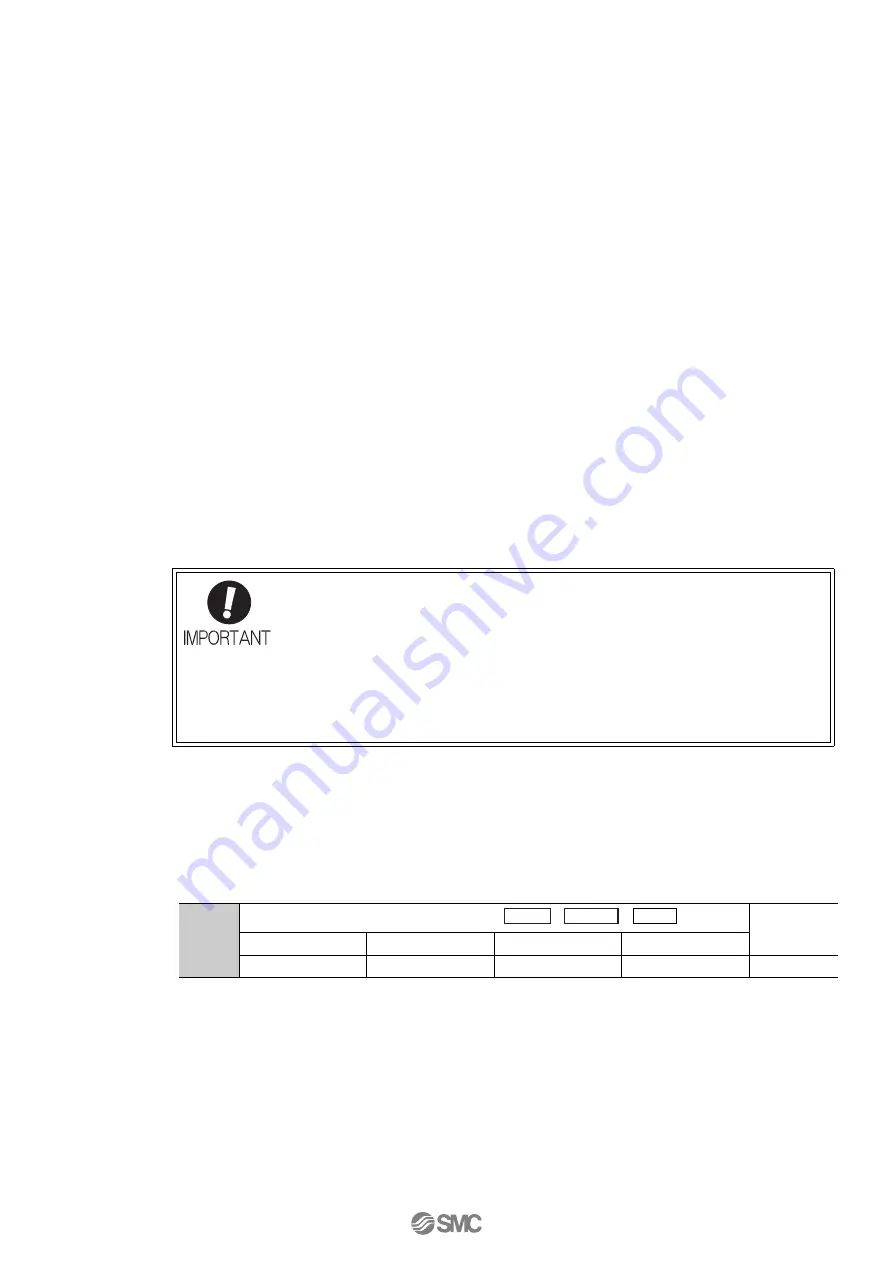
5 Adjustments
5-18
(3) When Advanced Autotuning Cannot Be Performed Successfully
Advanced autotuning cannot be performed successfully under the following conditions. Refer
to
5.4 Advanced Autotuning by Reference (Fn202)
and
5.5 One-parameter Tuning (Fn203)
for details.
•
The operating range is not applicable.
•
The moment of inertia changes within the set operating range.
•
The machine has high friction.
•
The rigidity of the machine is low and vibration occurs when positioning is performed.
•
The position integration function is used.
•
P control operation (proportional control) is used.
Note: If a setting is made for calculating the moment of inertia, an error will result when
P control operation is selected using /V_PPI of the servo command output signals
(SVCMD_IO) while the moment of inertia is being calculated.
•
The mode switch is used.
Note: If a setting is made for calculating the moment of inertia, the mode switch function
will be disabled while the moment of inertia is being calculated. At that time, PI
control will be used. The mode switch function will be enabled after calculating
the moment of inertia.
•
Speed feedforward or torque feedforward is input.
•
The positioning completed width (Pn522) is too small.
• Advanced autotuning makes adjustments by referring to the positioning completed
width (Pn522). If the DRIVER is operated in position control (Pn000.1=1), set the
electronic gear ratio (Pn20E/Pn210) and positioning completed width (Pn522) to the
actual value during operation. If the DRIVER is operated in speed control
(Pn000.1=0), set Mode to 1 to perform advanced autotuning.
• Unless the positioning completed signal (/COIN) is turned ON within approximately
3 seconds after positioning has been completed, "WAITING" will flash. Furthermore,
unless the positioning completed signal (/COIN) is turned ON within approximately
10 seconds, "Error" will flash for 2 seconds and tuning will be aborted.
Change only the overshoot detection level (Pn561) to finely adjust the amount of overshooting
without chang- ing the positioning completed width (Pn522). Because Pn561 is set by default
to 100%, the allowable amount of overshooting is the same amount as that for the positioning
completed width.
When Pn561 is set to 0%, the amount of overshooting can be adjusted to prevent
overshooting the positioning completed width. If the setting of Pn561 is changed, however,
the positioning time may be extended.
Pn561
Overshoot Detection Level
Speed
Position
Torque
Classification
Setting Range
Setting Unit
Factory Setting
When Enabled
0 to 100
1%
100
Immediately
Setup
Summary of Contents for LECYU Series
Page 30: ...1 Outline 1 9 1 4 3 Three phase 200 V LECYU2 V9 Models ...
Page 65: ...3 Wiring and Connection 3 11 3 Wiring Example with DC Power Supply Input DRIVER ...
Page 92: ...3 Wiring and Connection 3 38 External Dimensions Units mm 1 FN Type by Schaffner EMC Inc ...
Page 93: ...3 Wiring and Connection 3 39 2 FN Type ...
Page 143: ...4 Operation 4 44 ...