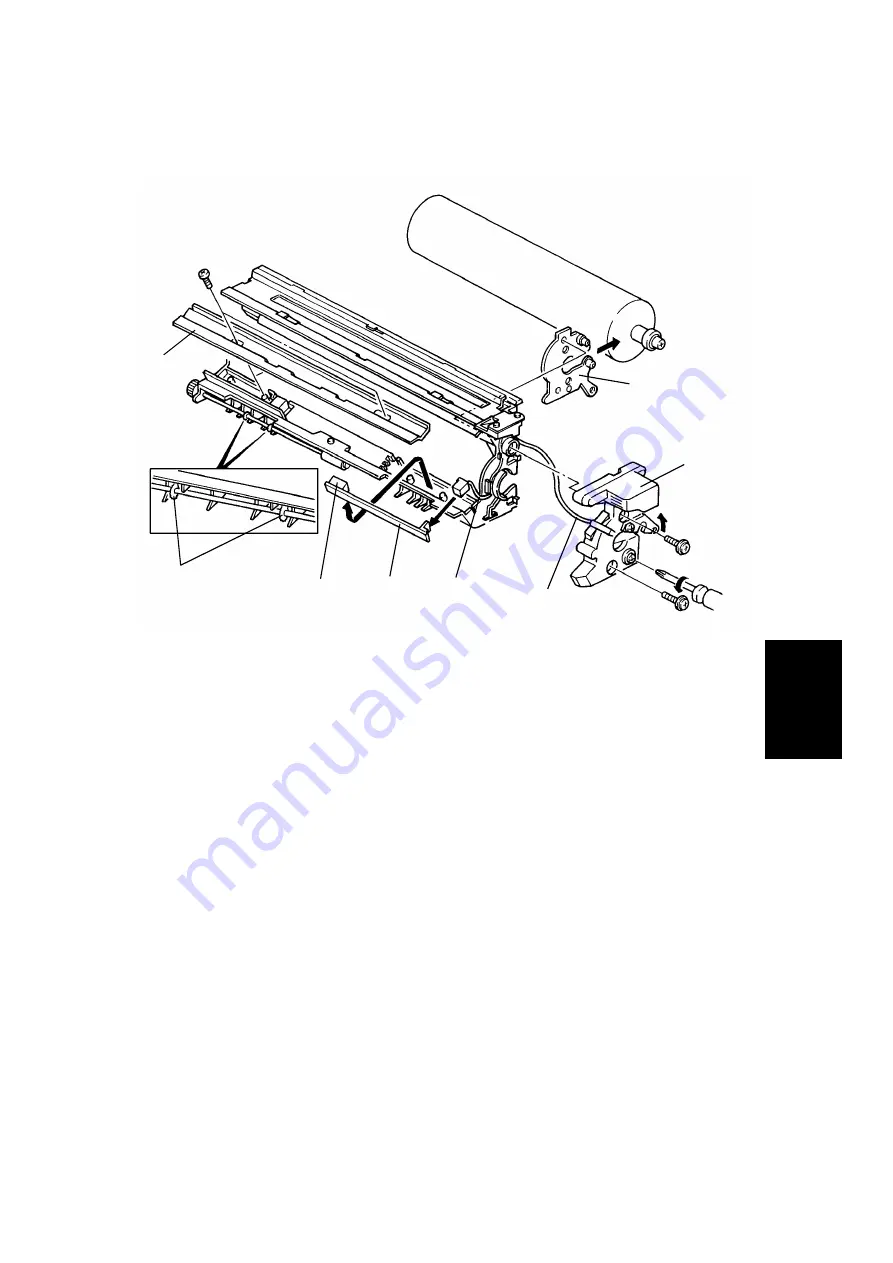
6.5
V SENSOR CLEANING AND REPLACEMENT
1. Remove the drum from the drum unit (see Drum Replacement) and keep
the drum wrapped in the protective sheet or a clean sheet of paper.
[Cleaning]
2. Clean the V sensor [A] with a blower brush from the drum side.
[Replacement]
2. Remove the ID/V sensor bracket [B] from the drum unit (2 screws).
3. Remove the drum stay [C] (2 long screws) from the drum unit.
4. Remove the front drum cover [D] from the unit.
5. Remove the V sensor board [E] from the drum unit (1 connector).
6. Couple the V sensor connector with a new V sensor board and install the
board on the drum unit.
[C]
[D]
[G]
[F]
[E]
[A]
[H]
[B]
Replacem
ent
Adjustm
ent
12 February 1992
AROUND THE DRUM
5-55
Summary of Contents for A085
Page 3: ...FT4227 FT4427 FT4727 A085 A087 A088 ...
Page 6: ...3 LOCATION OF UNIT ...
Page 7: ...4 LOCATION OF UNIT ...
Page 8: ...5 LOCATION OF UNIT ...
Page 9: ...6 LOCATION OF UNIT ...
Page 10: ...7 LOCATION OF UNIT ...
Page 11: ...8 LOCATION OF UNIT ...
Page 12: ...9 LOCATION OF UNIT ...
Page 13: ...10 1 EXTERIOR 1 A085 A087 A088 ...
Page 15: ...12 2 EXTERIOR 2 A085 A087 A088 ...
Page 17: ...14 3 OPERATION PANEL A085 A087 A088 ...
Page 19: ...16 4 PLATEN COVER A085 A087 A088 ...
Page 21: ...18 5 OPTICS SECTION 1 A085 A087 A088 ...
Page 23: ...20 6 OPTICS SECTION 2 A085 A087 A088 ...
