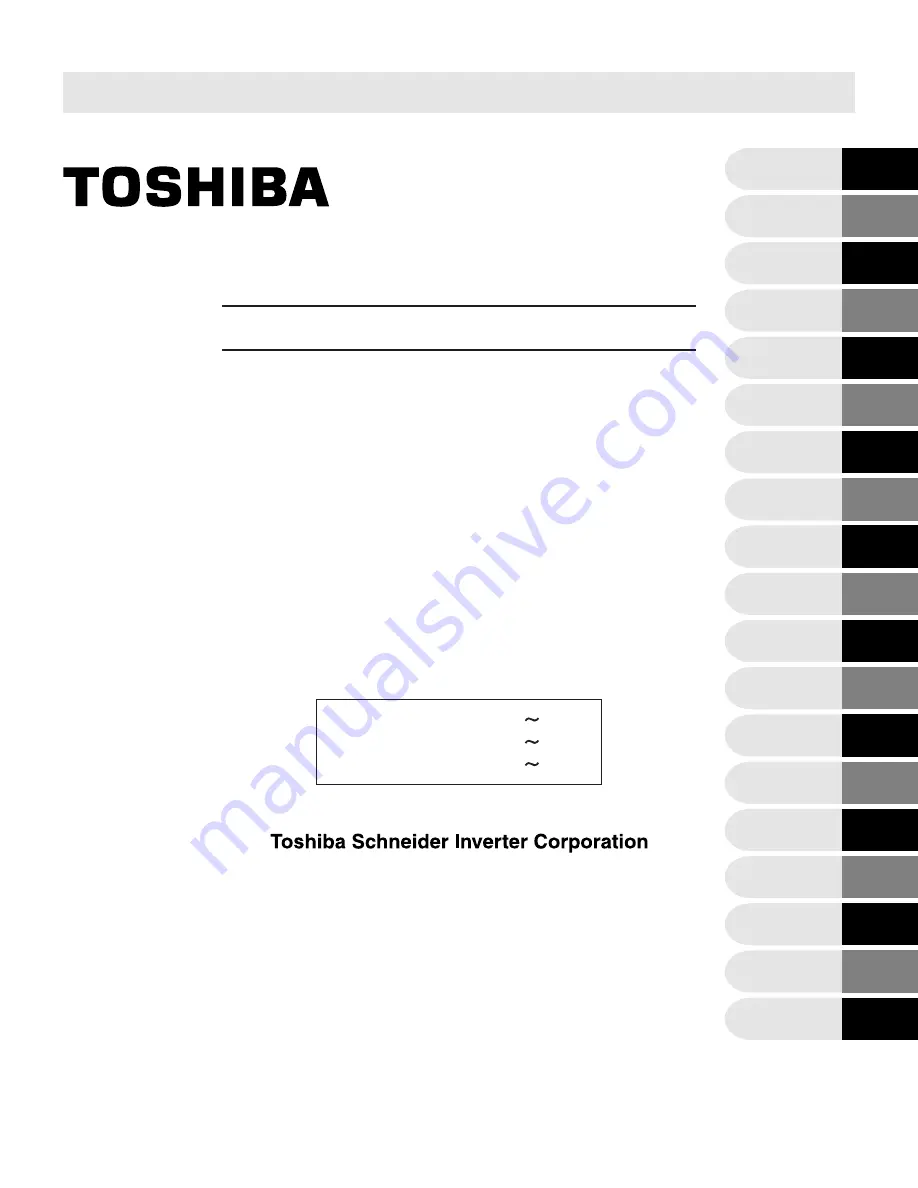
II
1
2
3
4
5
6
7
8
9
10
11
12
13
14
15
16
E6581158
Read first
I
Safety
precautions
Introduction
Contents
Connection
equipment
Operations
Basic VF-S11
operations
Basic
parameters
Extended
parameters
Applied
operation
Monitoring the
operation status
Taking measures
to satisfy the
CE directive
Peripheral
devices
Table of
parameters
and data
Specifications
Before making a service
call - Trip information and
remedies
Inspection and
maintenance
Warranty
Disposal of the
inverter
NOTICE
1.Make sure that this instruction manual is delivered to the
end user of the inverter unit.
2.Read this manual before installing or operating the inverter
unit, and store it in a safe place for reference.
Instruction Manual
New Global Standard Inverter
TOSVERT
TM
VF-
S11
1-phase 200V class 0.2
2.2kW
3-phase 200V class 0.2
15kW
3-phase 400V class 0.4
15kW
2003