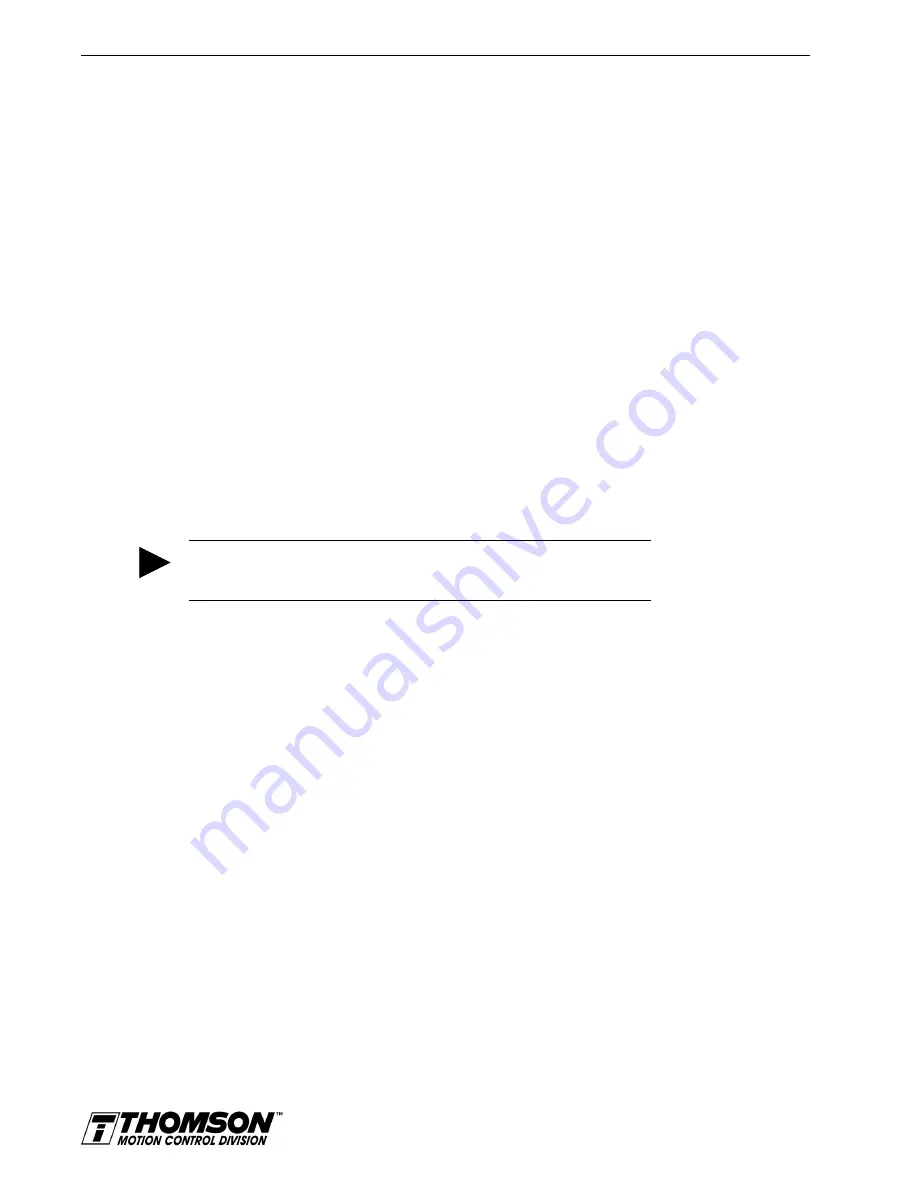
C-2
Electromagnetic Compatibility Guidelines for Machine Design
The EMI model provides only three options for eliminating the EMC problem:
•
reduce the EMI at the source,
•
increase the victim’s immunity to EMI (harden the victim), or
•
reduce or eliminate the coupling mechanism.
In the case of servo drives, reducing the EMI source requires slowing power semiconductor switching
speeds. However, this adversely affects drive performance with respect to heat dissipation and speed/
torque regulation. Hardening the victim equipment may not be possible, or practical. The final, and often
the most realistic solution is to reduce the coupling mechanism between the source and victim. This can
be achieved by filtering, shielding and grounding.
Filtering
As mentioned above, high frequency energy can be coupled between circuits via radiation or conduction.
The AC power wiring is one of the most important paths for both types of coupling mechanisms. The AC
line can conduct noise into the drive from other devices, or it can conduct noise directly from the drive
into other devices. It can also act as an antenna and transmit or receive radiated noise between the drive
and other devices.
One method to improve the EMC characteristics of a drive is to use an isolation AC power transformer
to feed the amplifier its input power. This minimizes inrush currents on power-up and provides electrical
isolation. In addition, it provides common mode filtering, although the effect is limited in frequency by
the interwinding capacitance. Use of a Faraday shield between the windings can increase the common
mode rejection bandwidth, (shield terminated to ground) or provide differential mode shielding (shield
terminated to the winding).
One alternative to AC line filters to reduce the conducted EMI emitting from the drive. This allows nearby
equipment to operate undisturbed. In most cases an AC line filter will not be required unless other sensitive
circuits are powered off the same AC branch circuit. The basic operating principle is to minimize the high
frequency power transfer through the filter. An effective filter achieves this by using capacitors and
inductors to mismatch the source impedance (AC line) and the load impedance (drive) at high frequencies.
For drives brought into use in Europe, use of the correct filter is essential to meet emission requirements.
Detailed information on filters is included in the manual and transformers should be used where specified
in the manual.
AC Line Filter Selection
Selection of the proper filter is only the first step in reducing conducted emissions. Correct filter instal-
lation is crucial to achieving both EMI attenuation and to ensure safety. All of the following guidelines
should be met for effective filter use.
1. The filter should be mounted to a grounded conductive surface.
2. The filter must be mounted close to the drive input terminals. If the distance exceeds 1 foot, then
a strap should be used to connect the drive and filter, rather than a wire.
3. The wires connecting the AC source to the filter should be shielded from, or at least separated
from the wires (or strap) connecting the drive to the filter. If the connections are not segregated
from each other, then the EMI on the drive side of the filter can couple over to the source side of
the filter, thereby reducing, or eliminating the filter effectiveness. The coupling mechanism can
be radiation, or stray capacitance between the wires. The best method of achieving this is to
TIP
“Common mode” noise is present on all conductors referenced to ground.
“Differential mode” noise is present on one conductor referenced to another
conductor.
Artisan Technology Group - Quality Instrumentation ... Guaranteed | (888) 88-SOURCE | www.artisantg.com