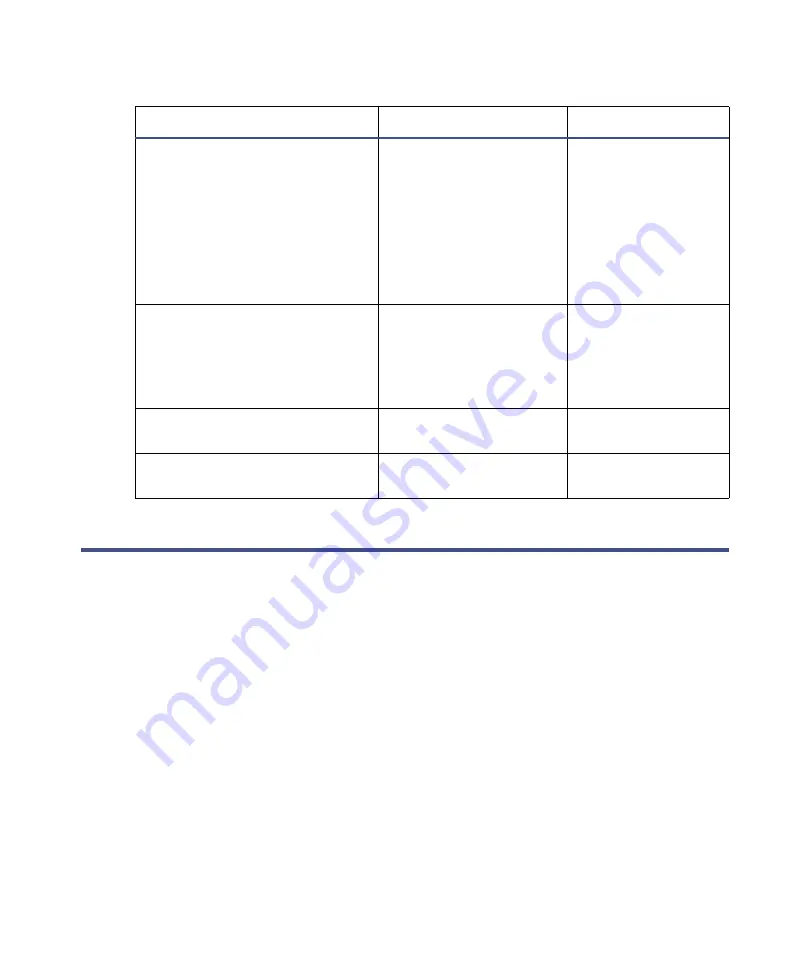
Spare parts
4-5
Spare parts
Replace only the parts mentioned in this document. For spare parts details,
see the Waters Quality Parts Locator on the Waters Web site’s
Services/Support page.
Replace the roughing pump’s
demister element.
Annually.
Tip:
Applications that
contaminate the
roughing pump oil
reduce this period,
which must be
determined from
experience.
Clean the APPI/APCI source
UV lamp window.
When the window
becomes visibly dirty
or when the sensitivity
decreases to
unacceptable levels.
Change the APPI/APCI source
UV lamp bulb.
When the bulb fails.
Replace the APPI lamp drive
assembly O-rings.
Annually.
See
Maintenance schedule:
Procedure
Frequency
For information...
Summary of Contents for Xevo TQD
Page 12: ...xii...
Page 20: ...xx Table of Contents...
Page 23: ...Uses and compatibility 1 3 Xevo TQD TP03406...
Page 24: ...1 4 Specifications and Operating Modes Xevo TQD with visor up TP03407...
Page 42: ...1 22 Specifications and Operating Modes...
Page 52: ...2 10 Preparing for Operation...
Page 76: ...3 24 Changing the Mode of Operation...
Page 194: ...4 118 Maintenance Procedures...
Page 208: ...A 14 Safety Advisories...
Page 234: ...B 26 External Connections...
Page 238: ...C 4 Materials of Construction and Compliant Solvents...
Page 250: ...Index 8...