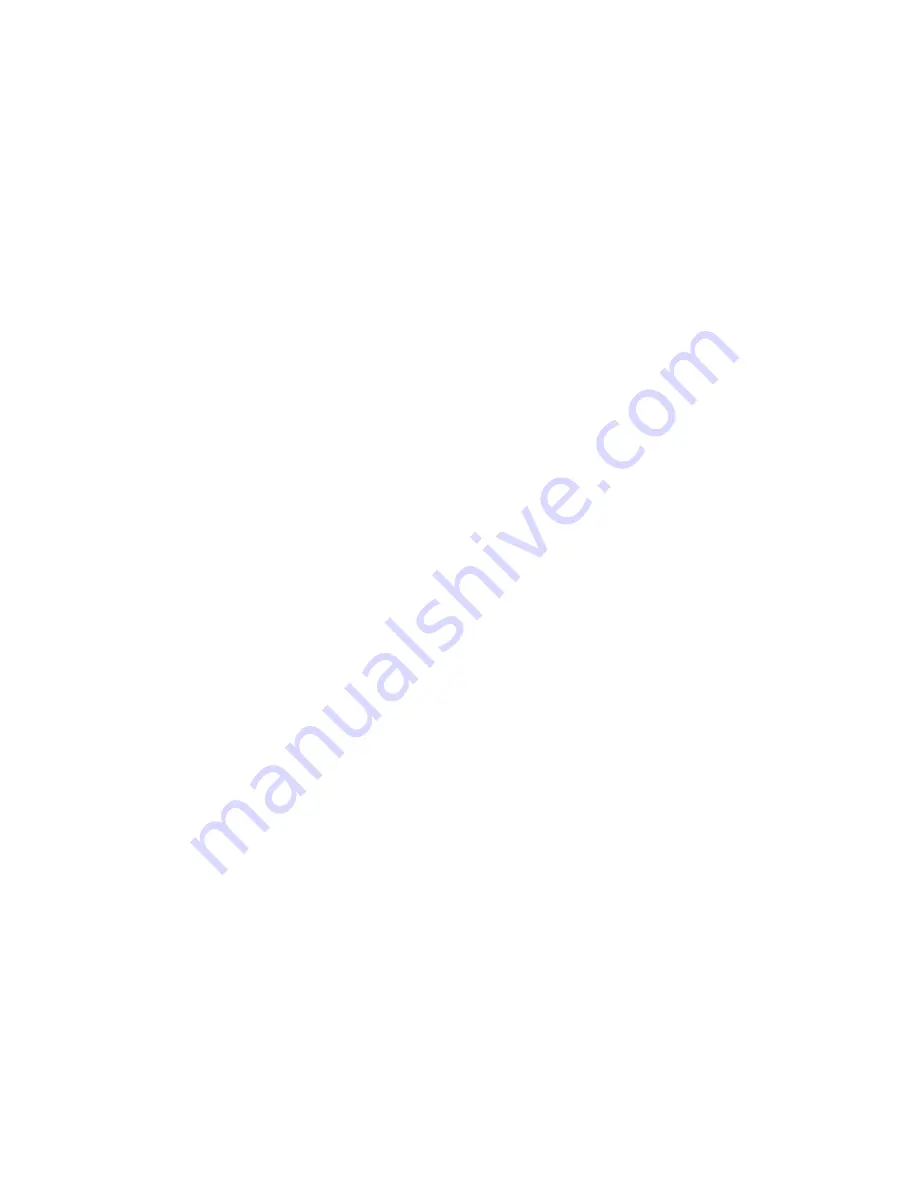
Troubleshooting
Communication Errors
6-6
Omni FTIR Multi Gas CEMS Instruction Manual
Thermo Fisher Scientific
●
Check for 24 VDC signal on temperature alarm connections to
probe off of the electrical panel using a multimeter. If only one
connection has 24 VDC, check temperatures at probe.
●
System in failsafe mode – zero air
●
Check alarm system continuity at sample probe, umbilical
wiring and temperature control box. See Chapter 7, “
System
Component Description
” and Appendix D, “
Calogix Setup
”.
●
Check Calogix software for correct software setup for alarm
states; see Appendix D, “
Calogix Setup
”.
●
“Last Pressure” reading in ‘Status’ on ImaccMonitor software main
screen reads 750.000000.
●
Check virtual com port number (See Appendix D, “
Calogix
Setup
”).
●
Check USB connection between PC and temperature
controller.
●
Stop and re-start script in ImaccMonitor.
External communications errors
●
Ethernet not communicating
●
Check IMACC Modbus TCP server running on PC.
●
Check power LED on ADAM hub Chapter 7, “
System
Component Description
”. If off, check 24 VDC breaker and
wiring to and from power supply.
●
Check Ethernet cable between computer and ADAM hub; see
Chapter 7, “
System Component Description
”.
●
Serial
●
Check IMACC Modbus TCP server running on PC.
●
Check serial cable connection.
●
Check ‘Hardware’ setup in Windows system menu.
Internal communications errors
●
No temperature readings or heating of system components
●
See ‘Temperature errors’ in this chapter.
●
No communications with FTIR
Communication
Errors
Summary of Contents for Omni FTIR Multi Gas CEMS
Page 1: ...Omni FTIR Multi Gas CEMS Instruction Manual Part Number 108004 00 11Apr2013...
Page 4: ...Thermo Fisher Scientific WEEE Compliance...
Page 20: ...Figures xvi Omni FTIR Multi Gas CEMS Instruction Manual Thermo Fisher Scientific...
Page 22: ...Tables xviii Omni FTIR Multi Gas CEMS Instruction Manual Thermo Fisher Scientific...
Page 182: ......
Page 206: ......
Page 216: ......
Page 234: ......