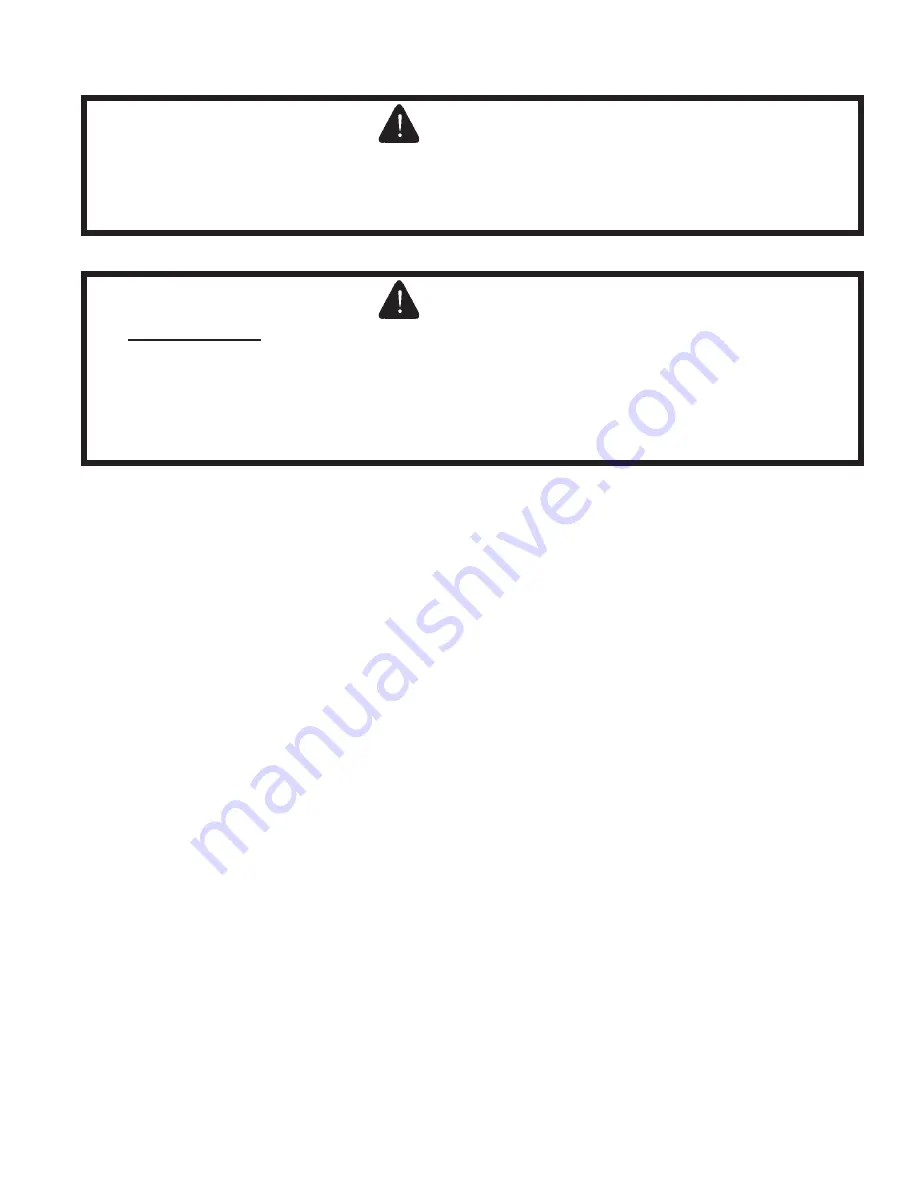
93
Appendix A: Instructions for Conversion of This Boiler for Use with LP Gas
All boilers listed in this manual are factory configured for use on Natural gas at altitudes at or below 2000 feet. Perform the steps
listed in these instructions to convert it for use with LP gas.
1) If not already done, install the boiler in accordance with this manual, following all instructions in Part XI (Start-up and
Check-out) up to Step 10.
2) Set the throttle to its preliminary setting for LP. To do this:
a. Turn the throttle (Figure A.1) clockwise until it stops (several full turns).
b. Turn throttle counter-clockwise the exact number of turns shown in Table A.2.
