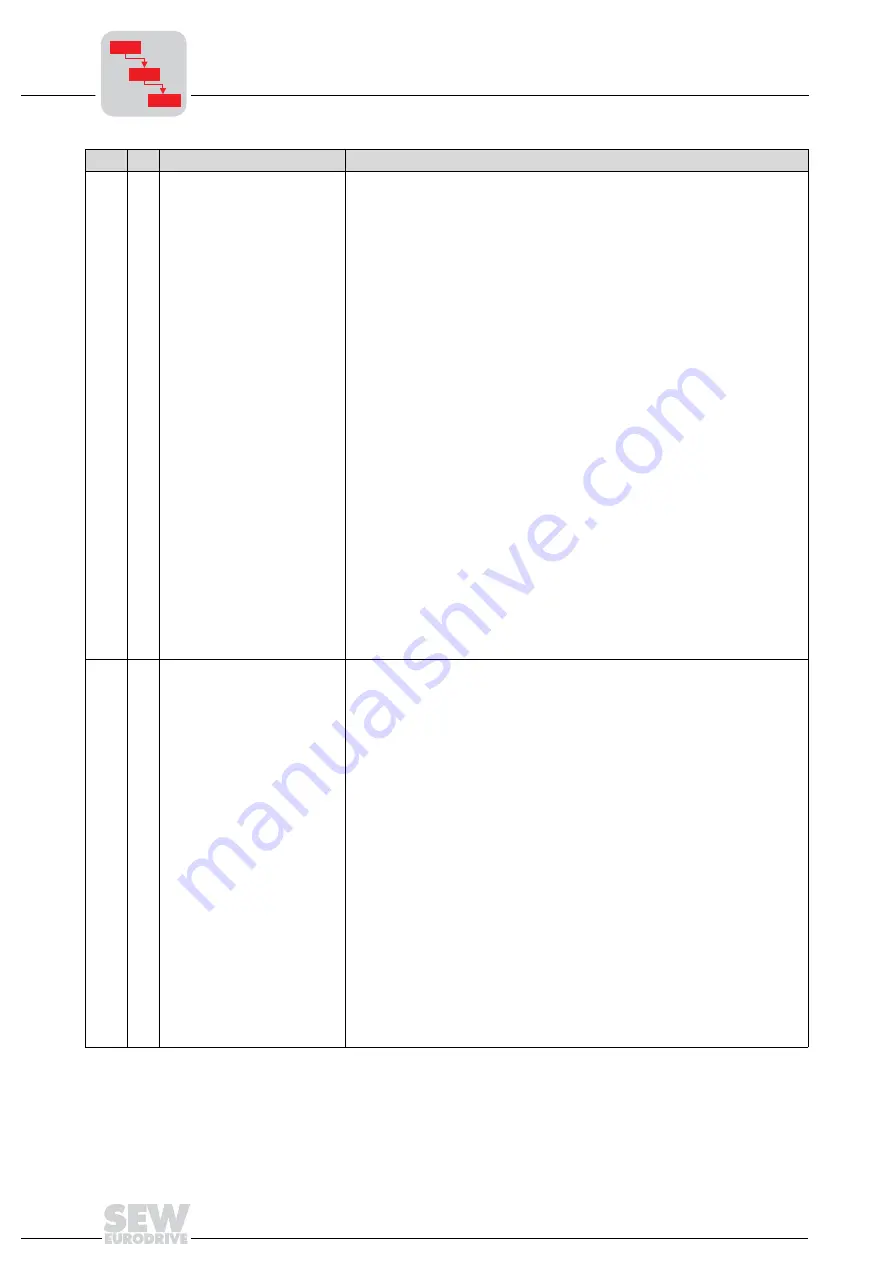
4
68
System Manual – MOVITRAC® 07
Explanation of the parameters
Parameters
100
•
Setpoint source
1 / UNIPOL/FIX.SETPT
The setpoint is provided by the analog inputs or the fixed setpoints. The
unit processes the fixed setpoints according to their value. The binary
inputs specify the direction of rotation.
2 / RS485
Only for service purposes! The setpoint comes from the RS-485 inter-
face. The +/- character of the setpoint determines the direction of rota-
tion.
4 / MOTOR POT
Set the setpoint using appropriately programmed terminals
Motor pot.
up and Motor pot. down. This motor potentiometer is a virtual potentiom-
eter and does not correspond to the setpoint potentiometer on the unit.
6 / FIX SETP+AI1
The setpoint is calculated by adding together the selected fixed setpoint
and analog input AI1. The binary inputs specify the direction of rotation.
Furthermore,
P112 AI1 operation mode applies.
7 / FIX SETP*AI1
The value at analog input AI1 serves as the evaluation factor for the
selected fixed setpoint (0 ... 10 V = 0 ... 100 %). n
min
is in effect if no
fixed setpoint is selected. The binary inputs specify the direction of rota-
tion.
10 / SBus
The system bus specifies the setpoint. The +/- character of the setpoint
determines the direction of rotation.
11 / FREQUENCY INPUT (in preparation, only in units with expanded func-
tions or LOGODrive units)
The frequency at binary input DI01 specifies the setpoint. The value is
set using parameter
P102 Frequency scaling. You can influence the
value with
P110 AI1 scaling. The following parameters are included in
the scaling if the PI-controller is activated:
•
P254 PI actual value scaling
•
P255 PI sensor offset
101
•
Control signal source
0 / TERMINALS
The binary inputs determine the control.
1 / RS485
Only for service purposes! The RS-485 interface and the binary inputs
determine the control.
3 / SBus
The system bus and the binary inputs determine the control.
4 / 3-WIRE-CONTROL
The 3-wire control principle determines the control.
In this case, the enable and direction of rotation signals of the inverter
react using edge control.
•
Connect the CW start button to the NO contact on the "CW/STOP"
binary input.
•
Connect the CCW start button to the NO contact on the
"CCW/STOP" binary input.
•
Connect the stop button to the "Enable/rapid stop" NC input.
If you connect CW and CCW at the same time, the drive decelerates
with downwards ramp P131.
If the
3-WIRE-CONTROL control signal source is active and the drive is
started by a start edge: You can stop the drive using the STOP button
when the RUN/STOP buttons are enabled. Then you can restart the
drive with the RUN button without another start edge being required.
The unit stores a start edge if you stop the drive with the stop button.
The unit enables the drive immediately if you then press the RUN but-
ton.
No.
OP Name
Description
P6..
P60.
P600