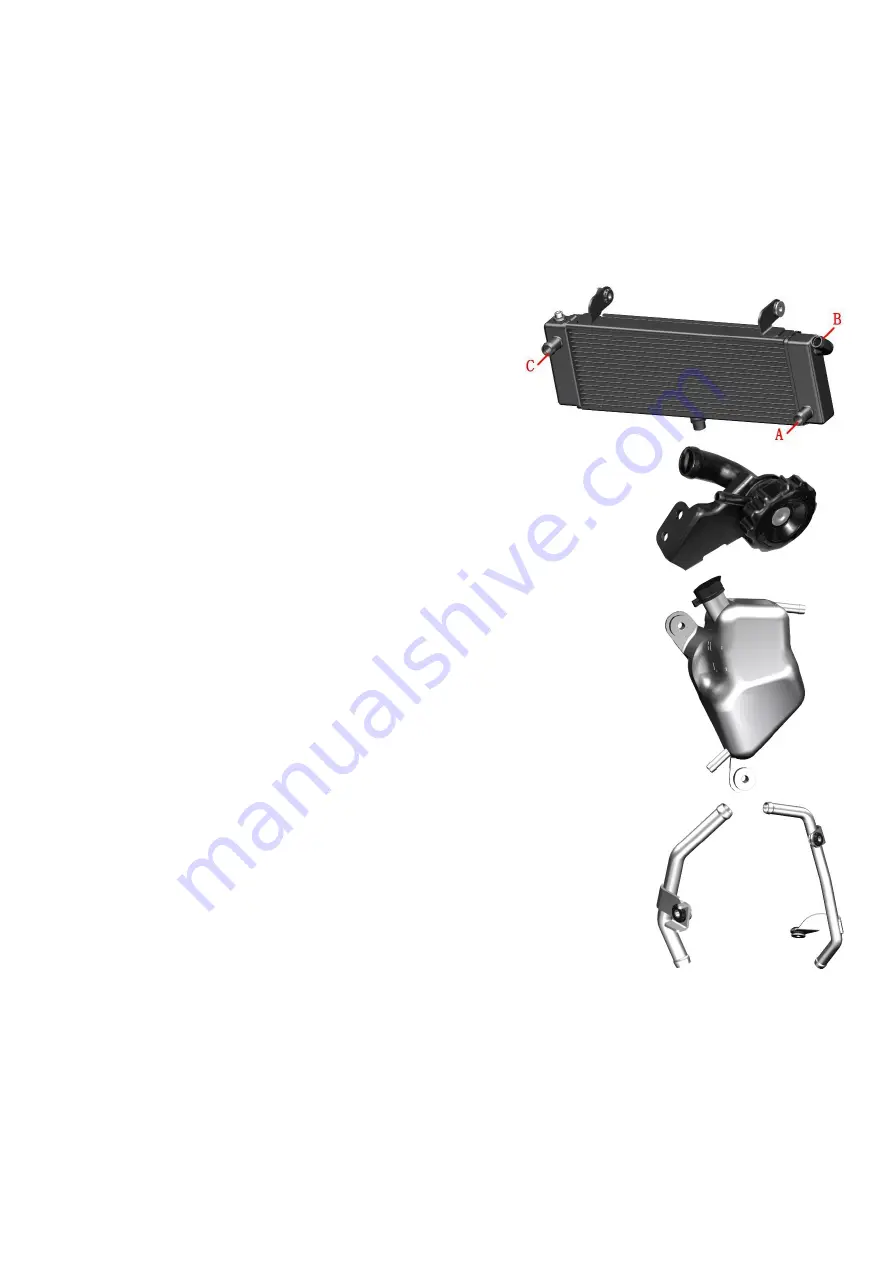
137
/
188
●After the soaking inspection is completed, the water stains should be wiped clean in time, or use a dust blower to blow dry.
