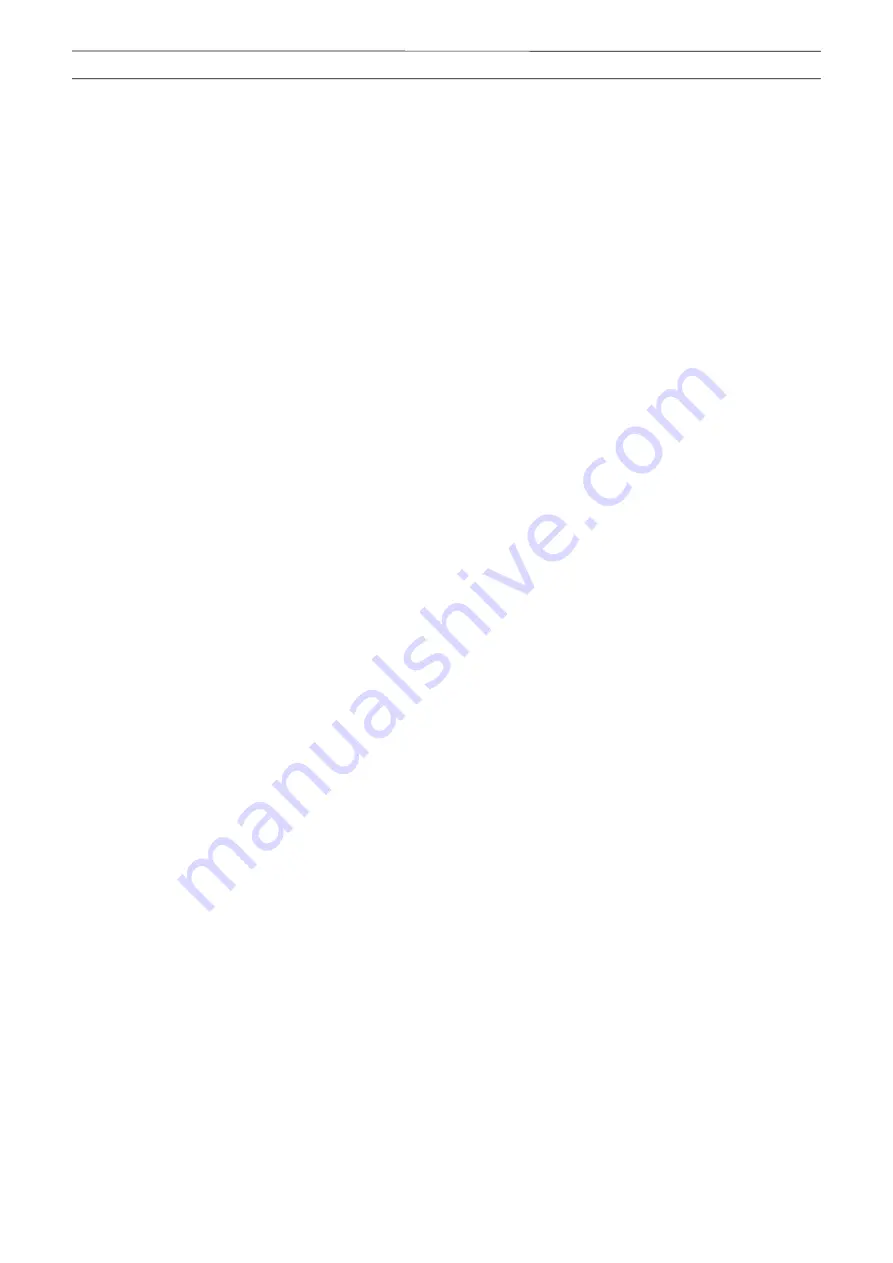
73
W301-0411E
Chapter B
Chapter B
User Mode
7.4.3 Information Relevant to Winch Drum Position Selection
(1) Specification selection flag
- A lifting capacity setting, winch position selection (#17200-53)
- Winch drum position selection effective flag (#17200-79)
- Winch drum selection method setting (#17200-96)
(2) By-models data
- Frame adjustment data (#10302)
(3) Winch drum select icon (#17204-62)
When the selection method (1) is employed, the winch selection status toggles between "front/rear" and
"front" every time the F3 or F4 key is pressed.
"Front" represents the condition that the auxiliary hook block is attached on the main wire rope
(i. e., the auxiliary winch is wound up all the way and the main hook block is detached.)
"Front/rear" represents the condition that the main hook block is attached on the main wire
rope and the auxiliary hook block is on the auxiliary wire rope.
(4) User preset menu (Refer to Chapter B, “4-5-6 Selection of winch to be used”)
(5) Boom and jib status setting (Refer to Chapter B, “2-2 Registration of Crane State”)
(6) Winch drum position selection adjustment menu (Refer to Chapter D, “4-1 Winch drum position selection”)
7.4.4 Output
(1) Models using user preset menu for winch position change
- Winch drum position icon display to normal operation status screen (Fig. 7.7.3, Fig. 7.7.4)
- Winch drum position icon display to integrated display screen
7.4.5 Processing Contents
(1) Models using user preset menu for winch position change
The winch drum position adjustment value is set in the adjustment menu. Then, the winch drum position is
determined in accordance with the adjustment value and with the boom and jib operating status, and the
rated capacity is determined. When the adjustment value is set as "Front," by Tadano, therefore, the
selection can be made by the winch drum position selection menu of user preset menu.
Adjustment value:
-Winch drum position adjustment value selection method = " Front — Front/Rear" (1)
Winch position = Front and Rear ... Main boom lift status: Front position,
S/T and jib lift status: Rear position
Winch position = Front ……………. Main boom lift status: Front position,
S/T and jib lift status: User preset menu selection