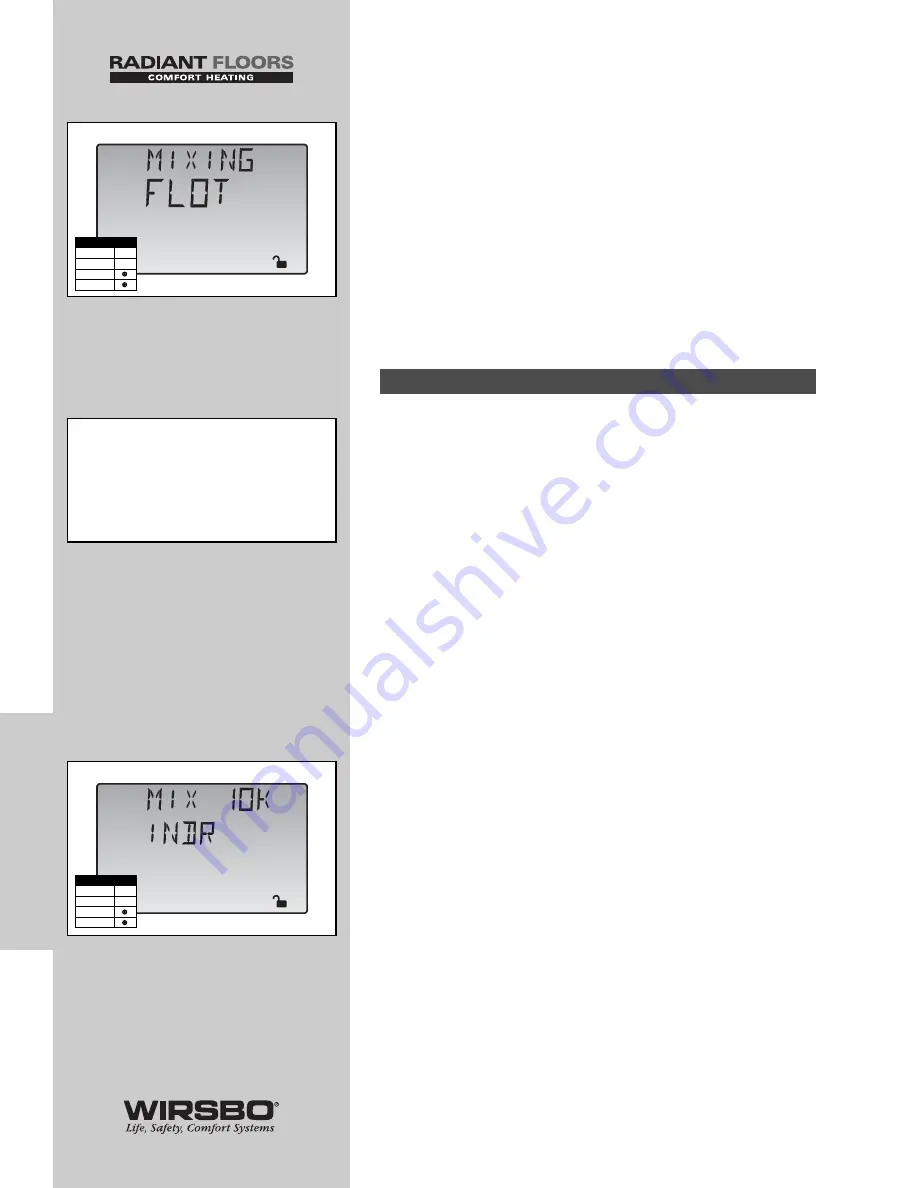
FLOATING ACTION (FLOT)
(See fig. k)
• A floating action actuator motor is connected to control on
Opn and Cls/P4 terminals (18 and 19)
• The control pulses actuator motor open or closed to
maintain correct supply water temperature at mix supply
sensor during mix demand
• The mixing valve actuator can be connected to a 2-way,
3-way or 4-way valve
• A visual indication as to whether control is currently opening
or closing the mixing valve is displayed in the LCD with the
words Open and Close (also, a visual indication of the valve's
current position is displayed in the form of a segmented bar
graph)
EXTERNAL MIXING DEMAND
(See fig. l)
An external mixing demand allows use of a conventional
thermostat system for zoning. Demand is generated by
applying a voltage between 24 and 240 VAC across the Mix
Demand terminals (1 and 2).
• Once voltage is applied, the Mix Demand pointer is
displayed in the LCD
• If the SYSTEMpro 311 is not in WWSD, it closes the Mixing
Pmp P1 contact
• The Mixing system pump segment is displayed in the LCD
• Control calculates a MIX TRG temperature based on outdoor
air temperature and settings
• If required, control operates Boiler contact (as described in
Section B2, page. 62) to provide heat to mixing device
10K INDOOR SENSOR (MIX 10K = INDR)
(See fig. l)
Set MIX 10K item to INDR to add an indoor sensor that offers
temperature control of a single zone mixing system. The
indoor sensor is connected to Com and Mix 10K terminals
(20 and 21). Power must also be applied to Mix Demand
terminals (1 and 2).
• With indoor sensor connected, control can sense the actual
room temperature
• Using this information, the control offers more constant
water flow through mixing system
• Indoor feedback fine-tunes supply water temperature in
mixing system to prevent overheating or underheating
NOTE:
To adjust room temperature for the mixing
zone, use MIX ROOM setting in the Adjust Menu.
Section D3: Mixing Demands
70
CONTROL FUNCTION
OVER
VIEW
CONTROL FUNCTION OVERVIEW -
CONTROL FUNCTION OVERVIEW - Section D - Mixing Zones
Adjust
k
Adjust
l
Access Level
LTD
USER
INST
ADV
Access Level
LTD
USER
INST
ADV
NOTE:
If connecting a Wirsbo
thermostat (WT1 or WT2) directly
to the Mix Demand terminals,
refer to Mixing Demand with
Wirsbo Thermostat on page 23.
Summary of Contents for SYSTEMpro 311
Page 1: ...SYSTEMpro 311 Installation Manual...
Page 90: ...88 APPENDIX II APPENDIX II SYSTEMpro 311 Menu Tree...
Page 91: ...89 APPENDIX II APPENDIX II SYSTEMpro 311 Menu Tree...
Page 92: ...90 APPENDIX III APPENDIX III Application Drawings...
Page 93: ...91 APPENDIX III APPENDIX III Application Drawings...
Page 94: ...92 APPENDIX III APPENDIX III Application Drawings...
Page 95: ...93 APPENDIX III APPENDIX III Application Drawings...
Page 96: ...94 APPENDIX III APPENDIX III Application Drawings...
Page 97: ...95 APPENDIX III APPENDIX III Application Drawings...
Page 98: ...96 APPENDIX III APPENDIX III Application Drawings...
Page 99: ...97 APPENDIX III APPENDIX III Application Drawings...
Page 106: ......