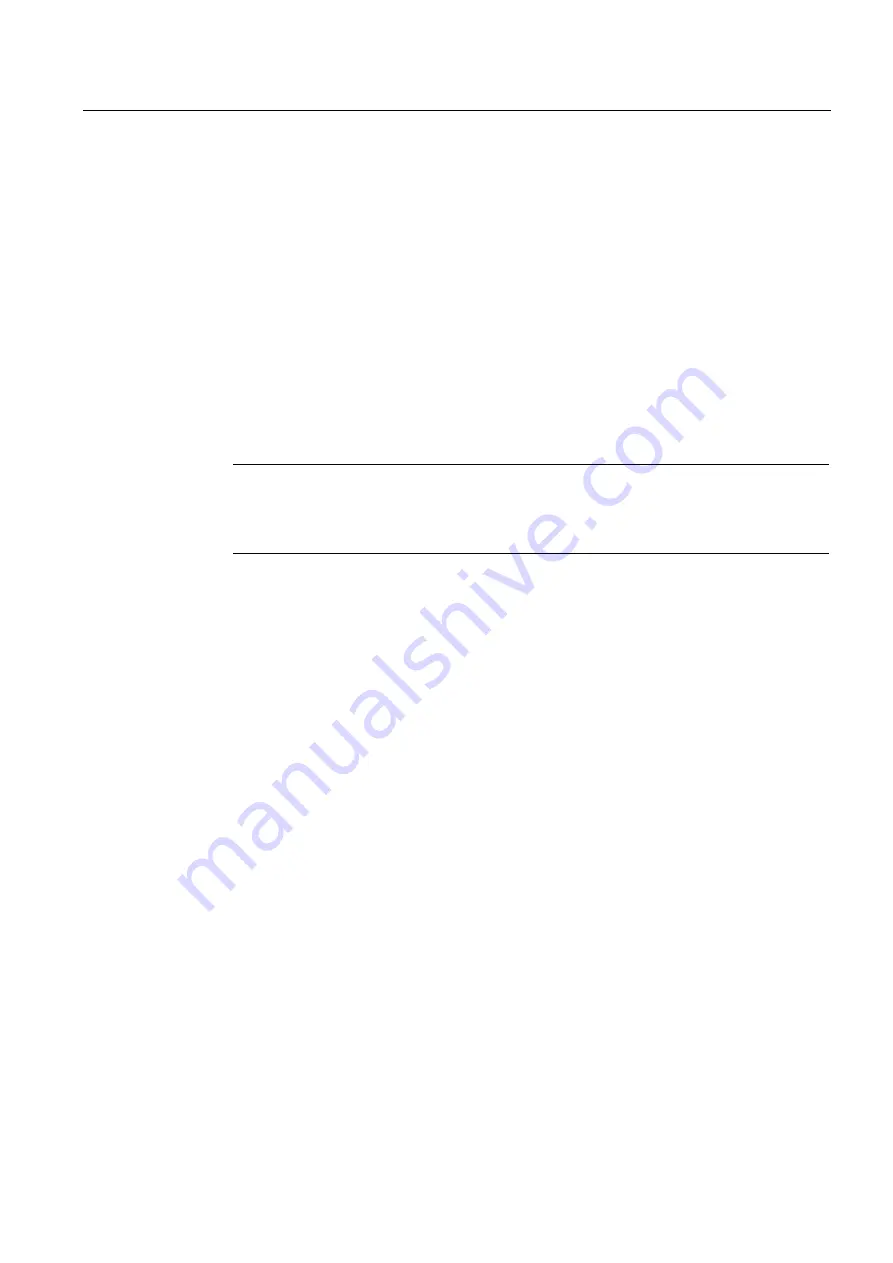
Gantry axes (G1)
6.4 Start-up of gantry axes
Turning, Milling, Nibbling
Function Manual, 11/2012, 6FC5397-1CP10-5BA0
103
If the gantry grouping is canceled, the following points must be noted:
●
Always activate the traversing range limits and set them to the lowest possible values
(position tolerance)
●
Synchronize the gantry grouping first if possible and then execute a POWER-ON-RESET
without referencing the axes again. This ensures that the traversing range limits always
refer to the same position (i.e. that which was valid on power ON).
●
Avoid using the step-change function. Position step changes are only permissible if they
stay within the permitted tolerance.
●
Always use an offset of 0 for the function generator and measuring function in contrast to
the recommendations for normal axes.
●
Set the amplitudes for function generator and measuring function to such low values that
the activated axis traverses a shorter distance than the position tolerance allows. Always
activate the traversing range limits as a check (see above).
Note
As a supplement to the more general description given here of features of start-up and
dynamic control response of drives, a complete example of a concrete constellation
defined on the basis of its machine data can be found in Chapter "Example".
Start-up support for gantry groupings
The commissioning functions of the function generator and measuring functions are
assigned parameters via PI services. All parameterized axes commence traversing when the
NC Start key on the MCP panel is pressed in JOG mode.
A window is displayed in the "Measuring function and function generator in gantry grouping"
operator interface. Two amplitude values, each with an offset and bandwidth, must be
entered in this window. The first amplitude value applies to the measuring axis and the
second to the other coupled axes.