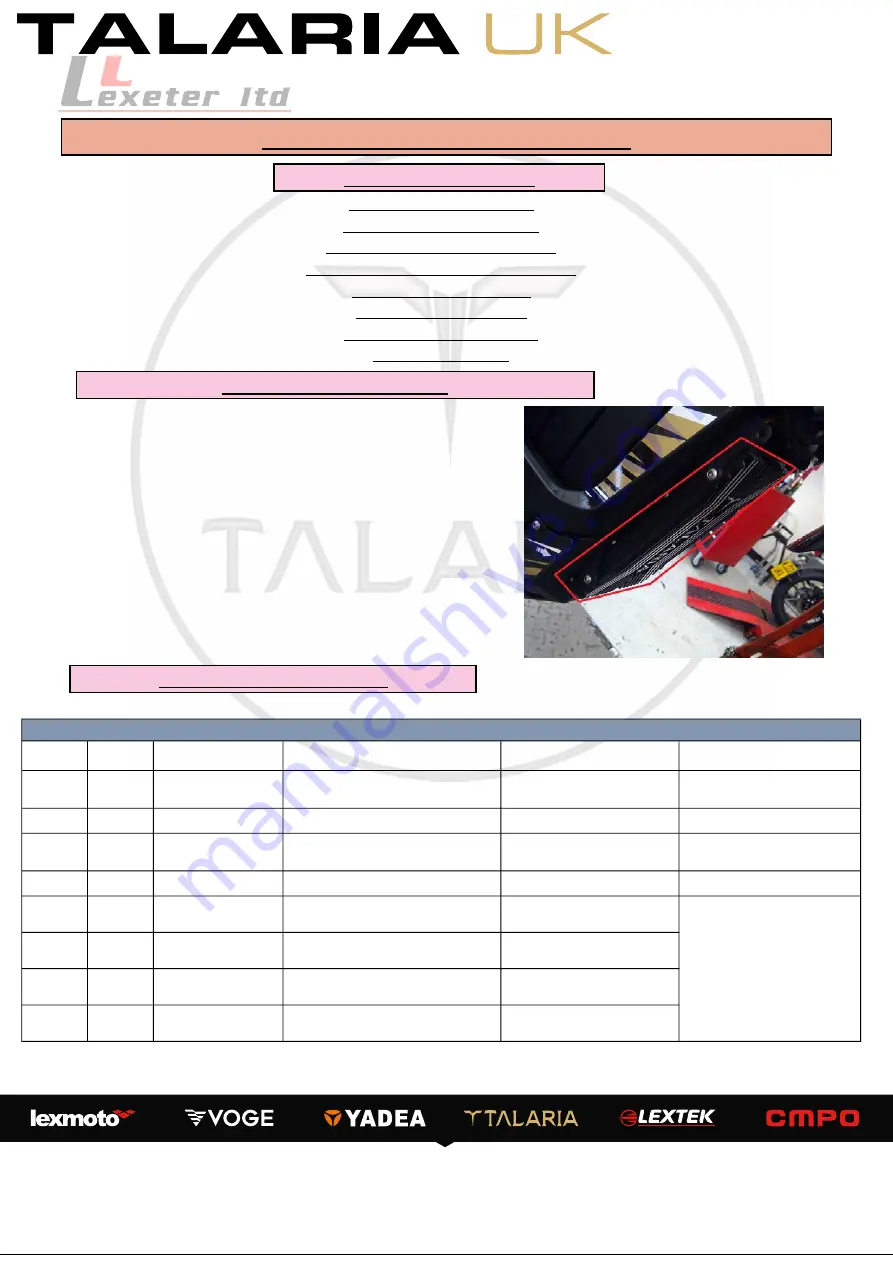
LLEXETER.CO.UK
LLEXETER LTD - UNITS 15-18 GREENDALE BUSINESS PARK - WOODBURY SALTERTON - DEVON - EX5 1EW - UNITED KINGDOM
COMPANY NO: 4940600 / VAT REGISTRATION NO: GB825156925 TEL: 01395 233128
5 Electronic Power-train
The Talaria Sting L1e utilises a proprietary motor
controller developed in house by Talaria and
uses a 3 phase control system to power the motor
combined with a Hall effect sensor system to
monitor both rotation direction and rotation speed
in the motor itself.
The Controller is located at the lower front of the
motorcycle chassis.
Chapter Contents
5.1 : Motor Controller
5.2 : Diagnostic Codes
5.3 : Motor Control Testing
5.4 Battery and Circuit Breaker
5.5 : Throttle Control
5.6 : Ignition Switch
5.7 : DC-DC Converter
5.8 : Tilt Sensor
5.1 Motor Controller
Error Code
TL3000
Error Code
TL45
Description
Possible fault
Solution
Remarks
E01
00001
Protection IC error
The inner communication of the chip is disconnected
Re-start the bike
Check all the CANbus wiring connections and
wiring to the battery, dashboard and motor
controller. Repair as necessary.
E02
00002
Battery cell connection wire
disconnected.
Internal battery cell connection failure
Re-start the bike
If fault persists, replace the battery
E03
00003
Voltage of battery cells are not
balanced.
The difference of battery cells is more than 500mV, this
error code will display on the dash.
Fully charge the battery
Re-start the bike
It may be necessary to cycle discharging and
recharging the battery 2-3 times. If fault
persists, replace the battery
E04
00004
Battery capacity measurement
error
Not applicable
/
E05
00005
Storage error
Internal storage error
Re-start the bike
E06
00006
Time display error
Internal clock failure
Re-start the bike
E07
00007
Discharge MOS error
Discharge circuit failure
Re-start the bike
E08
00008
Charge MOS error
Charging circuit failure
Re-start the bike
Troubleshooting
If fault persists, replace the controller
5.2 Diagnostic Codes