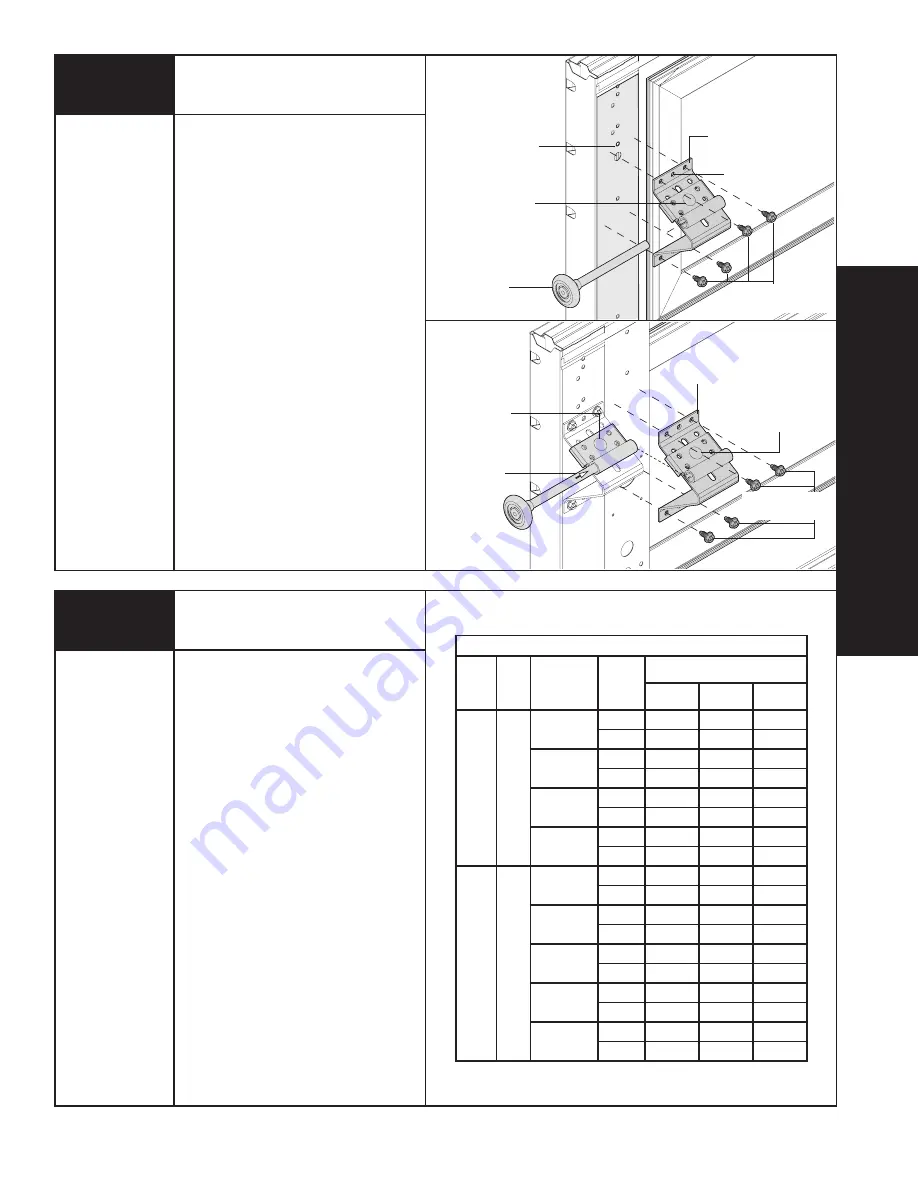
11
Please Do Not Return This Product To The Store.
Contact your local Wayne-Dalton dealer. To find your local Wayne-Dalton dealer, refer to your
local yellow pages/business listings or go to the
Find a Dealer
section online at
www.wayne-dalton.com
Tools Needed:
Tools Needed:
iNST
alla
Tio
N
7
Top bracket
Power Drill
7/16” Socket Driver
NoTe:
for windload specification option codes 1320
and 1340, two top bracket assemblies and a long
stem roller are required for each side.
Align center hole of the top bracket assembly(s) with
#6 hole in the end stile (See End Stile hole Pattern
on Pg 8). Ensure the top bracket assembly(s) is level
and aligned with the edge of the section. Secure
the top bracket assembly(s) to the endstile using
(4) 1/4” - 14 x 7/8” self drilling screws. Loosen the
5/16” - 18 nut on the top bracket assembly(s). Insert
a roller into the slide(s) of the top bracket. Repeat for
the opposite side.
The top bracket slide(s) will be adjusted and
tightened in Step 17.
Top bracket
assembly
End
stile
Top
section
#6 hole
Center hole
(4) 1/4”- 14 x 7/8”
Self drilling screws
(1) 5/16”- 18 x 5/8”
Carriage bolt and (1)
5/16”- 18 hex nut
Stile
Top bracket assembly
(1320/1340 only)
Long stem roller
(1320/1340 only)
(1) 5/16”- 18 x
5/8” Carriage bolt
and (1) 5/16”- 18
hex nut
(4) 1/4”- 14 x 7/8”
Self drilling screws
(1) 5/16”- 18 x 5/8”
Carriage bolt and (1)
5/16”- 18 hex nut
Power Drill
7/16” Socket Driver
u-bar
NoTe:
for door section identification see page 4.
Refer to the u-bar schedule to determine the required
number of u-bar(s), and placement on each section.
NoTe:
U-Bars are typically placed flush against the
upper or lower hinge leafs, except on top of the top
section.
Place the sections face down on a couple of
sawhorses or flat clean/ smooth surface. Butt the
sections together in the proper stack sequence and
flip up the hinges. Position the u-bars according to
the u-bar schedule, and flush against the hinge leafs.
Center the u-bars side to side on the section, and
secure using (2) 1/4” -14 x 7/8” self drilling screws
at each end stile and center stile location. Repeat for
all other sections except the top of the top section.
iNSTallaTioN oN The ToP SecTioN:
Position the
u-bar above the top bracket assembly. Center the u-
bar side to side on the section, and secure using (2)
1/4” - 14 x 7/8” self drilling screws at each end stile
and center stile location.
8
u-bar Schedule
Door
height
# of
sections
Section
Position
on
section
Specification options code
1300
1320
1340
6’- 0”
to
7’- 0”
4
Bottom
Bottom
Top
X
X
X
Lock
Bottom
X
Top
X
X
X
Intermediate I
Bottom
X
Top
X
X
X
Top
Bottom
X
Top
X
X
X
7’- 6”
to
8’- 0”
5
Bottom
Bottom
Top
X
X
X
Lock
Bottom
X
Top
X
X
X
Intermediate I
Bottom
X
Top
X
X
X
Intermediate II
Bottom
X
X
X
Top
X
X
X
Top
Bottom
X
Top
X
X
X
Short stem roller
(1300 only)