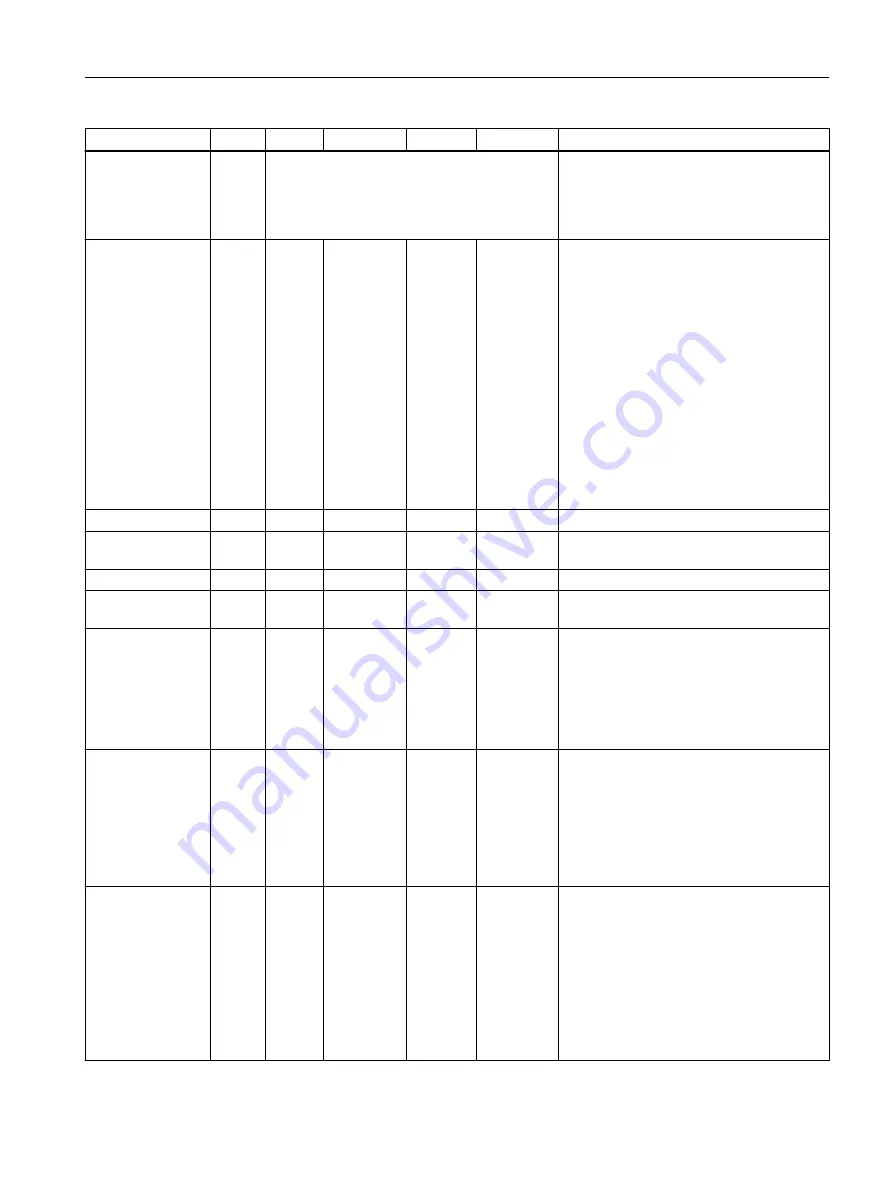
Parameter
ID
Unit
Default
Min
Max
Description
Speed Derate Curve 1151
Submenus define a curve for a quadratic load for
self cooling with the internal fan on the motor.
Use manufacturers data if available.
Set allowable motor load as a function of
speed to tailor the derating curve to the spe‐
cific motor manufacturers data for best pro‐
tection. See Table Speed Derate Curve Menu
(1151).
Maximum Motor
Inertia
1159
Kgm
2
0.0
0.0
500000.0
Set the motor inertia for calculating the mo‐
tor thermal capacity for the inverse time TOL
function. This does not include load inertia.
Entering zero allows the software to esti‐
mate the thermal capacity of the motor as
the default. Use manufacturers data if avail‐
able.
Refer to Appendix NEMA Table for the cor‐
rect value.
This parameter must be non-zero for proper
operation of the inverse time modes if the
motor parameters are outside the supported
range.
This parameter does not apply for Legacy in‐
verse time modes.
Motor trip volts
1160
V
4800
5
20000
Set the motor over-voltage trip point.
Overspeed
1170
%
120.0
0.0
290.0
Set the motor overspeed trip level as a per‐
centage of rated speed.
Underload enable
1180
Disable
Enable or disable underload protection.
I underload
1182
%
10.0
1.0
90.0
Set the current underload level based on the
rated motor current.
Underload timeout 1186
sec
10.0
0.01
900.0
Set the time for underload trip. The time is
cumulative, increasing and decreasing to
measure total time less than the underload
limit. Once the timeout is reached, the drive
will trip. The drive alarms if the current falls
below the threshold, with a half second hys‐
teresis.
Motor torque lim‐
it 1
1190
%
100.0
0.0
300.0
Set the motoring torque limit as a function of
the rated motor current. Torque limit 1
(1190 and 1200) are used as default when
no other torque limits are selected via the
SOP. The magnitude of this torque limit is the
maximum effective magnitude for the re‐
maining torque limits (1200, 1210, 1220,
1230 and 1240).
Regen torque
limit 1
1200
%
-0.25
-300.0
0.0
Set the regenerative torque limit as a func‐
tion of rated motor current at full speed. The
limit is allowed to increase inversely with
speed for a two quadrant drive.
Note: For drives with film capacitors (i.e. wa‐
ter-cooled Type 6SR325), change the setting
to -0.15 %. These cells have less losses and
failure to make this change could result in an
over voltage trip during deceleration of the
drive.
Parameter Assignment/Addressing
6.3 Options for Motor Menu (1) - first half
Control Manual
Operating Manual, A5E50491925A
93
Summary of Contents for SINAMICS PERFECT HARMONY GH180
Page 2: ......
Page 22: ...Table of contents NXGPro Control Manual 20 Operating Manual A5E50491925A ...
Page 24: ...Security NXGPro Control Manual 22 Operating Manual A5E50491925A ...
Page 504: ...NEMA Table NXGPro Control Manual 502 Operating Manual A5E50491925A ...
Page 517: ...Index D NXGPro Control Manual Operating Manual A5E50491925A 515 ...
Page 518: ...Index NXGPro Control Manual 516 Operating Manual A5E50491925A ...
Page 530: ...Glossary NXGPro Control Manual 528 Operating Manual A5E50491925A ...
Page 537: ......