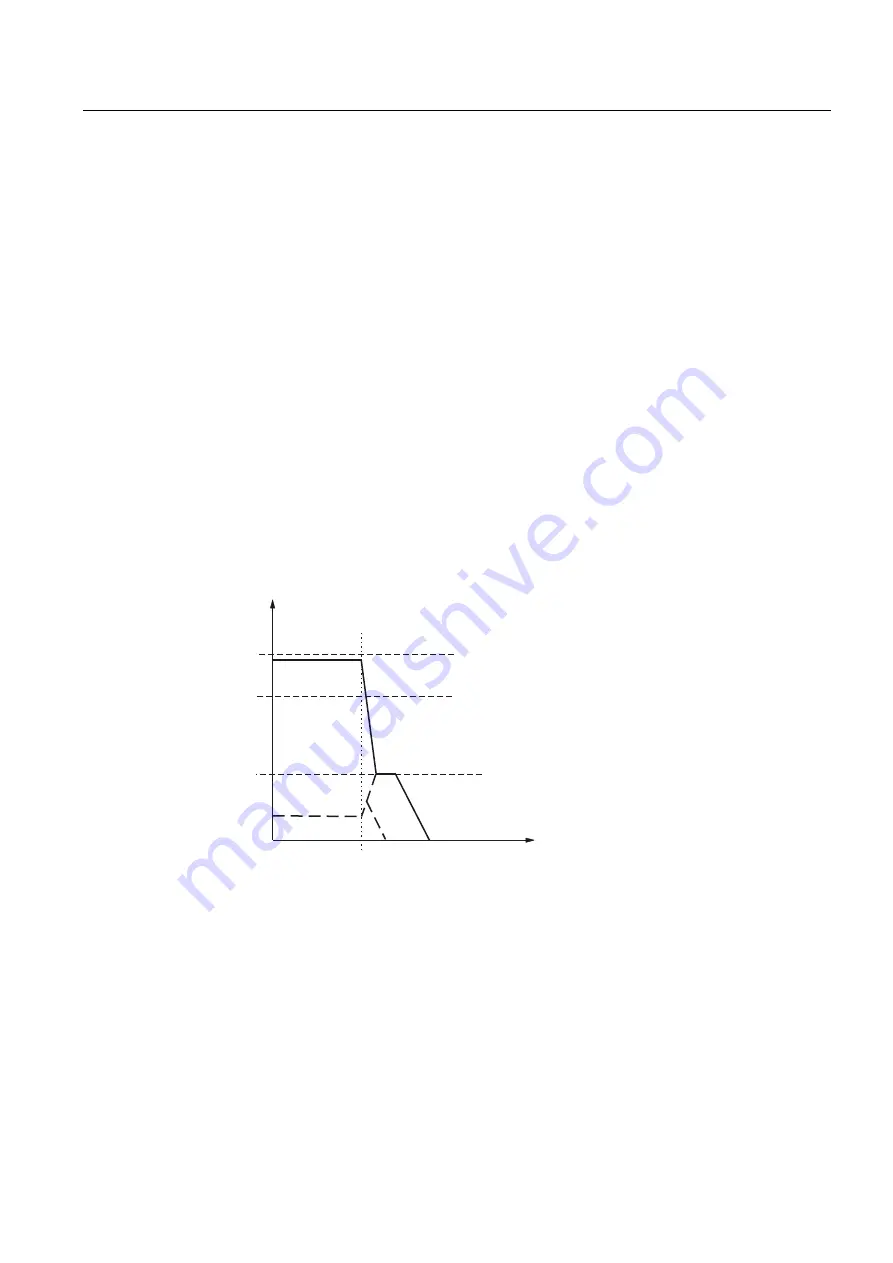
Spindle (S1)
20.2 Spindle modes
Turning, Milling, Nibbling
Function Manual, 11/2012, 6FC5397-1CP10-5BA0
347
20.2.3
Spindle positioning mode
When is positioning mode used?
The spindle positioning mode stops the spindle at the defined position and activates the
position control, which remains active until it is deactivated. With the SPOS =..... program
function, the spindle is in positioning mode (see also Section "Programming").
Block change
The block change is carried out when all functions programmed in the block have reached
their end criterion (e.g. axis traverse completed, all auxiliary functions acknowledged by
PLC) and the spindle has reached its position (IS "Exact stop fine" for spindle (V390x
0000.7)).
Requirements
A spindle position actual value encoder is absolutely essential.
Positioning from rotation
D
D
0'(1&B)5(4B/,0,7B/2:
HQFRGHUOLPLWIUHTXHQF\UHV\QFKURQL]DWLRQ
YDOXHRI0'
3KDVHWR
0'63,1'B326&75/B9(/2
SRVLWLRQFRQWURODFWLYDWLRQVSHHG
6326
0'(1&B)5(4B/,0,7
HQFRGHUOLPLWIUHTXHQF\
7LPHV
6SHHG
UHYPLQ
Figure 20-3 Positioning from rotation at different speeds
Sequence
Phase 1: Spindle rotates at a lower speed than the encoder limit frequency. The spindle is
synchronized. It is set to control mode. Process continues with Phase 2.
Phase 1a: Spindle rotates at a lower speed than the position control activation speed. The
spindle is synchronized. It is set to control mode. The rest of the sequence is possible via 4a.