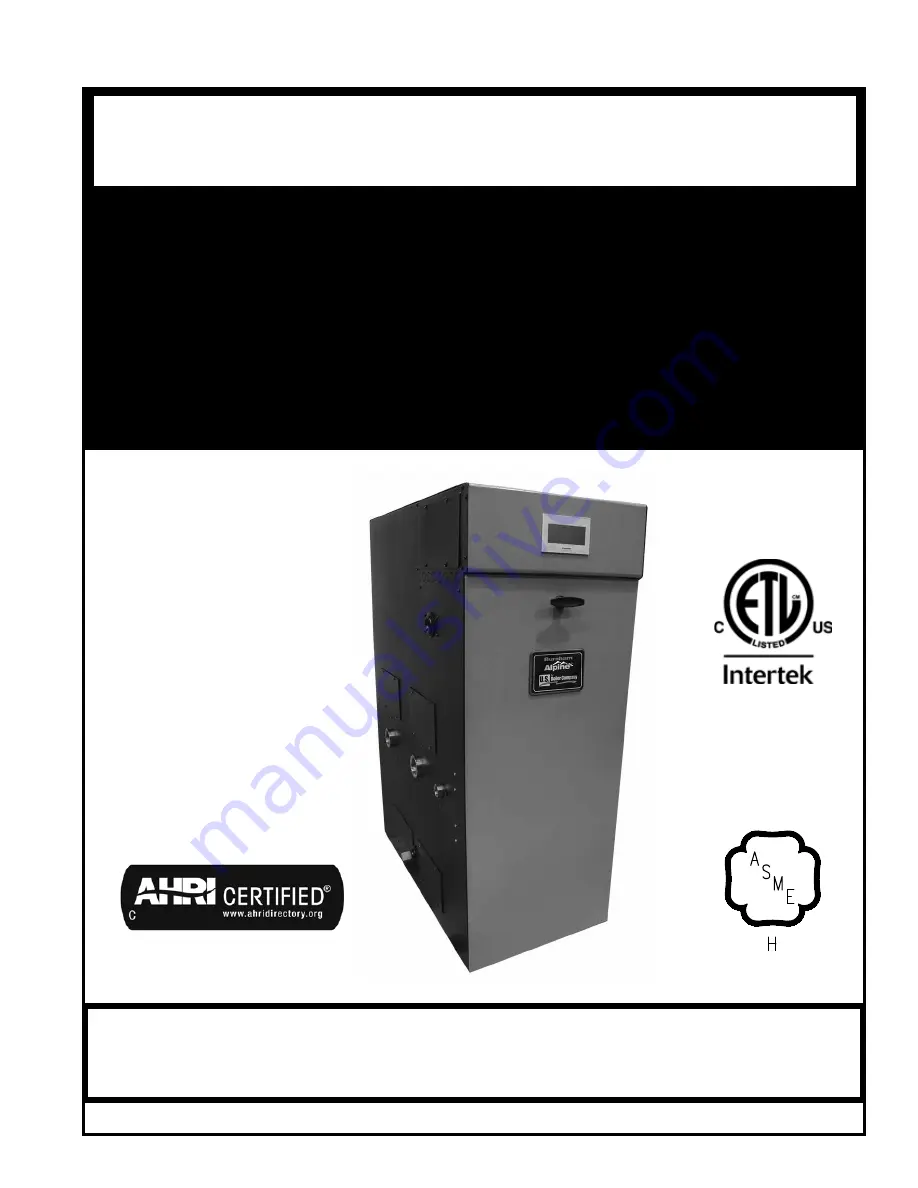
1
106307-02 - 2/17
Price - $5.00
Warning:
Improper installation, adjustment, alteration, service or maintenance can cause property damage,
injury, or loss of life. For assistance or additional information, consult a qualified installer, service agency or the
gas supplier. This boiler requires a special venting system. Read these instructions carefully before installing.
inSTaLLaTiOn, OPEraTing anD
SErViCE inSTrUCTiOnS FOr
aLPinE
™
COnDEnSing HigH EFFiCiEnCY
DirECT VEnT
GAS - FIRED HOT WATER BOILER
Size range - 399 MBH through 800 MBH
9700609
alpine “C” Models:
• ALP399C
• ALP500C
• ALP600C
• ALP700C
• ALP800C
http://waterheatertimer.org/Two-water-heaters.html#boiler
http://waterheatertimer.org/What-size-indirect-heater.html
Summary of Contents for Alpine ALP500C
Page 48: ...48 VI Water Piping and Trim continued Figure 28 Near Boiler Piping Heating Only ...
Page 62: ...62 Figure 40 Ladder Diagram VIII Electrical continued ...
Page 63: ...63 VIII Electrical continued 2 Figure 41 Wiring Connections Diagram ...
Page 72: ...72 IX System Start up continued Figure 48 Operating Instructions ...
Page 124: ...124 XIII Repair Parts continued ...
Page 126: ...126 XIII Repair Parts continued ALP600C ALP700C and ALP800C ALP800C shown ...
Page 130: ...130 XIII Repair Parts continued ...
Page 133: ...133 XIII Repair Parts continued 10A 10B 10C 10D 10G ...
Page 143: ...143 ...
Page 144: ...144 U S Boiler Company Inc P O Box 3020 Lancaster PA 17604 1 888 432 8887 www usboiler net ...