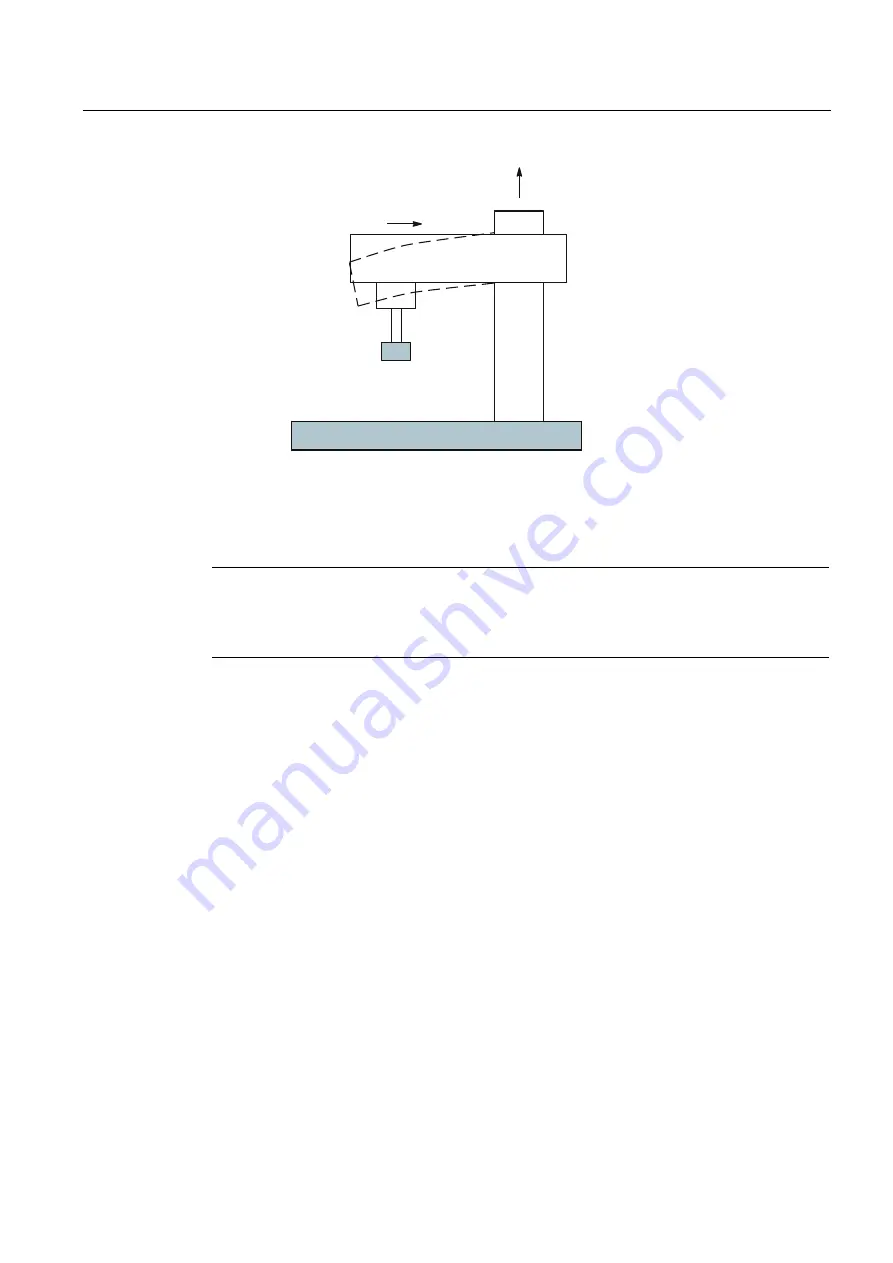
Compensation (K3)
11.3 Interpolatory compensation
Turning, Milling, Nibbling
Function Manual, 11/2012, 6FC5397-1CP10-5BA0
215
6DJLQQHJ<
GLUHFWLRQEHFDXVH
RIVHOIZHLJKW
=
<
Figure 11-4 Example of sag caused by own weight
Depending on the requirement, several compensation relations can be defined for one axis.
The total compensation value results from the sum of all the compensation values of this
axis.
Note
You can read the compensation value that is currently effective on the user interface under
the "Sag/temperature" variable. To do this, select softkey "System" followed by "Service
Display" → "Service Axes".
Setting options
The many ways in which the compensation value for sag compensation can be
produced/influenced are listed below (see diagram below).
1.
An axis can be defined as the input variable (base axis) for several compensation tables
(settable via system variables).
2.
An axis can be defined as the recipient of the output variable (compensation axis) of
several compensation tables (settable via system variable). The total compensation value
is derived from the sum of the individual compensation values.
The following definition applies for the maximum number of possible compensation
tables:
Total maximum number of tables available for all axes: 2
3.
An axis can be both a base axis and a compensation axis at any one time. The
programmed (required) position setpoint is always used to calculate the compensation
values.
4.
The scope of action of the compensation (starting and end position of the base axis) and
the distance between the interpolation points can be defined for every compensation
table (settable via system variables).
5.
Compensation can be direction-dependent (settable via system variables).