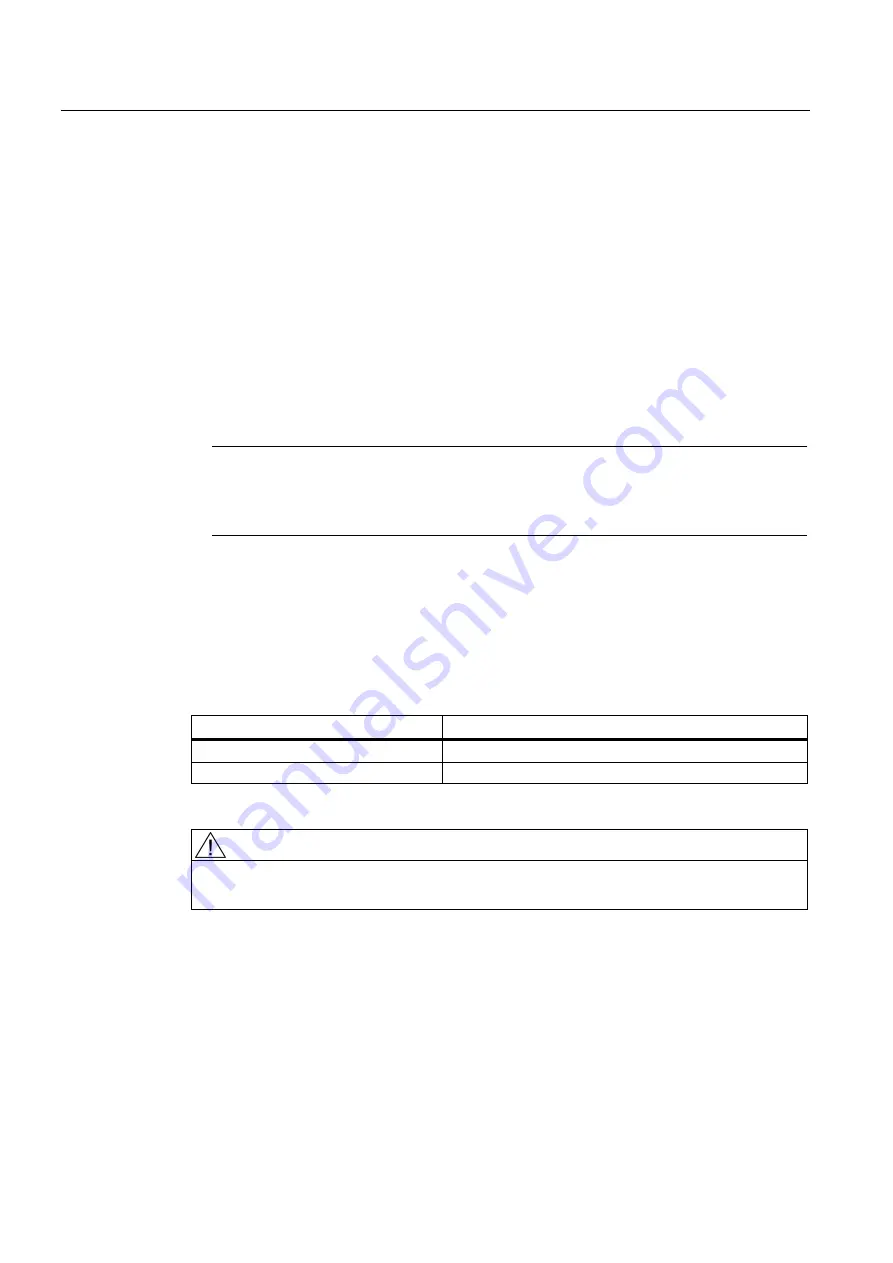
Reference Point Approach (R1)
18.3 Referencing with distancecoded reference markers
Turning, Milling, Nibbling
322
Function Manual, 11/2012, 6FC5397-1CP10-5BA0
Rotary measuring system
For rotary measuring systems, the same applies as for linear measuring systems (see
above).
Determining the absolute offset
The following procedure is recommended for the determination of the absolute offset
between the machine zero point and the position of the first reference mark of a machine
axis:
1.
Enter the value zero for the absolute offset:
MD34090 REFP_MOVE_DIST_CORR = 0
2.
Perform reference point approach.
Note
The reference point should be approached at a point in the machine where the exact
position of the machine axis relative to machine zero can be determined easily (using a
laser interferometer, for example).
3.
Determine the actual position of the machine axis via the operator interface screen.
4.
Measure the current position of the machine axis with reference to the machine zero
point.
5.
Calculate absolute offset and enter in MD34090.
The absolute offset is calculated with respect to the machine coordinate system and
depending on the orientation of the measuring system (equidirectional or inverse) as:
Orientation of the measuring system
Absolute offset
equidirectional
Measured po displayed actual position
Opposite direction
Measured position - displayed actual position
WARNING
After determining the absolute offset and the entry in MD34090, the reference point
traversing for the machine axis must be carried out once more.