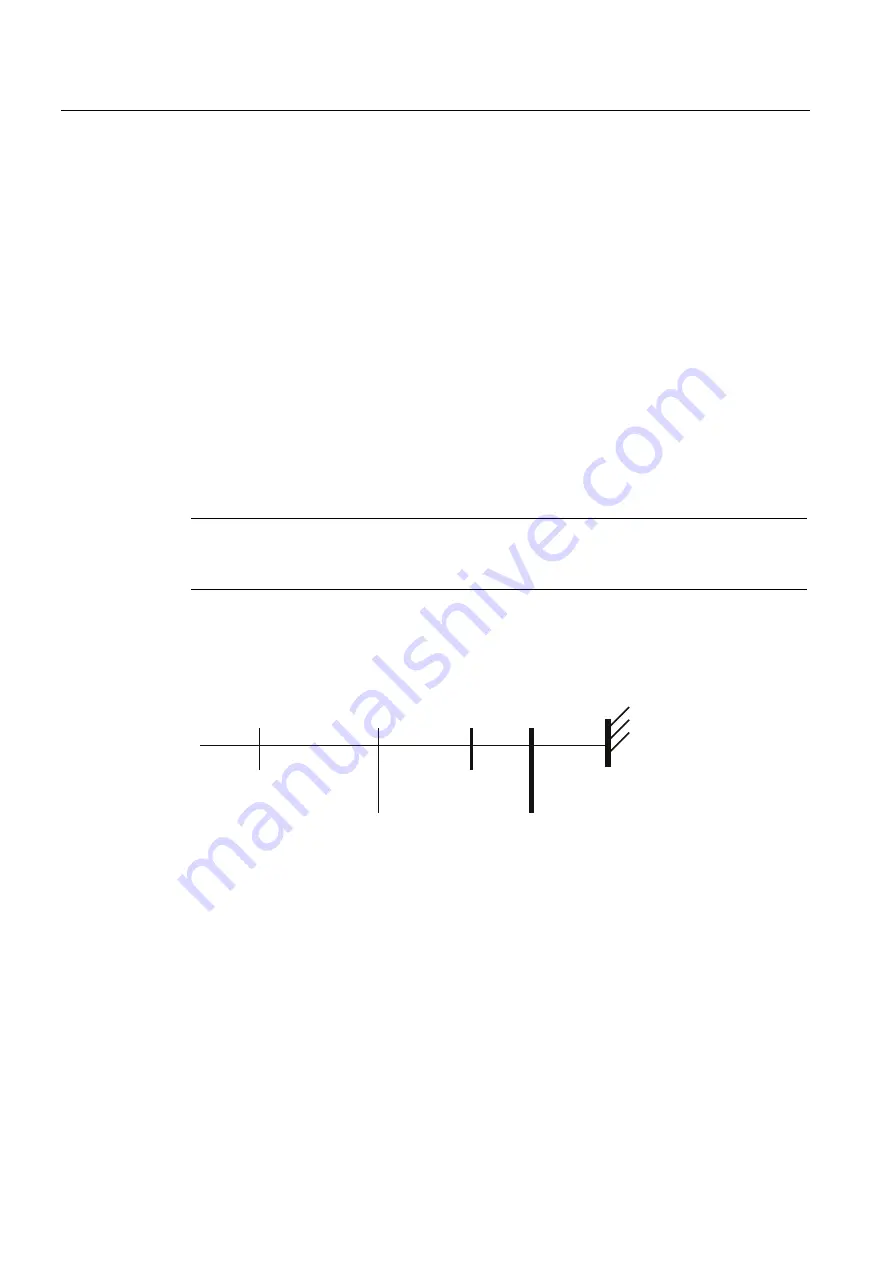
Axis Monitoring (A3)
2.4 Monitoring of static limits
Turning, Milling, Nibbling
50
Function Manual, 11/2012, 6FC5397-1CP10-5BA0
Effect
If the number of zero mark errors entered in MD36310 ENC_ZERO_MONITORING is
reached for a measuring system, alarm 25020 "Zero mark monitoring" is triggered.
The affected axis/spindle is brought to a standstill using a rapid stop (with open position
control loop) along a speed setpoint ramp. The braking ramp duration is specified in
MD36610 AX_EMERGENCY_STOP_TIME.
If the axis is assigned to an interpolatory grouping with other axes, then these are also
braked using a rapid stop with following error reduction (default for partial position setpoint =
0).
Causes of errors
●
MD36300 ENC_FREQ_LIMIT (encoder limit frequency) set too high.
●
Encoder cable damaged.
●
Encoder or encoder electronics defective.
Note
When an error occurs in the measuring circuit, interface signal "Referenced/synchronized 1"
(V390x 0000.4) is cancelled; i.e. the axis must be re-referenced.
2.4
Monitoring of static limits
(0(5*(1&<6723
0HFKDQLFDO
HQGRIWUDYHUVLQJ
UDQJH
+:OLPLWVZLWFK
VW6:OLPLWVZLWFK
QG6:OLPLWVZLWFK
FDQEHDFWLYDWHGYLD3/&
Figure 2-3
Overview of travel limits of a linear axis
2.4.1
Hardware limit switches
Function
Every axis has a hardware limit switch for each traversing direction, which prevents the slide
from moving out of the slide bed.