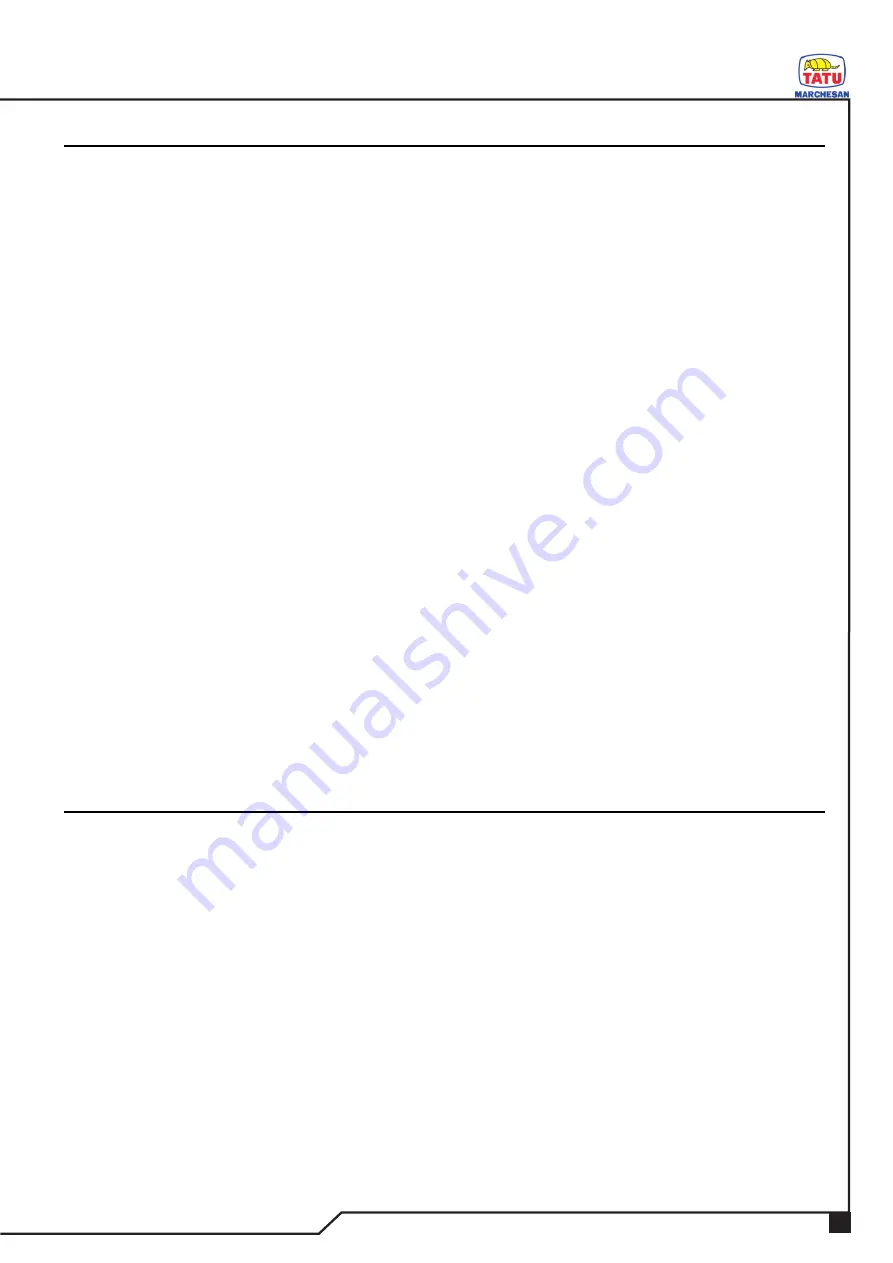
15
PMT - Rev. 05 - Sep/22
The PMT corn head features a interchangeable frame with all models of national and
international combine harvesters through the use of a specific frame for the coupling of the
straw elevator. This system allows that a single operator performs the job. It also levels the
equipment during the harvest.
Light and resistant platforms provide high speed and demand less effort from the
hydraulic system. The lateral transmission is easy to access through the opening of the
lateral lid.
Lowest attack angle among competition with just 13°.
Harvest height of approximately 10 cm from the ground, allowing for harvesting when
the cobble is close to the soil.
Augers with two different coil pitch types that do not allow the cobbles to be crushed
and prevent losses while keeping high rotations. The augers also avoid bindweed bushings.
Advanced, universal and zinc plated gathering chains with seven links each.
The chains tighteners have a squared tube that protects the spring, avoiding that any
impurity gets inside it and prejudice its performance.
The lateral chains are lubricated automatically, decreasing the abrasion caused by the
corn straw and by the friction between the metallic parts.
The pulling rollers are formed by six fins made of high carbon steel, tempered, sharpened
and welded for a greater safety. The tips of the pulling rollers are unaligned to avoid that
when picking up bedridden crops, the cobs on the ground do not cause bushings, thus
avoiding that any straw enters inside the equipment.
2. To the operator
Intended use of the equipment
1. To avoid damages, serious accidents or death, do NOT allow passengers on any
part of the equipment.
2. The equipment must not be used by an inexperienced operator or one that do not
know every conduction, operation and command controlling techniques.
Prohibited use of the equipment
Summary of Contents for PMT
Page 1: ...OPERATOR S MANUAL PMT PMT...
Page 60: ...58 PMT Rev 05 Sep 22 11 Notes...
Page 62: ...www marchesan com br...