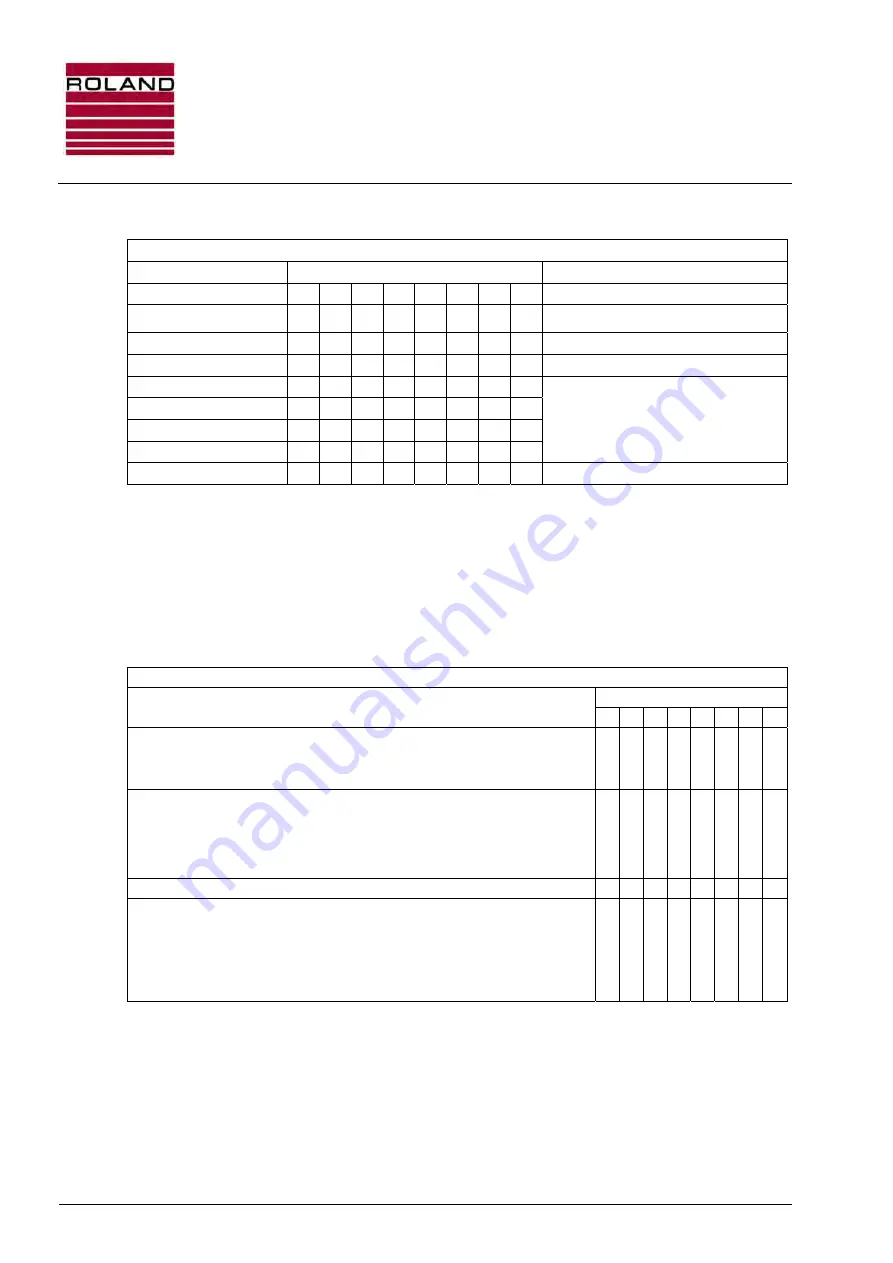
Manual
Double Sheet Detector R1000 series E20
with integrated fieldbus interface
Communication with the PLC
B0046191 / Rev. 1.12
90
ROLAND ELECTRONIC GmbH · Otto-Maurer-Str. 17 · DE 75210 Keltern · Phone +49 (0)7236-9392-0 · Fax +49 (0)7236-9392-33
6.4.1
Structure of the parameter channel
Structure of the parameter channel
Meaning I/O
Byte
Notes
Byte
0 1 2 3 4 5 6 7
Management
x
Data access control
(reading, writing, handshake)
Program index
x
Selection of the tooling program
Parameter index
x
Selection of the parameter
Application data byte 0
x
MSB (most significant byte)
LSB (least significant byte)
Application data byte 1
x
Application data byte 2
x
Application data byte 3
x
Checksum
x
Checksum of the transferred bytes 1 - 6
Data access control
Services are initiated exclusively by the master. The R1000 as slave cannot initiate data
transmissions.
The management byte (E0) is used by the master to select the service (for example writing or
reading) and to confirm the access. The R1000 confirms via the management myte (A0) the
execution of the command. If an access is not allowed and therefore, the service cannot be
executed, then the R1000 declares this action a collision.
Structure of management byte
Management byte (I0/O0)
Bit
7
6 5 4 3 2 1
0
Collision
0 = access correct, 1 = access not correct."
"1"" is set by the R1000 only if a service is inadmissible or cannot be executed. In
this case the master has to take the service back, in order to reset the error
condition. See section "reset faulty access" in this chapter.
x
Handshake
This condition is changed with each new command. Only the master
controls, if a new order from the R1000 has to be executed. The R1000 mirrors that
handshake as soon as the order has been processed. If the order could be
executed, the collision bit remains set to 0. If the order could not be executed, then
the collision bit is set to 1 by the R1000. Additional orders can be executed only by
cancelling the incorrect service.
x
Application data length
always set to 11 (11 = 4 byte)
x
x
Service selection
0000 = Empty service
0001 = Read parameter
0010 = Write parameter
0100 = Open parameter channel
1000 = Close parameter channel
00000000 = Reset parameter channel
x
x
x
x