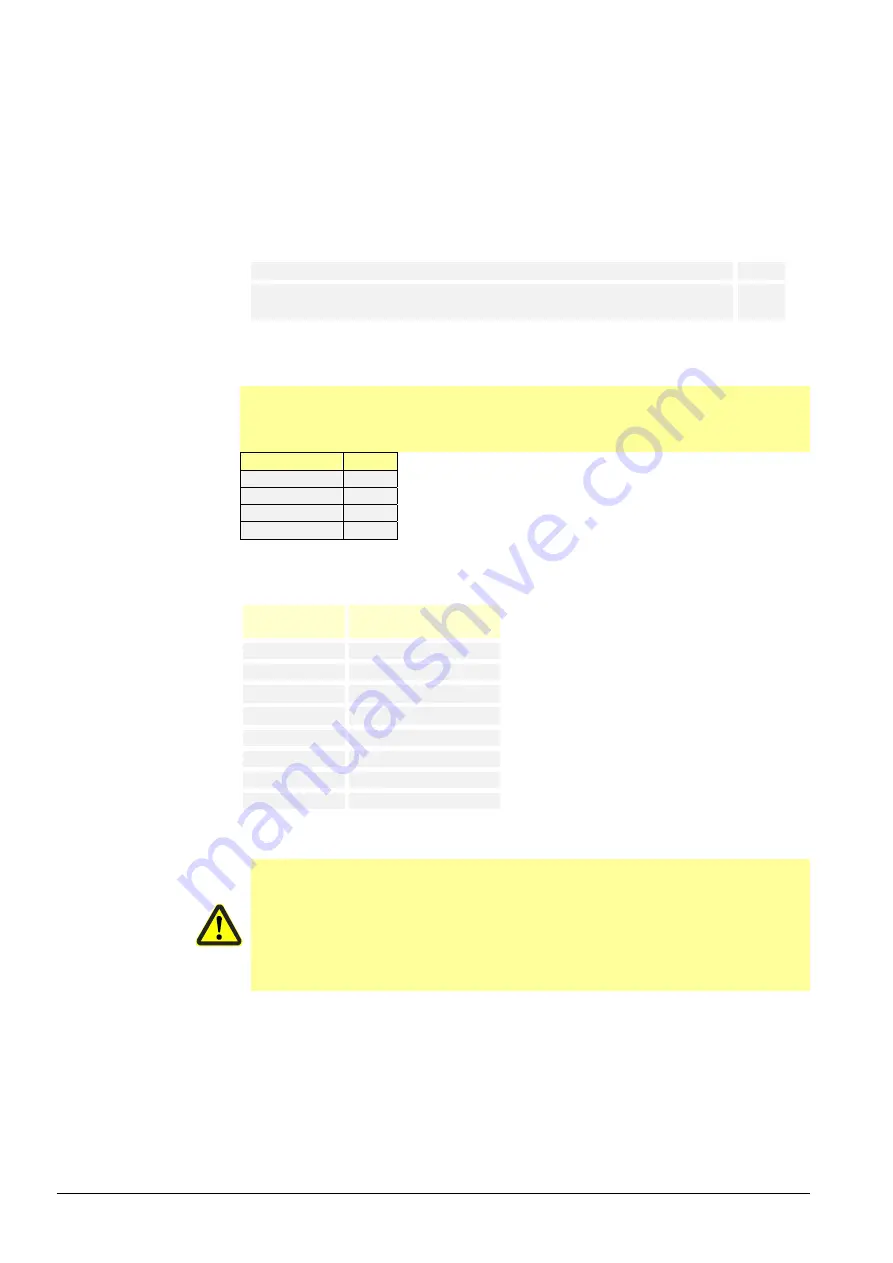
104/219
Building Technologies
Basic Documentation LMV27...
CC1P7541en
11 Actuators X53 / X54
17.12.2018
11.5 Monitoring the actuator positions
To monitor the actuator’s current positions, an optical incremental transducer with a
resolution of 0.7° is used. The correct position of the drive shaft is ensured by
comparing the motor steps made with the position obtained from the incremental
transducer. Due to the different resolutions of motor steps and incremental transducer
plus the selected tolerance band, the following error detection band is obtained. The
position where – in the error detection band – shutdown takes place depends on the
position currently required.
For the default setting made in the factory, the error detection band is as follows:
Smallest position error where an error can be detected
1,1°
Greatest position error where an error is securely detected (default setting
parameter 606)
1,7°
The presetting of 1.7° (default setting, parameter 606) is suited for use with actuators
type SQN1 and SQM3.
Note
When using SQN1 actuators equipped with plastic gear trains, we recommend to
change the preset values as follows:
Product no.
Value
SQN13.14
1.7°
SQN14.14
1.7°
SQN13.17
2.2°
SQN14.17
2.2°
When referencing under output conditions, the resilience of the actuator’s gear train
must also be taken into consideration:
Product no.
Resilience at max.
rated driving torque
SQM33.41
0.2°
SQM33.51
0.2°
SQM33.6
0.2°
SQM33.7
0.2°
SQN13.14
0.3°
SQN13.17
0.8°
SQN14.14
0.3°
SQN14.17
0.8°
The error detection time is <1 second.
Caution!
This means that – for the design and setting of the burner – a position error
resulting from the sum of …
-
greatest position error from which an error is detected in all positions,
-
resilience at the max. rated torque, and
-
mechanical influence from the link between actuator and regulating unit
(e.g. coupling)
must not lead to a critical state in terms of safety.