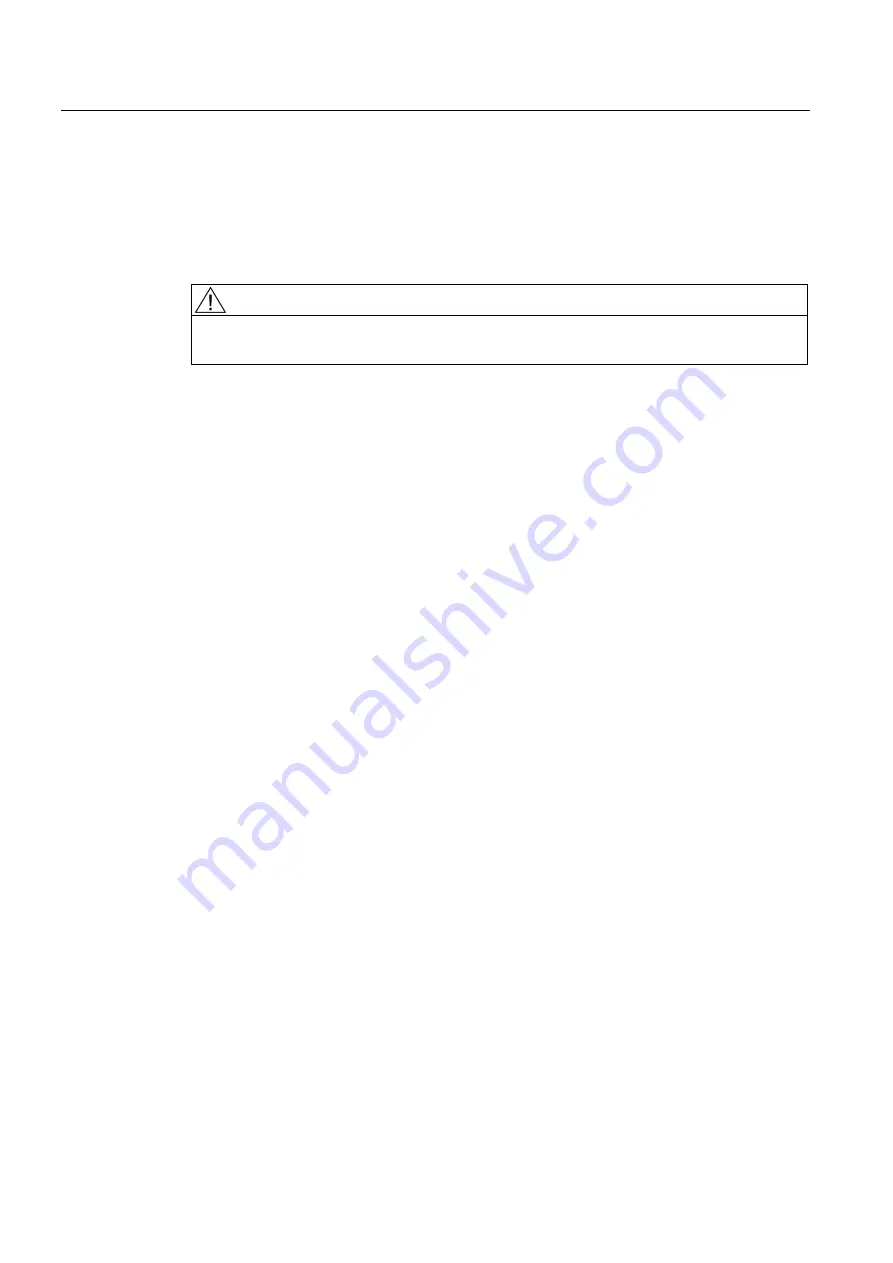
Gantry axes (G1)
6.3 Referencing and synchronizing gantry axes
Turning, Milling, Nibbling
90
Function Manual, 11/2012, 6FC5397-1CP10-5BA0
The forced coupling between the gantry axes can be separated by making the following MD
setting and then performing a RESET:
MD37140 GANTRY_BREAK_UP = 1 (break up gantry grouping)
The gantry axes can then be traversed separately by hand; the monitoring of the warning
and trip limits is not operative in this state.
CAUTION
If the gantry axes remain mechanically coupled, there is a risk of damage to the machine
when the leading or synchronized axes are traversed in this operating state!
6.3
Referencing and synchronizing gantry axes
6.3.1
Introduction
Misalignment after starting
Immediately after the machine is switched on, the leading and synchronized axes may not
be ideally positioned in relation to one another (e.g. misalignment of a gantry). Generally
speaking, this misalignment is relatively small so that the gantry axes can still be referenced.
In special cases (e.g. gantry axes were brought to a standstill because of a disturbance,
power failure, or EMERGENCY OFF), before the axes can be traversed the dimensional
offset must be checked for permissible tolerance values and a compensatory motion
executed if necessary.
To execute this compensatory motion, the gantry grouping must be separated by means of
the following machine data:
MD37140 GANTRY_BREAK_UP (break up gantry grouping)
Gantry synchronization
All gantry axes must first be referenced and then synchronized after the control system is
switched on. During gantry synchronization, all gantry axes approach the reference position
of the gantry grouping in the decoupled state.
The reference position of the gantry grouping for referencing the gantry axes corresponds to
the reference position of the leading axis:
MD34100 REFP_SET_POS (reference point value/destination point for distance-coded
system)
Otherwise, the reference position is the current actual position of the leading axis.
These operations for referencing and synchronizing the gantry axes are executed
automatically in accordance with a special flowchart.