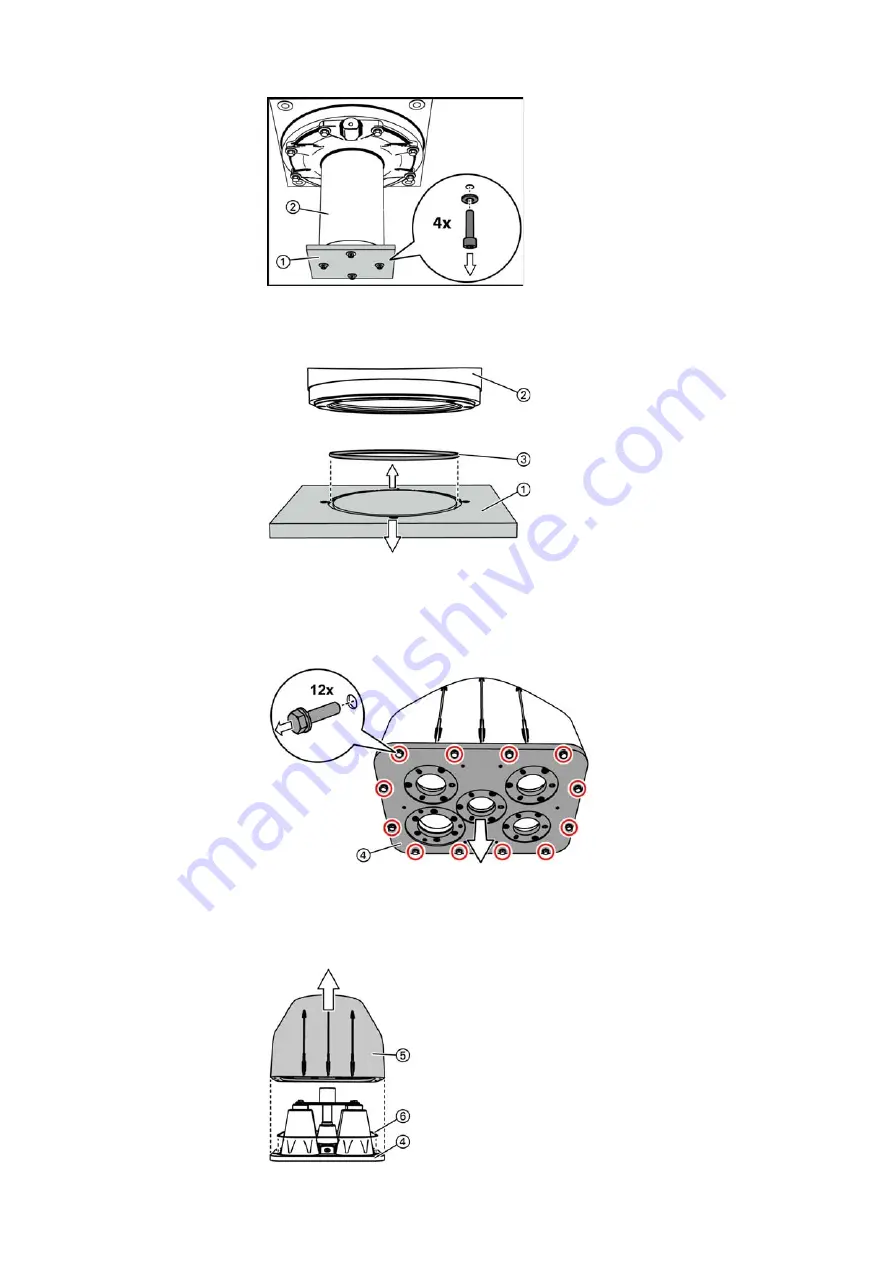
Installation
98/214
Revision 11 • INSTALLATION AND OPERATING INSTRUCTIONS • 8DA10 • 861-9601.9
➭ Remove the cover of the transformer housing ① and the sealing ring ③ .
➭ Undo 12 bolt-and-washer assemblies M8x40 at the cover of the panel connection
housing ④ .
➭ Remove the panel connection housing ⑤ .
➭ Take the sealing ring ⑥ out of the groove in the cover of the panel connection housing.
Fig. 110: Removing the cover of the transformer housing
①
Transformer housing
②
Cover of transformer housing
Fig. 111: Removing the cover of the transformer housing and
the sealing ring
①
Cover of transformer housing
②
Transformer housing
③
Sealing ring (O-ring)
Fig. 112: Removing the cover with the plug sockets
④
Cover of panel connection housing
Fig. 113: Removing the panel connection housing
④
Cover of panel connection housing
⑤
Panel connection housing
⑥
Sealing ring