Page 25: ...22 7 OPTICS SECTION 3 A085 A087 A088 ...
Page 27: ...24 8 OPTICS SECTION 4 A085 A087 A088 ...
Page 29: ...26 9 OPTICS SECTION 5 A085 A087 A088 ...
Page 31: ...28 10 BY PASS FEED TABLE A085 A087 A088 ...
Page 33: ...30 11 PAPER FEED TRAY A085 A087 A088 ...
Page 35: ...32 12 PAPER FEED SECTION A085 A087 A088 ...
Page 37: ...34 13 TRAY LIFT SECTION A085 A087 A088 ...
Page 39: ...36 14 LCT SECTION 1 A087 A088 ...
Page 41: ...38 15 LCT SECTION 2 A087 A088 ...
Page 43: ...40 16 LCT SECTION 3 A087 A088 ...
Page 45: ...42 17 VERTICAL TRANSPORT SECTION A085 A087 A088 ...
Page 47: ...44 18 PAPER REGISTRATION A085 A087 A088 ...
Page 49: ...46 19 DRUM SECTION 1 A085 A087 A088 ...
Page 51: ...48 20 DRUM SECTION 2 A085 A087 A088 ...
Page 53: ...50 21 DEVELOPMENT UNIT 1 A085 A087 A088 ...
Page 55: ...52 22 DEVELOPMENT UNIT 2 A085 A087 A088 ...
Page 57: ...54 23 CLEANING UNIT A085 A087 A088 ...
Page 59: ...56 24 T S CORONA UNIT A085 A087 A088 ...
Page 61: ...58 25 TRANSPORT SECTION A085 A087 A088 ...
Page 63: ...60 26 FUSING UNIT 1 A085 A087 A088 ...
Page 65: ...62 27 FUSING UNIT 2 A085 A087 A088 ...
Page 67: ...64 28 PAPER EXIT SECTION 1 A085 A087 A088 ...
Page 69: ...66 29 PAPER EXIT SECTION 2 A085 A087 A088 ...
Page 71: ...68 30 FRAME SECTION 1 A085 A087 A088 ...
Page 73: ...70 31 FRAME SECTION 2 A085 A087 A088 ...
Page 75: ...72 32 FRAME SECTION 3 A085 A087 A088 ...
Page 77: ...74 33 FRAME SECTION 4 A085 A087 A088 ...
Page 79: ...76 34 DRIVE SECTION 1 A085 A087 A088 ...
Page 81: ...78 35 DRIVE SECTION 2 A085 A087 A088 ...
Page 83: ...80 36 ELECTRICAL SECTION 1 A085 A087 A088 ...
Page 85: ...82 37 ELECTRICAL SECTION 2 A085 A087 A088 ...
Page 87: ...84 38 ELECTRICAL SECTION 3 A085 A087 A088 ...
Page 89: ...86 39 ELECTRICAL SECTION 4 A085 A087 A088 ...
Page 91: ...88 40 DUPLEX UNIT 1 A088 ...
Page 93: ...90 41 DUPLEX UNIT 2 A088 ...
Page 95: ...92 42 DUPLEX UNIT 3 A088 ...
Page 97: ...94 43 MAIN CONTROL BOARD A085 A087 A088 ...
Page 98: ...95 43 MAIN CONTROL BOARD A085 A087 A088 ...
Page 99: ...96 43 MAIN CONTROL BOARD A085 A087 A088 ...
Page 102: ...99 44 MEMORY BOARD A085 A087 A088 ...
Page 104: ...101 45 AC HARNESS A085 A087 A088 ...
Page 106: ...103 46 DC HARNESS TYPE 2 A085 A087 A088 ...
Page 108: ...105 47 DC HARNESS TYPE 4 A085 A087 A088 ...
Page 110: ...107 48 FUSING UNIT HARNESS A085 A087 A088 ...
Page 112: ...109 49 LCT HARNESS A087 A088 ...
Page 114: ...111 50 DECAL AND DOCUMENT A085 A087 A088 ...
Page 115: ...112 50 DECAL AND DOCUMENT A085 A087 A088 ...
Page 116: ...113 50 DECAL AND DOCUMENT A085 A087 A088 ...
Page 117: ...114 50 DECAL AND DOCUMENT A085 A087 A088 ...
Page 118: ...115 50 DECAL AND DOCUMENT A085 A087 A088 ...
Page 120: ...117 51 SPECIAL TOOL A085 A087 A088 ...
Page 122: ...PARTS INDEX ...
Page 154: ...SECTION 1 OVERALL MACHINE INFORMATION ...
Page 163: ...SECTION 2 DETAILED SECTION DESCRIPTION ...
Page 165: ...SECTION 3 INSTALLATION ...
Page 178: ...SECTION 4 SERVICE TABLES ...
Page 201: ...SECTION 5 REPLACEMENT AND ADJUSTMENT ...
Page 227: ...FT5233 5433 5733 SERVICE MANUAL ...
Page 230: ...SECTION 1 OVERALL MACHINE INFORMATION ...
Page 255: ...SECTION 2 DETAILED SECTION DESCRIPTIONS ...
Page 373: ...SECTION 3 INSTALLATION ...
Page 403: ...SECTION 4 SERVICE TABLES ...
Page 449: ... 6 Duplex Tray PREVENTIVE MAINTENANCE SCHEDULE 12 February 1992 4 46 ...
Page 456: ...SECTION 5 REPLACEMENT AND ADJUSTMENT ...
Page 575: ...SECTION 6 TROUBLESHOOTING ...