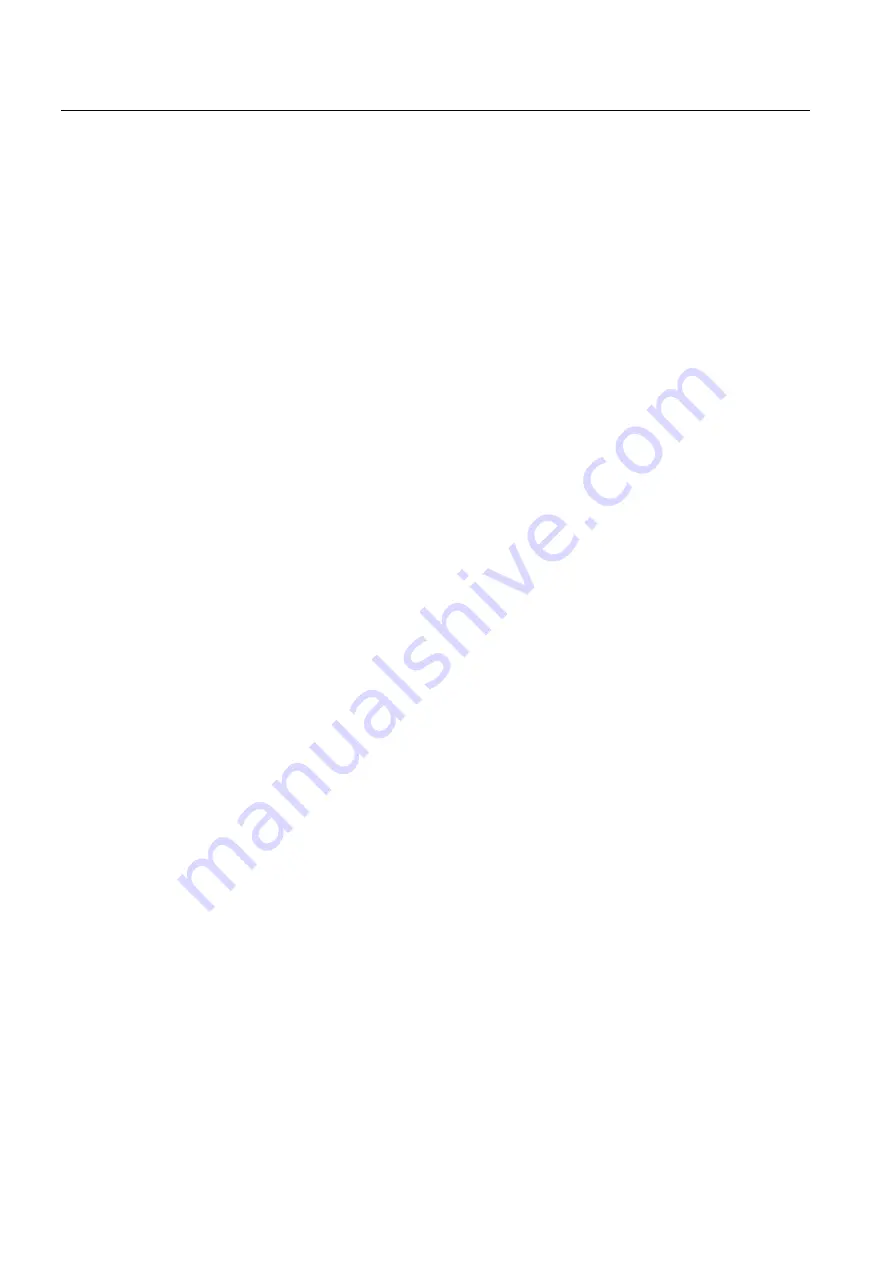
Speed/torque coupling, master-slave (TE3)
23.3 Configuring a coupling
Turning, Milling, Nibbling
394
Function Manual, 11/2012, 6FC5397-1CP10-5BA0
23.3
Configuring a coupling
Static
A master-slave coupling is configured in the slave axis only.
Each slave axis is assigned one master axis for speed setpoint coupling and one for torque
compensation control (default setting).
The assignments done in the following machine data are automatically active in each control
start-up.
MD37252 MS_ASSIGN_MASTER_TORQUE_CTR
MD37250 MS_ASSIGN_MASTER_SPEED_CMD
23.4
Torque compensatory controller
A PI controller calculates a load-side additional speed setpoint from the torque difference
between the master and slave axes. This is applied as standard to the command speed
setpoint in the master and slave axes with different signs in each case.
The torque setpoints used for torque compensation control are smoothed in the drive
(r0079). The smoothing time constant is entered in drive parameter p0045. The same value
should be set in the master and slave axes.
The gain factor MD37256 MS_TORQUE_CTRL_P_GAIN corresponds to the percentage
ratio of the maximum axis velocity MD32000 MAX_AX_VELO to the rated driving torque
(p2003) of the slave axis.
The I component is disabled in the default setting.
The integral time MD37258 MS_TORQUE_CTRL_I_TIME is entered in seconds.
The torque compensation controller output is actively limited to the MD37260
MS_MAX_CTRL_VELO value.
If the following settings are made, the torque compensation controller will be inactive:
●
MD37254 MS_TORQUE_CTRL_MODE = 3
●
MD37256 MS_TORQUE_CTRL_P_GAIN = 0.
The torque distribution can be parameterized via the input variables of the torque
compensatory controller. Weighting of the driving torque values:
●
Slave axis: MD37268 MS_TORQUE_WEIGHT_SLAVE
●
Master axis: 100 - MD37268
If motors with different rated torque values are used, the 50% to 50% standard distribution
must be adapted to suit.
A mechanical coupling is absolutely necessary when the torque compensatory controller is
used. Otherwise, the drives involved could accelerate from standstill.