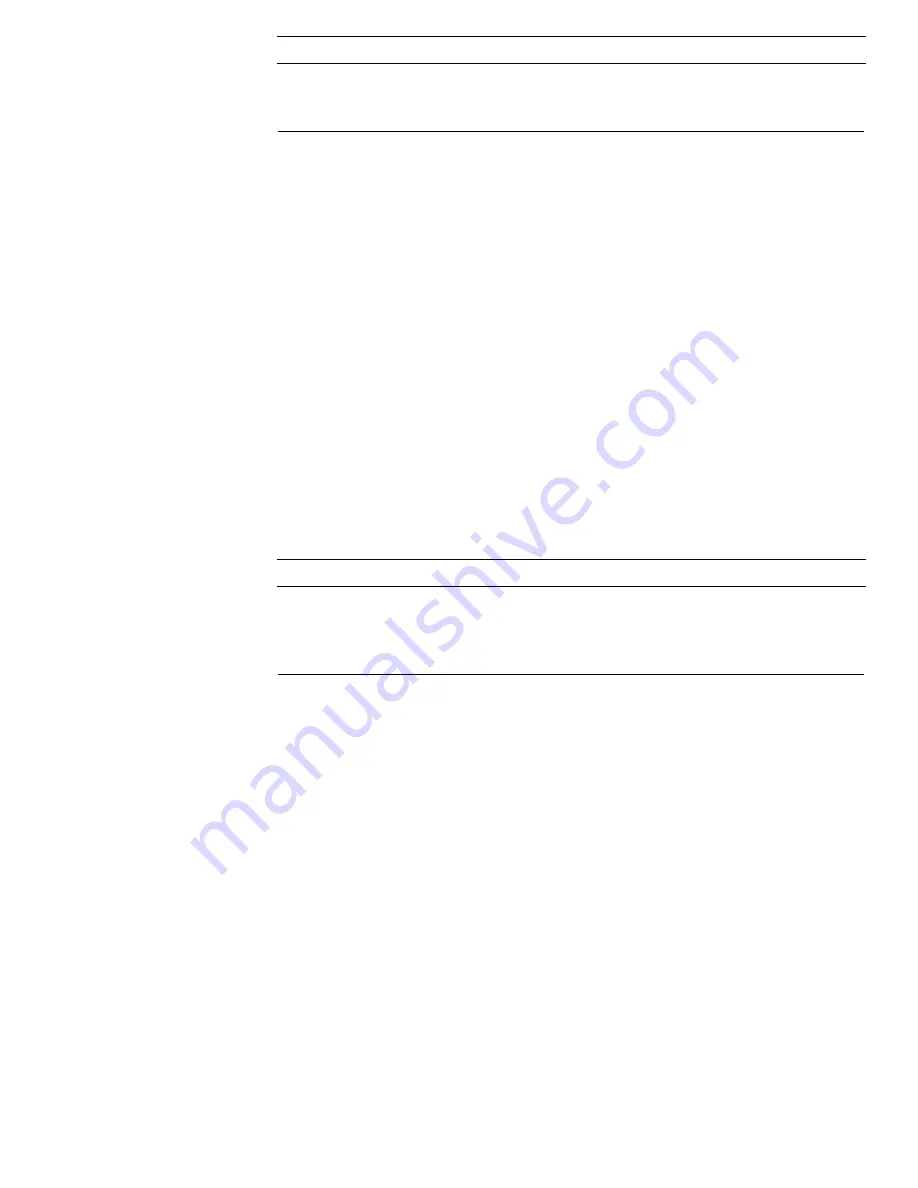
IMPORTANT
Use 2 people to perform all the tests, with 1 person in the operators
seat and the other available to read and record the test results.
1. Use the following resources to assist with hydraulic system troubleshooting.
• The Hydraulic Schematic in
Appendix A (page A–1)
•
Hydraulic Flow Diagrams (page 5–14)
• General and system specific troubleshooting tables in Chapter 3 –
Troubleshooting
2. Always wear the eye protection when you performing hydraulic system tests.
3. Clean the machine fully before you disconnect or disassemble the hydraulic
components.
Note:
Cleanliness is required whenever you work on the hydraulic
equipment. Contamination causes wear on hydraulic components.
4. To prevent hydraulic system contamination, put metal caps or plugs on any
hydraulic lines left open or exposed during testing or removal of components.
5. The engine must be in good operating condition. Use the tachometer on
the T2: TDM display to verify and monitor engine RPM when performing a
hydraulic test. Engine speed can affect the accuracy of the test readings.
Use the information below when performing hydraulic system tests. If engine
RPM is above or below the specified speed during a test, you will need to
adjust the expected hydraulic performance parameters (aprox. 3% per 100
engine rpm at full throttle)
IMPORTANT
Hydraulic component output volume relates directly to engine RPM.
For every 100 engine rpm the following component output volumes
will change by the volume listed.
• Traction Pump: 100 engine RPM = 3.8 liters (1 gallon or 129 ounces) of
hydraulic fluid displaced per minute
• Gear Pump (P3): 100 engine RPM = 1.7 liters (0.45 gallon or 57 ounces) of
hydraulic fluid displaced per minute.
• Gear Pump (P4): 100 engine RPM = 1.1 liters (0.29 gallon or 37 ounces) of
hydraulic fluid displaced per minute
6. When you use a hydraulic tester (pressure and flow), ensure that the inlet and
outlet hoses are properly connected and not reversed to prevent damaging
the hydraulic tester or components.
7. When you use a hydraulic tester (pressure and flow), open the tester load
valve fully before you start the engine to reduce the possibility of damaging
the components.
8. Install the hydraulic fittings by hand and ensure that they are not
cross-threaded before you tighten them with a wrench.
9. Position any test hoses away from parts that may move during the test
procedure.
10. After you connect the test equipment, check the hydraulic-fluid level in the
hydraulic tank and ensure that the fluid level is correct.
11. Perform all the hydraulic tests with the hydraulic fluid at normal operating
temperature.
Outcross 9060
Page 5–35
Hydraulic System: Testing the Hydraulic System
18234SL Rev B
Summary of Contents for 07511AA
Page 4: ...Reader Comments Page 4 Outcross 9060 18234SL Rev B ...
Page 18: ...Safety Safety and Instructional Decals Page 1 10 Outcross 9060 18234SL Rev B ...
Page 38: ...Specifications and Maintenance Special Tools Page 2 20 Outcross 9060 18234SL Rev B ...
Page 96: ...Engine Service and Repairs Page 4 24 Outcross 9060 18234SL Rev B ...
Page 208: ...Hydraulic System Service and Repairs Page 5 112 Outcross 9060 18234SL Rev B ...
Page 294: ...Electrical System Service and Repairs Page 6 86 Outcross 9060 18234SL Rev B ...
Page 384: ......