounding
must respect the Table 4.
Table 4 -
Minimum insulation distance (mm)
Voltage
Type of protection of the enclosure
Ex e / Ex de
Ex n/ Ex d/ Ex t
U ≤ 440 V
6
4
440 < U ≤ 690 V
10
5.5
690 < U ≤ 1000 V
14
8
1000 < U ≤ 6900 V
60
45
6900 < U ≤ 11000 V
100
70
11000 <U ≤ 16500 V
-
105
Take the required measures in order to ensure the type of protection, the EPL and the degree of protection indicated on the motor
nameplate:
- not-used cable inlet holes in the terminal boxes must be properly closed with certified plugs;
- components supplied loose (for example, terminal boxes mounted separately) must be properly closed and sealed;
The cable entries used must be fitted with components (such as, cable glands and conduits) that meet the applicable standards and
regulations for each country. For “Ex d” motors, the conduit entries are permitted only for electrical equipment of group II.
The fixing elements mounted in the threaded through holes in the motor enclosure (for example, the flange) must be properly sealed, with
the products listed in item 5, to ensure the degree of protection indicated on the motor nameplate.
The motor must be installed with overload protection devices. These protection devices can be integrated to the motor (such as thermistors in the windings)
or external protection devices, where the motor load is monitored by the nominal current. For three-phase motors, it is recommended to install a phase failure
protection device. Motors driven by variable frequency drives must have their winding thermal protections connected. For other starting methods, the use of the
thermal protections is optional. For “Ex n”, “Ex ec”, “Ex d/Ex db”, “Ex de/Ex db eb”, “Ex tb” and “Ex tc” motors: all thermal protections (RTDs, bimetal thermal
protectors and thermistors for stator protection) used in the motor protection circuit can be connected via a standard industrial controller located in a safe area.
For “Ex eb” motors: all thermal protections (RTDs, bimetal thermal protectors and thermistors for stator protection) used in the motor protection circuit must be
separately protected by the use of an intrinsic safety supply that ensures the minimum EPL Gb level of protection.
Ensure the correct operation of the accessories (brake, encoder, thermal protection, forced ventilation, etc.) installed on the motor before it is started.The temperature
limits for alarm and tripping of the thermal protection can be defined according to the application, however they may not exceed the values shown in Table 5.
Thread
Material
M16
M20
M25
M32
M40
M50
M63
M80
Metric
Plastic
3 to 5
3 to 5
6 to 8
6 to 8
6 to 8
6 to 8
6 to 8
6 to 8
Metallic
40 to 50
40 to 50
55 to 70
65 to 80
80 to 100
100 to 120
115 to 140
160 to 190
Thread
Material
NPT 1/2"
NPT 3/4"
NPT 1"
NPT 1 1/2"
NPT 2"
NPT 2 1/2"
NPT 3"
NPT 4"
NPT
Plastic
-
5 to 6
6 to 8
6 to 8
6 to 8
6 to 8
6 to 8
6 to 8
Metallic
40 to 50
40 to 50
55 to 70
65 to 80
100 to 120
115 to 140
150 to 175
200 to 240
Type of protection
of enclosure
Component
M4
M5
M6
M8
M10
M12
M14
M16
M20
Ex d
Ex de
Terminal Box Cover
Class 8.8/12.9
-
3.5 to 5
6 to 12
14 to 30
28 to 60
45 to 105
75 to 110
115 to 170 230 to 330
Class A2-70 / A4-70
-
3.5 to 5
6 to 8.5
14 to 19
28 to 40
45 to 60
75 to 100 115 to 170 225 to 290
Grounding
1.5 to 3
3 to 5
5 to 10
10 to 18
28 to 40
45 to 70
-
115 to 170
-
Ex d
Terminal block
1 to 1.5
2 to 4
4 to 6.5
6.5 to 9
10 to 18
15.5 to 30
-
30 to 50
50 to 75
Ex de
1 to 1.5
2 to 4
4 to 6.5
6.5 to 9
5 to 9
10 to 15
-
20 to 30
-
Locking bolt for connection clamp
-
3 to 7
4 to 8
7 to 11
-
-
-
-
-
Locking bolt for power cables
-
-
-
2 to 6
6 to 10
-
-
-
-
Ex n
Ex t
Ex e
Terminal box cover
-
3 to 5
4 to 8
8 to 15
18 to 30
25 to 40
30 to 45
35 to 50
-
Grounding
1.5 to 3
3 to 5
5 to 10
10 to 18
28 to 40
45 to 70
-
115 to 170
-
Terminal block
1 to 1.5
2 to 4
4 to 6.5
6.5 to 9
10 to 18
15.5 to 30
-
30 to 50
50 to 75
Terminal block fixing bolts
-
3 to 5
5 to 10
10 to 18
28 to 40
45 to 70
75 to 110
115 to 170
-
Characteristic
Terminal block type designation
W-A12
W-B12 (160 V)
W-B12 (500 V)
Voltage
Up to 160 V
Up to 160 V
Up to 500 V
Current
Max. 15 A
Max. 15 A
Max. 20 A
Conductor cross-section
0,3 to 2,5 mm²
0,3 to 4 mm²
0,3 to 4 mm²
Number of cables per terminal connection
2x1 mm²
2x1,5 mm²
2x1,5 mm²
Connection torque
0,5 to 0,7 Nm
Service temperature
-20 °C to + 80 °C
ATEX marking/certificate
II 2G Ex eb IIC Gb / I M2 Ex eb I Mb / PTB 06 ATEX 1078 U
IECEx marking/certificate
Ex eb IIC Gb / Ex eb I Mb / IECEx PTB 17.0014U