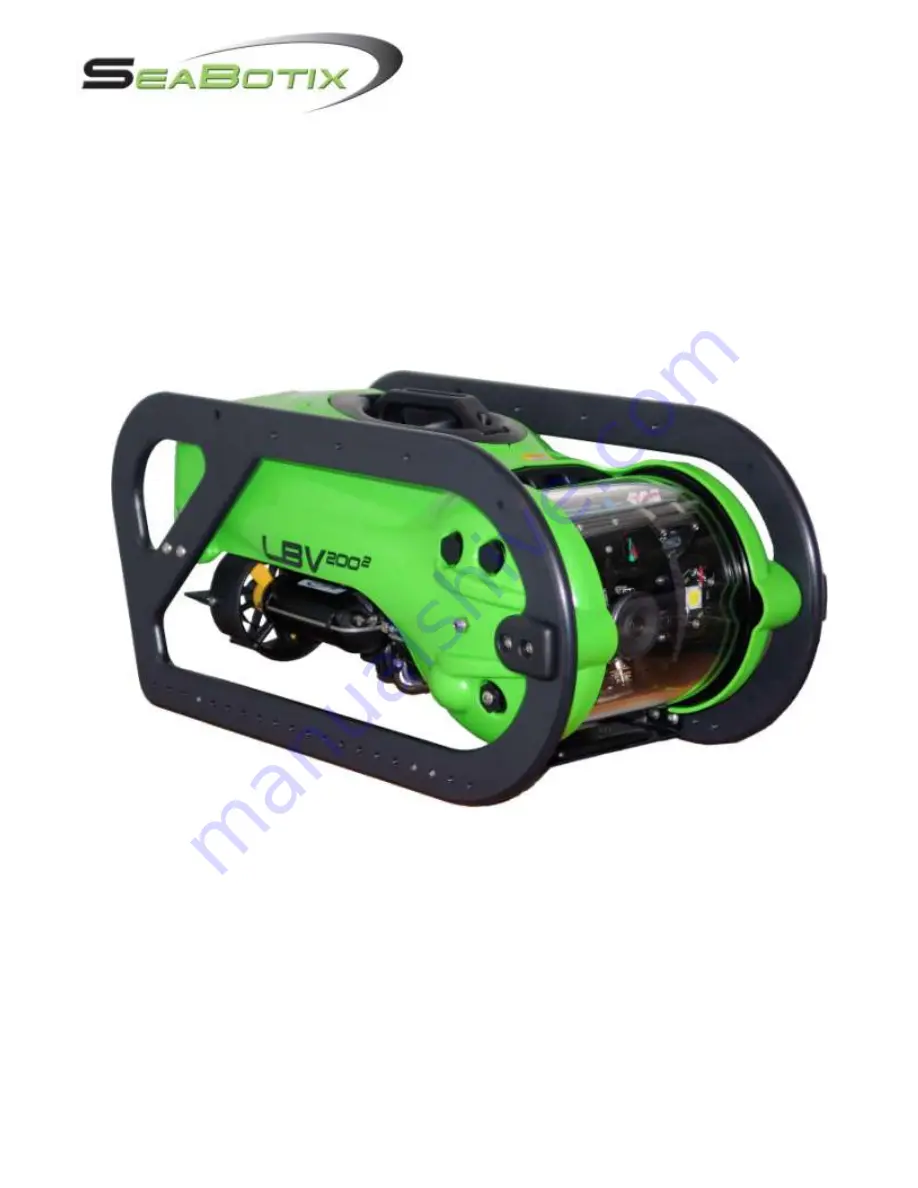
Head Office
: SeaBotix Inc., 2877 Historic Decatur Road STE 100, San Diego, CA 92106 USA +1 (619) 450-4000
Australia Office
: SeaBotix Inc. Australia Pty Ltd.8A Sparks Road, Henderson, WA 6166, Aus61 (0)8 9437-5400
© 2009 by SeaBotix, Inc. All Rights Reserved
LBV200
2
Operators Manual
DOCS-010
Rev B
The information, photographs, illustrations and descriptions contained in this manual are the
property of SeaBotix Inc. Unauthorized duplication and distribution is strictly forbidden.
Additionally, SeaBotix Inc. reserves the right to alter any and all information contained in this
manual.