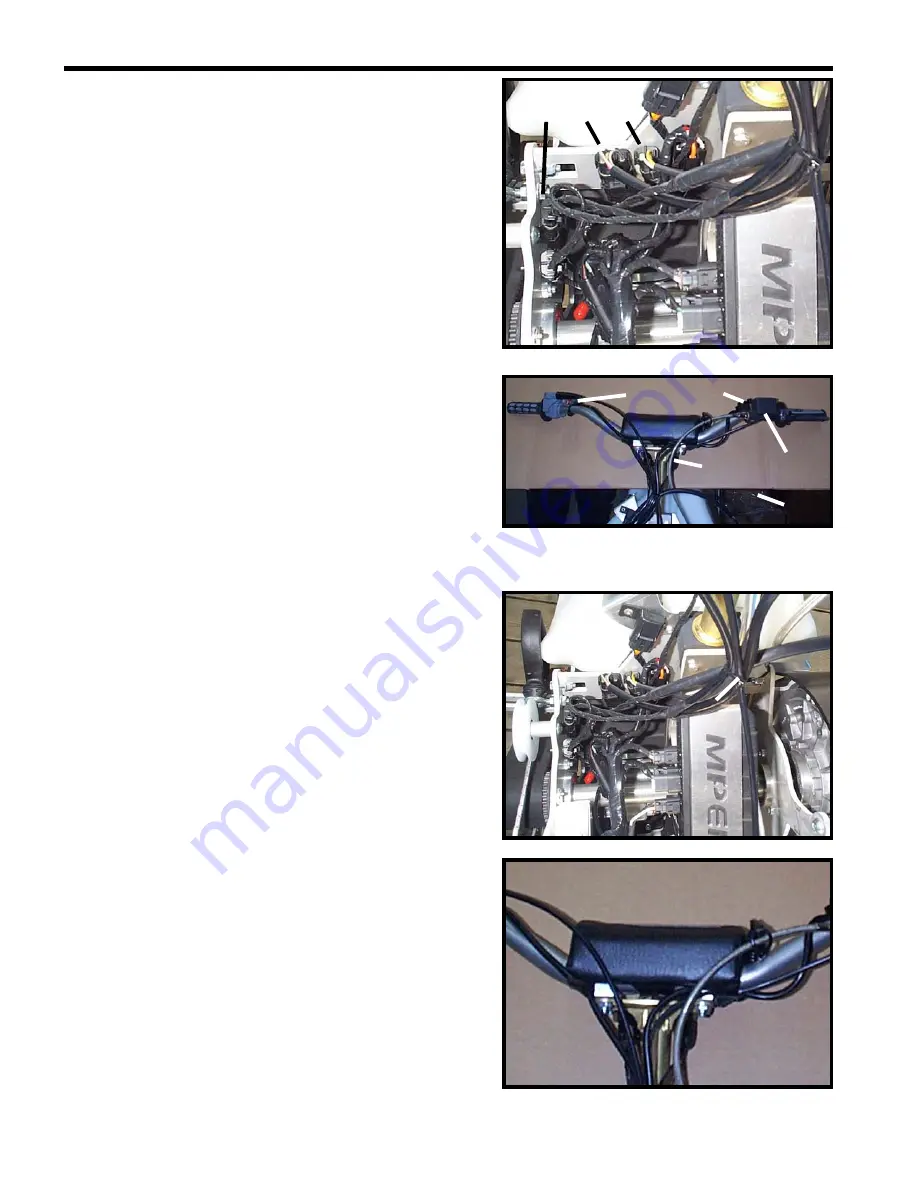
WIRE, CABLE AND HOSE ROUTING 16-6
Handlebar-Mounted Devices/Switchgears
1. Brake
switch
The 2-circuit connector from the brake switch (YL and
YL/WT wires) connects to the 2-circuit connector on the
main wiring harness (YL and WT wires).
2. Dimmer
switch
The 3-circuit connector from the dimmer switch (GY, RD/YL
and GY/BK wires) connects to the 3-circuit connector on the
main wiring harness (GY, YL and VI/WT).
3. Tether
switch
The 2-circuit connector from the tether switch (BK and
BK/YL wires) connects to the 2-circuit connector on the
main wiring harness (BK and BK/YL wires).
4. Emergency stop switch
The 2-circuit connector from the emergency stop switch (BK
and BK/YL wires) connects to the 2-circuit connector on the
main wiring harness (BK and BK/YL wires).
5. Headlamp Connector
Once all of the connectors are seated, group the handlebar
accessory, headlamp and throttle cable together with a nylon tie
wrap. MAKE SURE that this grouping does not affect the cycling
of the throttle cable or the steering of the vehicle in any way.
Place the emergency stop switch, the dimmer switch and the
brake switch wires underneath the crashpad as shown at right.
1
2
3
4
5
1
2
3
Tie wrap
Summary of Contents for 600HO
Page 1: ...MY2004 Set up Service and Shop Manual SNOW HAWK 600HO...
Page 28: ...PERIODIC MAINTENANCE 2 11 Symbols used on the NGK spark plugs...
Page 32: ...FUEL SYSTEM 3 3 CARBURET0RS TM 40...
Page 53: ...REWIND STARTER 5 1 REWIND STARTER...
Page 59: ...COOLING SYSTEM 6 1 COOLING SYSTEM 1 2 3 4 5 6 7 8 9 10 11 12 12 12 12 12 12 12 12 12...
Page 67: ...ENGINE CYLINDERS HEAD BASE 7 4 ENGINE CRANKSHAFT AND PISTONS...
Page 69: ...ENGINE CYLINDERS HEAD BASE 7 6 ENGINE TOP END...
Page 89: ...ENGINE CYLINDERS HEAD BASE 7 26...
Page 127: ...FRONT FORK AND TWIN AXIS SKI 11 1 FRONT FORK...
Page 129: ...FRONT FORK AND TWIN AXIS SKI 11 3 FRONT FORK ASSEMBLY...
Page 145: ...REAR SUSPENSION SHOCKS AND TRACK 12 2 REAR SHOCK 53 67 68 69 70...
Page 146: ...REAR SUSPENSION SHOCKS AND TRACK 12 3 MIDDLE SHOCK 54 73 67 70...
Page 149: ...REAR SUSPENSION SHOCKS AND TRACK 12 6 SHOCK EXPLODED VIEW 11 10 11 9 2 12 13 7 6 8 1 5 3 4...