3) Attempt to start the boiler using the lighting instructions located on Page 60. If the boiler does not light on the first try
for ignition, allow to boiler to make at least four more attempts to light. If boiler still does not light, turn the throttle
counterclockwise in 1/8 turn increments, allowing the boiler to make at least four tries for ignition at each setting, until the
boiler lights.
4) After the burner lights, force the burner to high fire by entering the Diagnostics Menu, and selecting Manual Input, then “HF”
as described in Part XI (start-up and checkout). Allow the boiler to operate for approximately 5 minutes before
taking combustion readings. Note: that after 15 minutes, boiler is automatically released from high fire hold. The boiler will
also be released from manual input if the user manually navigates back to the home screen.
5) Perform a combustion test, sampling flue products from the tap in the front of the vent adaptor.
6) While the burner is at high fire adjust the throttle as needed to obtain the CO2 settings shown in the Table A.3:
• To reduce the CO2 (increase the O2) turn the throttle clockwise
• To increase the CO2 (reduce the O2) turn the throttle counter-clockwise
Make adjustments in increments of 1/8 to 1/4 turn and allow the boiler at least a minute to respond to each adjustment before
making another. In general, the CO level will be at its lowest somewhere in the CO2 range shown in this table. Consult
factory if it is not possible to reduce the CO level below 200PPM air free within the range of CO2s shown for the fuel and
altitude at which the boiler is being used.
DANGER
These instructions include a procedure for adjusting the air-fuel mixture on this boiler. This
procedure requires a combustion analyzer to measure the CO2 and Carbon Monoxide (CO) levels
in flue gas. Adjusting the air-fuel mixture without a proper combustion analyzer could result in
unreliable boiler operation, personal injury, or death due to carbon monoxide poisoning.
WARNING
•
LP CONVERSIONS
- This conversion shall be performed by a qualified service agency in
accordance with the manufacturer’s instructions and all applicable codes and requirements of the
authority having jurisdiction. If the information in these instructions is not followed exactly, a fire, an
explosion or production of carbon monoxide may result causing property damage, personal injury,
or loss of life. The qualified service agency is responsible for proper conversion of this boiler. The
installation is not proper and complete until the operation of the converted appliance is checked as
specified in the instructions below.
Summary of Contents for Shadow Series
Page 10: ...9 Figure 5 1 Wall Layout Mounting Hole Location...
Page 11: ...10 Figure 5 2 Boiler Mounting Bracket Installation Boiler Wall Mounting...
Page 17: ...16 FIGURE 7 4 WALL PENETRATION CLEARANCES FOR PVC VENT PIPE...
Page 34: ...33 FIGURE 7 24 INSTALLATION OF IPEX AND DIVERSITECH CONCENTRIC TERMINAL THROUGH ROOF...
Page 41: ...40 FIGURE 9 2 NEAR BOILER PIPING HEATING ONLY BOILER LOOP PIPING SHOWN SHADED...
Page 42: ...41 FIGURE 9 3a NEAR BOILER PIPING HEATING PLUS INDIRECT WATER HEATER...
Page 43: ...42 FIGURE 9 3b NEAR BOILER PIPING HEATING PLUS INDIRECT WATER HEATER...
Page 47: ...46 This page is intentionally left blank...
Page 50: ...49 FIGURE 10 2 LINE VOLTAGE FIELD CONNECTIONS FIGURE 10 3 LOW VOLTAGE PCB TERMINAL CONNECTIONS...
Page 52: ...51 FIGURE 10 4a 120V LWCO FIELD WIRING FIGURE 10 4b 24V LWCO FIELD WIRING...
Page 54: ...53 FIGURE 10 6 INTERNAL WIRING CONNECTIONS DIAGRAM...
Page 55: ...54...
Page 62: ...61 Lighting and Operating Instructions...
Page 82: ...81 FIGURE 14 6 CONTROLS LOCATION FIGURE 14 7 PRESSURE SWITCH TUBING CONNECTIONS...
Page 87: ...86 Blower Gas Valve Assembly for 150 180...
Page 90: ...89...
Page 103: ...102...