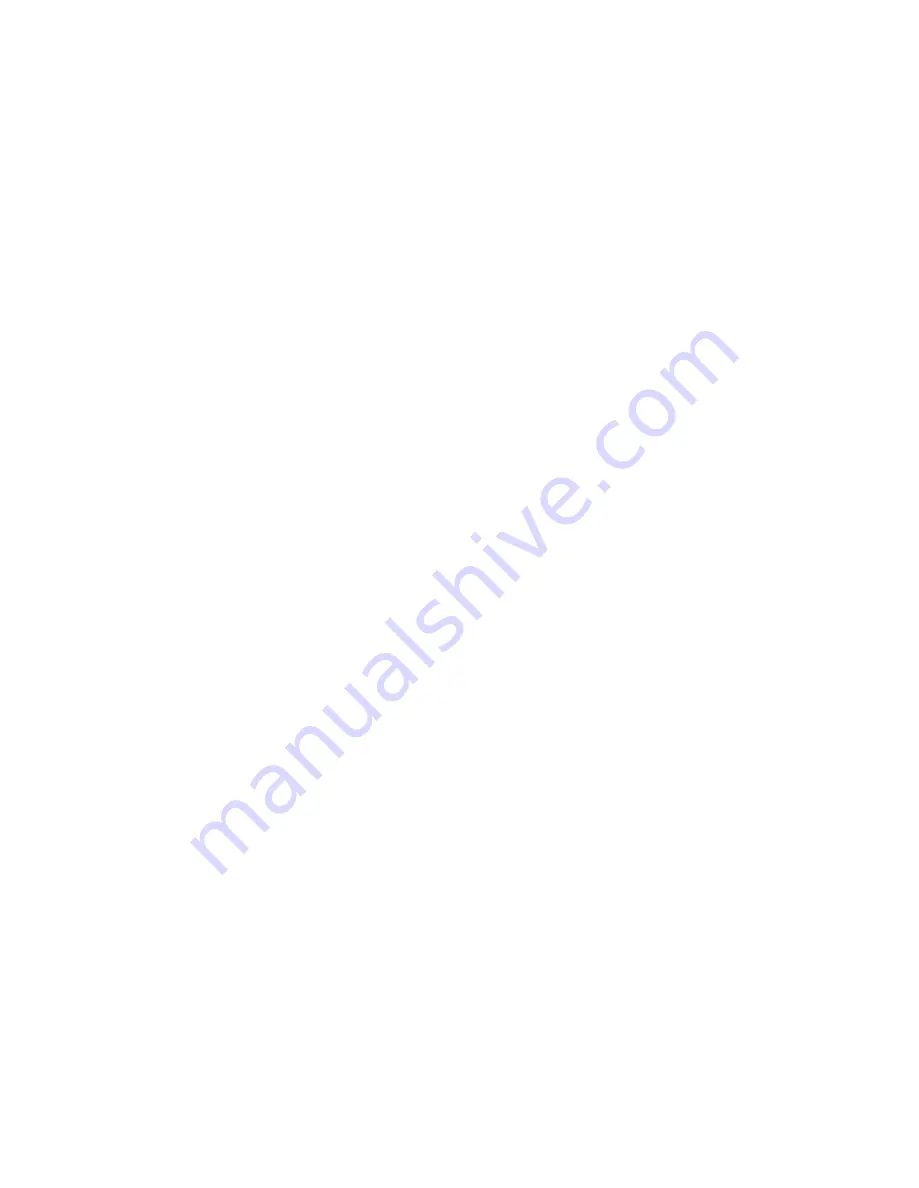
2-2
2.2.3 Air Supply (if used without pneumatic cart)
The 2500's pneumatic system requires an air supply that is clean and oil free. If the generator
is to be used without the pneumatic cart, instrument air at a maximum pressure of 175 PSIG
and capable of a flow rate of at least 20 L/min is recommended. The air supply should be
filtered to a partical size of 0.5 microns or less, a hydrocarbon content of 1 PPM or less, with
a pressure dewpoint of 15 °C or less.
2.2.4 Distilled Water Supply
The 2500 humidity generator requires one gallon (3.8 liters) of double distilled water per fill.
A one gallon supply can last from 12 hours to as many as 6800 hours of continuous use
depending upon the temperature and humidity at which the generator is operated (reference
section 1.6.5). During operation near ambient temperature and 50% RH, one gallon should
last for approximately 290 hours.
2.3 PREPARATION
2.3.1 Chamber Fluid Filling
Reference Fig 2-2 and Drawings 97D25924 & 91S25917
Temperature conditioning of the 2500 test chamber utilizes a 60-70% mixture of propylene
glycol and 30-40% water as the heat transfer fluid. This fluid is circulated by a magnetically
coupled centrifugal pump through the refrigeration and heating system and the fluid shell
surrounding the test chamber.
2.3.1.1 Chamber Fluid Filling Procedure
Chamber fluid filling requires:
T10 Torx Driver (supplied)
Chamber fill funnel (insert into the 5/8" (15.9mm) diameter opening) (supplied)
3 US gallons (11.35 liters) of -100 °C propylene glycol mix (4 US gallons (15.14 liters) for
2500ST) (supplied)
To fill chamber fluid jacket proceed as follows:
1)
Remove top right console panel (panel above chamber).
2)
Locate fluid fill port (under insulation and labeled "Fluid Fill Port").
3)
Remove "Red" cap and insert the chamber fill funnel into fluid fill port.
4)
Using 3 U.S. gallons of -100 °C propylene glycol mix (4 U.S. gallons for
2500ST),
fill until level is approximately 1/4" (6.35 mm) below the bottom
of the fill port. Note: the fluid should touch the base of the funnel.
5)
Remove funnel and replace fluid fill port cap and insulation.
6)
Replace top right console panel.
7)
Chamber fluid filling is now complete.
See figure 2-2