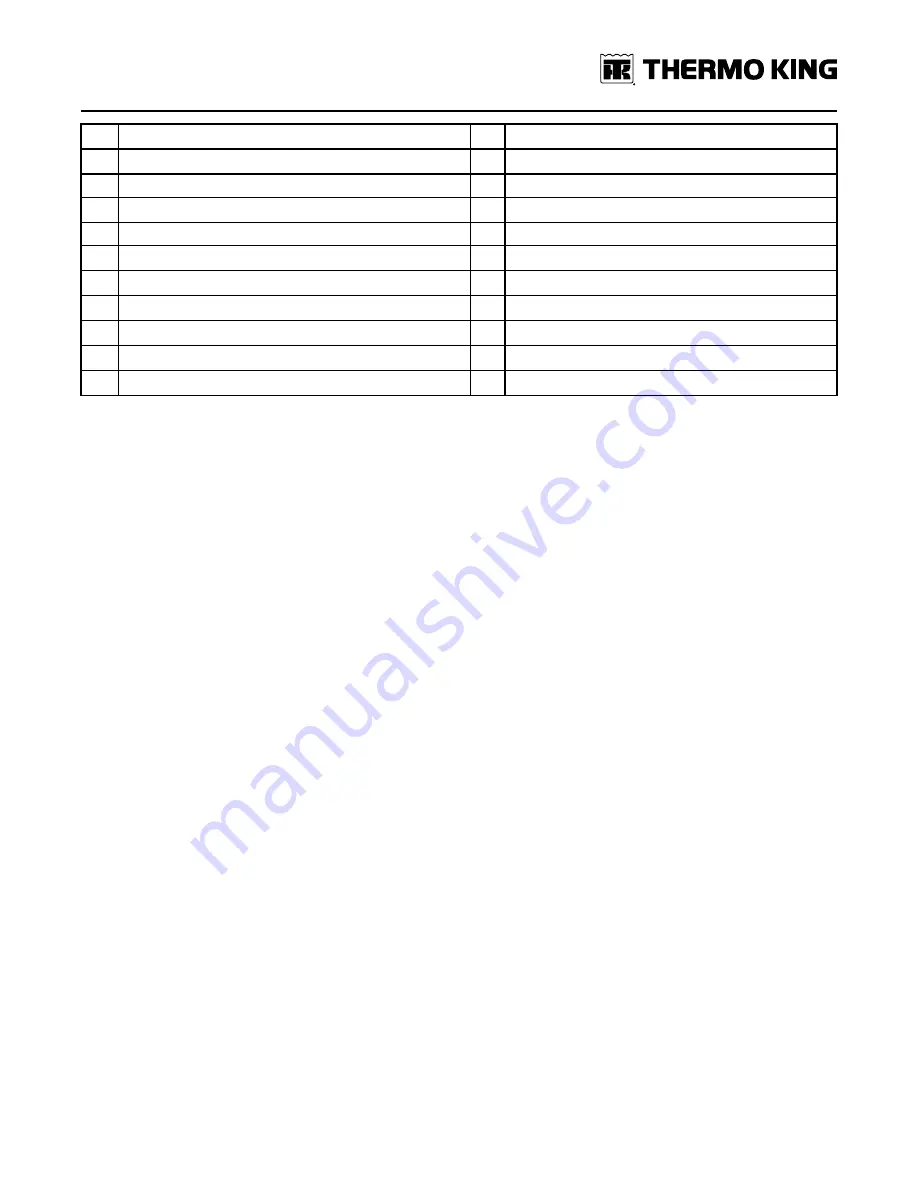
TK 61555-2-MM-EN
89
6.
Valve and cover screw
22.
Restriction Fitting
7.
Flatwasher
23.
Discharge Manifold
8.
Suction valve
24.
Manifold Screw
9.
Valve Cap
25.
Pipe Plug
10.
Gasket
26.
Plate Cover
11.
Sealing Washer
37.
Cover Gasket
12.
Valve O-Ring
28.
Schrader Valve
13.
Suction Transducer
29.
O-ring seal adapter
14.
Suction Valve adapter
30.
O-ring
15.
Adapter O-Ring
31.
Adapter Cap
16.
Discharge Valve screw
Compressor
Removal
1. Pump down the compressor and equalize the pressure to 0 psig (0 bar). Verify that pressure
holds 0 psig and front seat the discharge and suction service valves to isolate the compressor
from the circuit. Recover remaining refrigerant from the compressor before moving to next
steps.
2. Loosen and remove the compressor/electric motor belt from the Electric Motor pulley.
3. Unbolt and remove compressor oil filter bracket from flywheel housing (optional).
4. Unbolt the discharge valve and the suction valves from the compressor.
5. Keep the compressor ports covered to prevent dust, dirt, etc., from falling into the
compressor.
6. Disconnect all high pressure cutout switch wires. Disconnect the pilot solenoid valve line.
Remove compressor belt guard.
7. Support compressor and remove the compressor mounting bolts from flywheel housing.
8. Lift the service valves out of the way.
9. Slide the compressor to the left until coupling pins are clear.
10. Remove the compressor from the front of the unit.
N
No
otte
e:: When the compressor is removed from the unit, note the oil level or measure the oil
removed from the compressor. Add the same amount of oil to the replacement
compressor.
11. Remove clutch from compressor crankshaft on Model 50 units, from drive coupling on Model
30 units.
Installation
1. Replace clutch from compressor crankshaft on Model 50 units, or on drive coupling on Model
30 units.
2. Lift compressor into the unit and install the mounting bolts.
N
No
otte
e:: The 8-pin compressor drive hub will only slide onto the coupling pins in one of two
positions that are 180 degrees apart.
3. Install suction and discharge service valves and torque to the correct value. Coat new o-ring
or gasket with compressor oil. Connect the high pressure cutout switch wires.
4. Reconnect the pilot solenoid valve and compound pressure gauge lines.
5. Pressurise the compressor and test for refrigerant leaks.
6. If no leaks are found, evacuate the compressor. Replace the compressor/electric motor belt