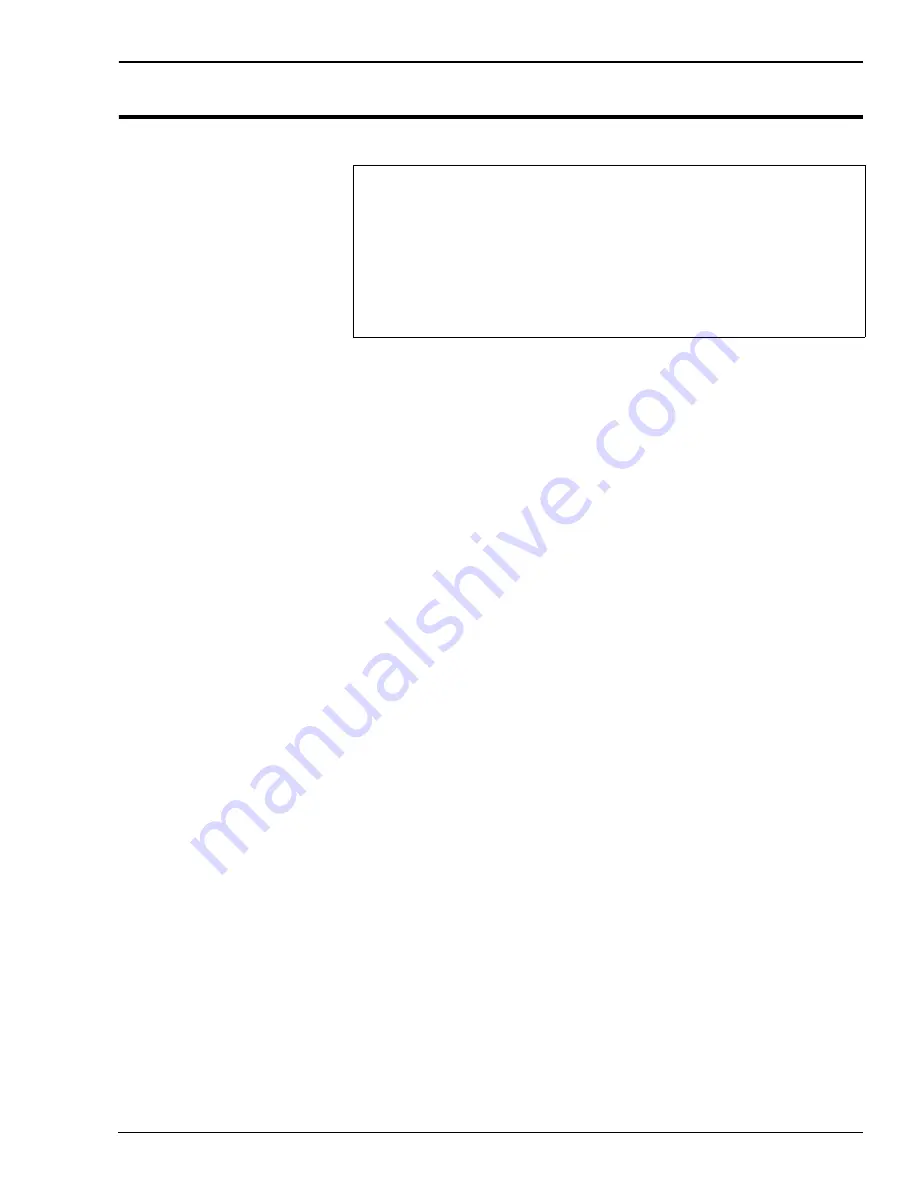
General Procedures
•
Watkiss Automatic SpineMaster Service Manual - Edited 17/06/04
6 - 1
Chapter 6 General Procedures
SECTION
PAGE
Product Specifications . . . . . . . . . . . . . . . . . . . . . . . . . . . . . . . . . . . . . . 2
Space Requirements . . . . . . . . . . . . . . . . . . . . . . . . . . . . . . . . . . . . . . . . 4
Recommended Tools & Consumables . . . . . . . . . . . . . . . . . . . . . . . . . . 5
Recommended Spare Parts . . . . . . . . . . . . . . . . . . . . . . . . . . . . . . . . . . 6