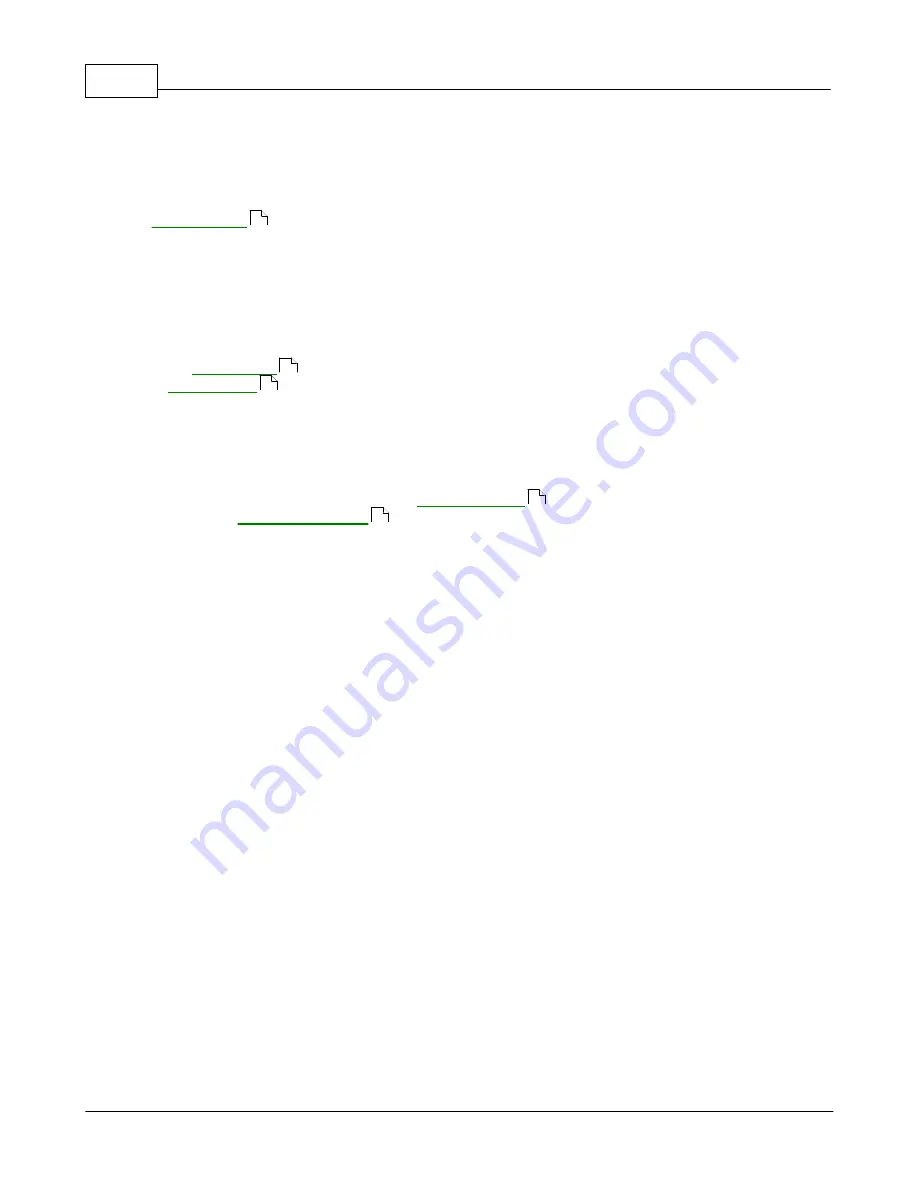
VibrationVIEW Help
225
© 1995-2005 Vibration Research Corporation. All rights reserved.
7.3.5
End of Timed Test
End of Timed Test (
Sine Stop Code
)
This code indicates that the test was run for the scheduled time duration (as defined in the
dialog box). When this code is displayed, the test is complete and the output is
turned off.
7.3.6
Front Panel Start
Front Panel Start (
Sine Stop Code
)
This code indicates that the test was started using the "Start" switch on the front panel of the
VibrationVIEW
I/O unit. While this code is displayed, the system is in the starting mode, as described
in the
stop code. Once the desired level has been reached, the test mode will change
.
7.3.7
Holding Frequency
Holding Frequency (
Sine Stop Code
)
This code indicates that the output frequency is held at a fixed value. The frequency sweep can be
frozen using either mouse control in the
dialog box or by clicking the "Hold Sweep"
button in the
.
7.3.8
Input channel N is clipping
Input channel n is clipping (
Sine Stop Code
)
This code indicates that the input signal to channel n is exceeding the allowable input voltage range of
+/- 10 volts and is being distorted by clipping. To solve this problem, use an accelerometer with a
lower mV/G sensitivity rating.
The maximum allowable acceleration readings for various accelerometer sensitivities are shown in the
table below.
Sensitivity
Maximum Acceleration
10 mV/G
1000 G peak
20 mV/G
500 G peak
50 mV/G
200 G peak
100 mV/G
100 G peak
1000 mV/G
10 G peak
7.3.9
NI-DAQ error code
NI-DAQ error code (
Sine Stop Code
)
This code indicates that an error occurred while reading input channels from the National Instruments
data acquisition card. This error typically happens when another program (e.g. VibrationAnalyzer) is
attempting to read data from the data acquisition card at the same time as the
VibrationVIEW
program.
Do not run the VibrationAnalyzer program while a sine test is running.
To clear this error condition, stop and resume the test. That is, click the "Stop" button, click the "Run"
button and select "Yes" to continue the current test.
286
228
227
263
206
Summary of Contents for VibrationVIEW
Page 15: ...Document Revision Part I ...
Page 17: ...How To Part II ...
Page 96: ...Menu commands Part III ...
Page 142: ...Test Definition Part IV ...
Page 217: ...Control Centers Part V ...
Page 227: ...Accelerometer Toolbars Part VI ...
Page 231: ...Stop Codes Part VII ...
Page 263: ...Typical Views Part VIII ...
Page 268: ...VibrationVIEW Help 255 1995 2005 Vibration Research Corporation All rights reserved ...
Page 269: ...Dialog Boxes Part IX ...
Page 303: ...Windows Elements Part X ...
Page 309: ...APPENDIX Part XI ...
Page 311: ...APPENDIX 298 1995 2005 Vibration Research Corporation All rights reserved ...