If
the main water tank and the small water tank are blown dry by blowing dust loose, the wind pressure should not be too large
and should be far away from the radiating fins to avoid damage or deformation of the radiating fins.
●Except the gas pressure is specifi
ed when doing the air tightness test, the compressed air of 160kPa (1.63 Kgf/cm2, 23.2 psi)
shall be introduced, and the parts shall be immersed in water and left for 10s without bubbles. If there are bubbles, the air leaks
and needs to be replaced.
●The h
eat dissipation fins are allowed to have a small amount of lodging deformation. If the lodging area is too large, it will
affect the heat dissipation effect, and it is recommended to replace it. A small amount of deformation can be corrected with a
small flat-blade screwdriver.
●It is forbidden to use high
-pressure water gun or high-pressure air to directly flush or blow the heat sinks of the main water
tank and the small water tank.
●Before further testing, check the appearance for signs of leakage. If
there is a slight leakage, try to repair it, otherwise it should
be replaced.
1. Main water tank(M310)
Check whether the cushion rubber is aging and cracked.
Block the A and C ports with a self-made cap, and check the tightness by
ventilating from the B port.
Compressed air with lower air pressure can be blown from the back to
the water tank from a long distance to clean up foreign objects on the
surface. Or use a low-pressure water gun to spray the radiating fins from a
long distance to clean up foreign objects on the surface.
2. Attention to the water tank filling port(M310)
Caution:
●Special ventilation tooling (gas pressure reducing valve, air gun, sealing tube) is required for
testing.
●After the soaking inspection is completed, the water stains should
be wiped clean in time.
2.1 Overall leak check
Seal the small tube and ventilate the large tube for air tightness inspection.
2.2 Check of pressure relief valve
Pass 120kPa (1.22 Kgf/cm2, 17.4 psi) compressed air into the big pipe, put the water filler into
the water and let stand for 10 seconds. The small pipe should be free of bubbles. Increase the
compressed air to
130kPa (1.33 Kgf/cm2, 18.9 psi). Bubbles appear.
3. Auxiliary water tank
First check whether the rubber cover is aging and cracked, if any, replace it. If the appearance
is good, then check the air tightness.
Seal the two small water outlets and open the black plastic cover of the water tank for air
tightness inspection.
Continue to seal the small water outlet, fill the auxiliary tank with water and turn the auxiliary
tank upside down, and observe whether the rubber cover of the water tank seeps. If there is
seepage, it is unqualified. Pour out the water after checking the tightness, remove the plug and
let the auxiliary water tank dry naturally or blow it dry with a dust blower.
4. Aluminum inlet pipe and aluminum outlet pipe(M310)
Check whether the weld is cracked or cracked; check whether the buffer rubber is aging and
cracked. If the appearance is good, then check the air tightness.
Seal one end and ventilate from the other end to check air tightness.
5. Small water tank(M310)
Check whether the fan and net cover are firmly assembled, and there should be no jamming
of the rotating fan blades. Check whether the cushion rubber is aging and cracked. Check whether the fan cable is damaged.
Seal one water outlet and ventilate from the other end for air tightness inspection.
The blue of the fan plug is the positive pole, and the black is the negative pole. Find a battery with sufficient power and
connect the wires according to the positive and negative poles, and check whether the fan draws air backwards.
Compressed air with lower air pressure can be blown from the back to the water tank from a long distance to clean up foreign
objects on the surface. Or use a low-pressure water gun to spray the radiating fins from a long distance to clean up foreign
objects on the surface.
Summary of Contents for ZONTES 310T-M 2022
Page 1: ...1 188 ZT125 310T M Maintenance Manual 2022 09 14 ...
Page 91: ...91 188 l So far the adjustment operation of the valve clearance is completed ...
Page 115: ...115 188 Electrical schematic diagram of EFI system ...
Page 156: ...156 188 Exploded view of front fork components M125 310 Directional exploded view ...
Page 173: ...173 188 ...