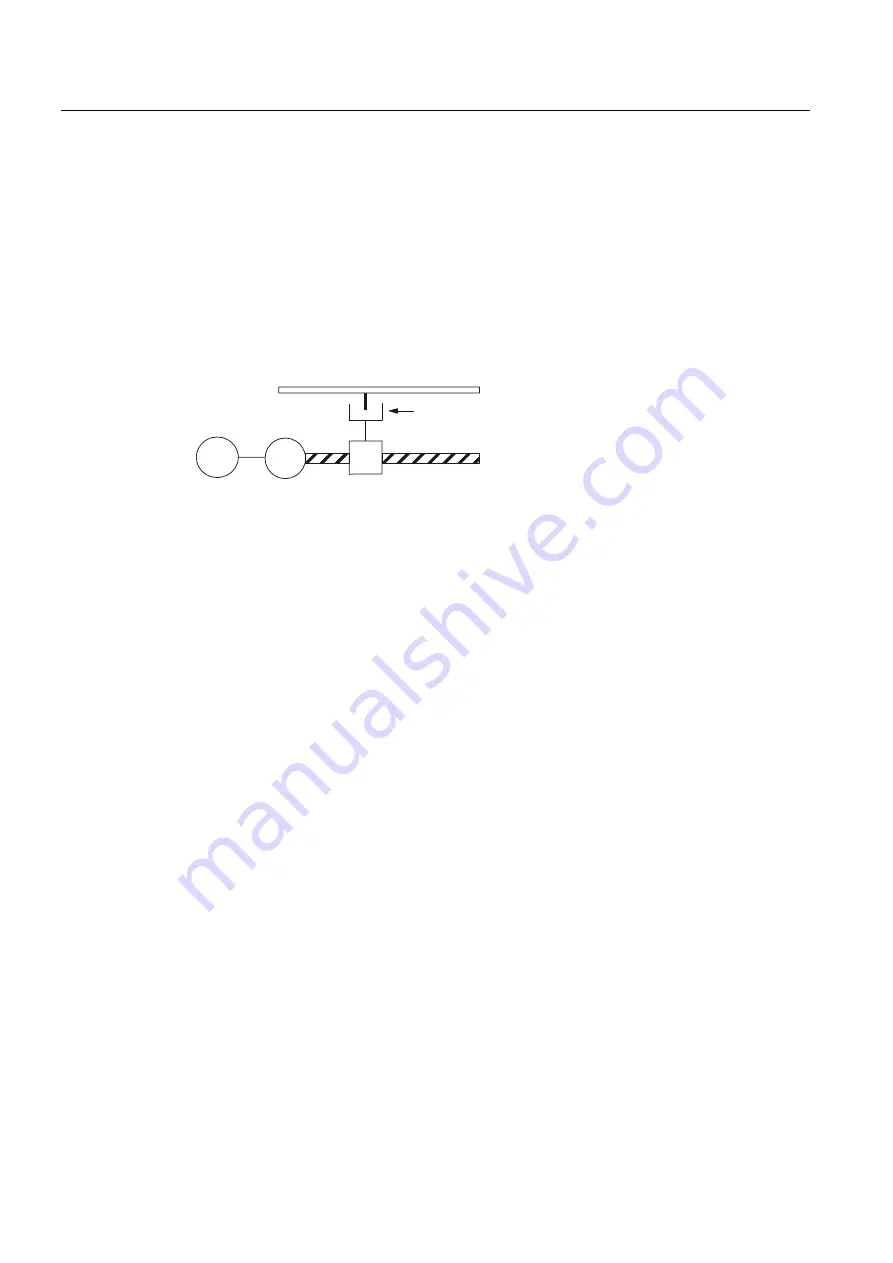
Compensation (K3)
11.2 Backlash compensation
Turning, Milling, Nibbling
208
Function Manual, 11/2012, 6FC5397-1CP10-5BA0
Effectiveness
Backlash compensation is always active in all operating modes after reference point
approach.
Positive backlash
The encoder leads the machine part (e.g. table). Since the actual position acquired by the
encoder also leads the real actual position of the table, the table travels too short a distance
(see diagram below). The backlash compensation value must be entered as a positive value
here (= normal case).
(QFRGHUDFWXDOYDOXHOHDGVWKHUHDODFWXDOYDOXHWDEOH
7KHWDEOHGRHVQRWWUDYHUVHIDUHQRXJK
7DEOH
(QFR
GHU
0
%DFNODVK
Figure 11-1 Positive backlash (normal case)
Negative backlash
The encoder lags behind the machine part (e.g. table); the table then travels too far. The
correction value entered is negative.
High backlash compensation values
The user has the option of applying the backlash compensation value gradually in several
increments when the relevant axis reverses direction. This prevents an excessive setpoint
step change from causing specific axis errors.
The contents of the axis-specific MD36500 ENC_CHANGE_TOL determine the increment
with which the backlash compensation value (MD32450 BACKLASH) is applied. Please note
that the backlash compensation is fully calculated only after n servo cycles
(n=MD32450/MD36500). An excessive time span can cause the triggering of standstill
monitoring alarms. If MD36500 is greater than MD32450, the compensation is performed in
a servo cycle.