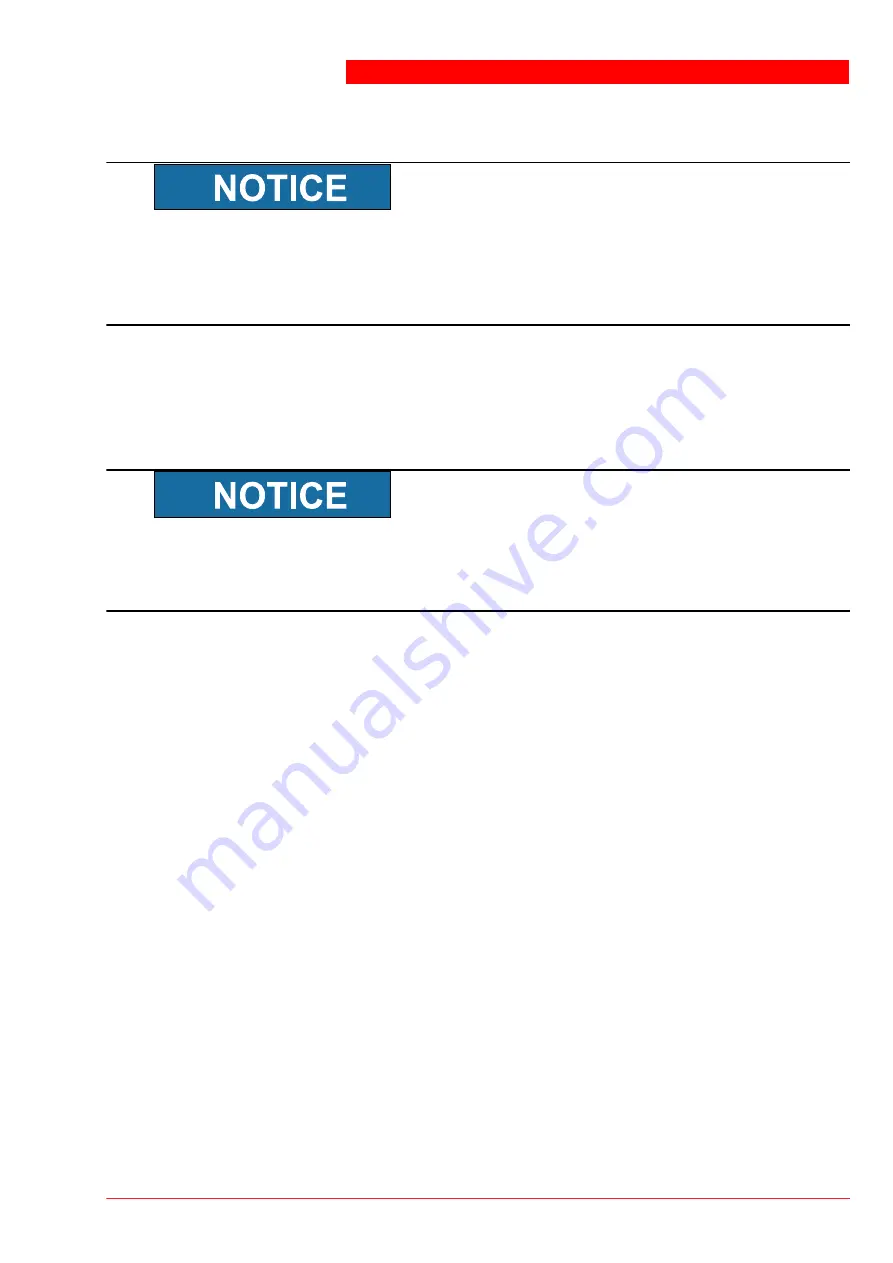
Installation and Service Manual
49
SK 2055 / 2070 / 2090
This setting remains active for 10 minutes, after which the safe limit monitoring
is automatically reactivated. The setting will not be saved in the EEPROM,
which means that the safe limits will always be active after starting and
stopping.
7.6 Code 66 - Potentiometers disabled
This option allows the functioning of the potentiometers to be checked. This
option replaces the value on the potentiometer input by a constant value. The
lift will function normally, but without elevation differences being corrected.
This setting remains active for 2 minutes, after which safe limit monitoring is
automatically reactivated. The setting will not be saved in the EEPROM, which
means that the safe limits will always be active after starting and stopping.
7.7 Code 67 - Adjusting potentiometers
This programme aligns the resistance tolerances for the individual
potentiometers.
The potentiometer circuit is monitored electronically and the vehicle lift is
disabled if there is a difference of more than 3%. Error code 16 appears in the
display to show it has been disabled.
The potentiometers should be adjusted with the guide pieces at half the
maximum lifting height (distance of approx. 900 mm between the underside of
the guide pieces and the base plates).
The potentiometers should also be readjusted after one or both potentiometers
have been replaced.
Motor runtime counter
A two-digit number appears after code 67 showing the number of operational
hours the motor has run (100 hours is approx. 12,000 lifts). This is recorded in
the EEPROM.
Summary of Contents for Freedomlift SK 2055
Page 108: ...Installation and Service Manual 108 SK 2055 2070 2090 14 2 Electrical diagram 3 x 230V ...
Page 109: ...Installation and Service Manual 109 SK 2055 2070 2090 14 3 Electrical diagram 3 x 400V ...
Page 113: ...Installation and Service Manual 113 SK 2055 2070 2090 14 6 Dimensions SK 2055 3 piece arms ...