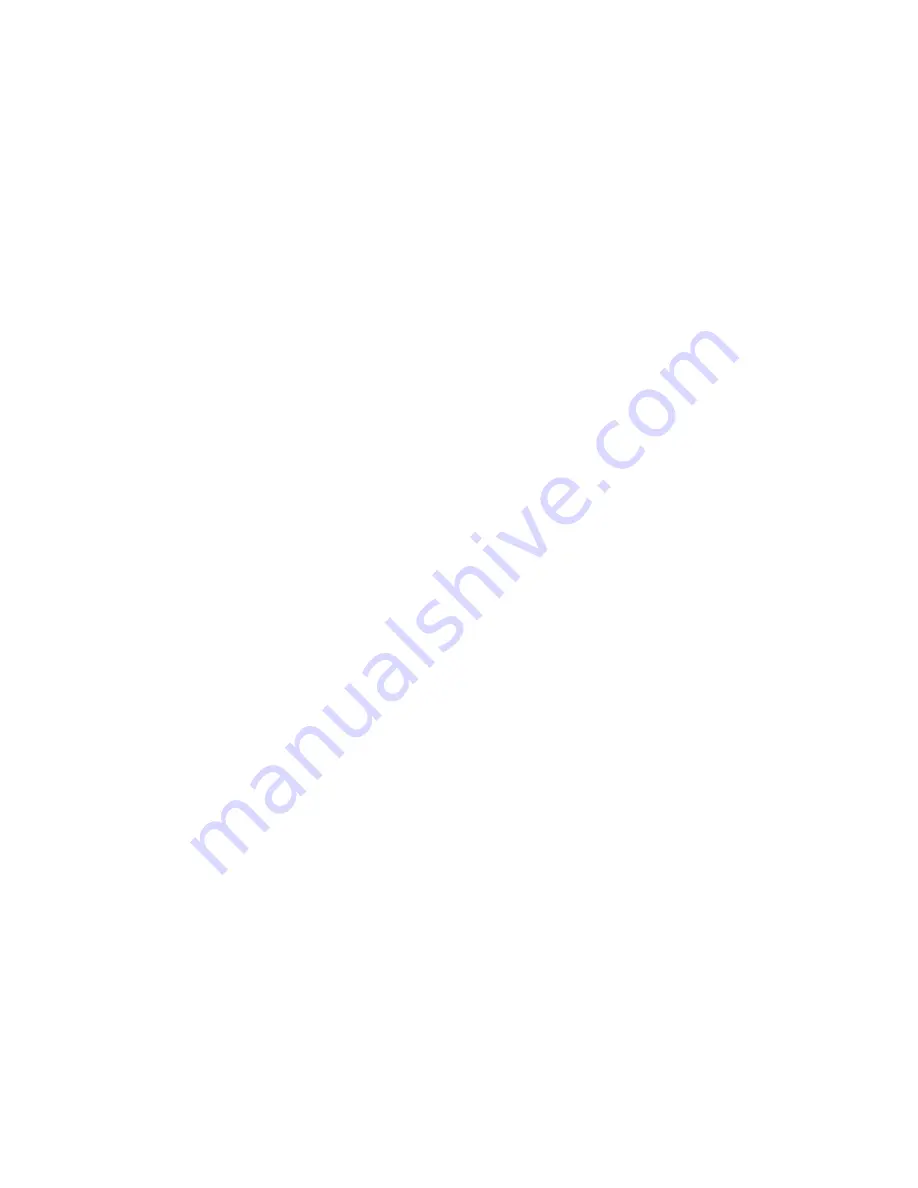
Installing the Auxiliary Load Valve (continued)
5. Operate the auxiliary load valve. Check for hydraulic leaks and correct
if necessary.
6. Install the operator’s console; refer to
Removing and Installing the Operator’s
.
7. Test the attachment/loader circuit relief valve pressure before returning the
machine to service; refer to
Attachment/Loader Circuit Testing – Relief Valve
Pressure Test (page 5–43)
.
8. Check the hydraulic fluid level and adjust if necessary before returning the
machine to service.
Hydraulic System: Service and Repairs
Page 5–104
Outcross 9060
18234SL Rev B
Summary of Contents for 07511AA
Page 4: ...Reader Comments Page 4 Outcross 9060 18234SL Rev B ...
Page 18: ...Safety Safety and Instructional Decals Page 1 10 Outcross 9060 18234SL Rev B ...
Page 38: ...Specifications and Maintenance Special Tools Page 2 20 Outcross 9060 18234SL Rev B ...
Page 96: ...Engine Service and Repairs Page 4 24 Outcross 9060 18234SL Rev B ...
Page 208: ...Hydraulic System Service and Repairs Page 5 112 Outcross 9060 18234SL Rev B ...
Page 294: ...Electrical System Service and Repairs Page 6 86 Outcross 9060 18234SL Rev B ...
Page 384: ......